Understanding ceramic and glass decorating - Techniques
In part two of our coverage of printing onto glass and ceramic, FESPA UK’s Peter Kiddell explores the techniques and latest technologies used to decorate them.
When screen-printing companies decide to expand their product offerings, an area that many explore is the market for decorated glass and ceramic products.
However, lack of familiarity with the methods and materials used in glass and ceramic printing usually steers all but the most adventurous printers away from such work.
Whether you are decorating glass or ceramic the printing techniques used are very similar all aim to achieve the adhesion of pigment to the surface and have that pigment maintains its colour or performance over the required time period.
No different to any other application but the operating conditions of printed glass and ceramics can be extremely challenging.
Total Transfer Process
When printing directly onto glass and ceramics, screen printing and pad printing can be used. There is a combination of both processes called “Total Transfer.”
This is where the image is screen printed onto a flat plate and then picked off by a silicone pad and transferred to the article. The decorated product is then fired in the normal way.
The reason for using this process is to enable relatively thick deposits of ink to be printed with the pad-printing process, as shown in the picture below.
Image courtesy of PDS International Limited
Pad Printing with Thermoplastic Inks
Pad printing with heated plates and thermoplastic inks works very well but there are pros and cons for both systems. Four colour process is possible with inorganic Cyan, Magenta, Process Yellow and Process Black.
This is not for the inexperienced as colours can easily change in the printing and firing process. You don’t have the benefit of colour bars, greyscales or density measurement as the printed colours change during the firing process and you can’t guillotine off the colour bars.
The simpler alternative to direct printing with ceramic colour is to produce waterslide or heat applied transfers. These transfers are produced by screen printing and lithographic printing. Waterslide use water soluble glue that allows the image to lift off special paper before being positioned on the substrate.
Heat applied transfers come off the carrier paper or film when applied with a heated blanket to the substrate. In both cases the applied image has to be fired at elevated temperatures.
Sublimation
None of these methods should be confused with sublimation transfers that appear to print onto ceramics and glass but are in fact producing an image in a polyester lacquer that has been sprayed or dip coated on to the surface.
Although very attractive this is not as resistant as fired enamels or even UV cured inks. Sublimation inks are not particularly colour safe in sunlight or elevated temperatures but it is still a big market particularly in personalisation and business gifts.
Developments in the dyes and application methods are increasing the use of the process which is ideally suited for the use of digital printing in the creation of the transfers.
In summary the options are:
- Inorganic ink that can be screen printed or pad printed but requires a kiln or lehr to fuse the enamel to the surface.
- Organic ink that can be screen printed or pad printed that requires heat or Ultra Violet energy to cure. If the curing methods is heat then the maximum temperature will be in the region of 180oC for a period of time.
- Waterslide or heat applied transfers printed with inorganic ink that have to be fired in a kiln or lehr.
- Sublimation systems are an ideal means of decorating a huge range of polyester objects and substrates.
Production of Transfers
If you don’t have the kiln or lehr, as a screen printer, the production of transfers can still be a very good business. There are still some very able printing companies making an excellent living from this market.
Four colour process printing provides great results particularly as the firing process in the kiln helps blend the colours and reduces the characteristic dot patterns.
Transfers can be produced using multiple colours, 20+ is not unheard of. The challenge of producing waterslide transfers is maintaining the condition of the adhesive coated transfer paper. Variation in the paper during printing can wreck accurate registration.
Special dryers known as wicket dry are often used and the print shop has to have the humidity carefully controlled. Although you don’t need a production lehr or kiln to produce transfers you will need a means of test firing the applied transfers.
With heat applied transfers the production methods are similar, but rather than printing onto adhesive coated paper a release paper is used and the image has a heat activated adhesive that forms a temporary bond with the glass or ceramic, allowing automatic application with heated silicone rubber formes. Once applied the transfers are fired onto the glass.
In this series of two parts, FESPA UK's Peter Kiddell has just touched on the topics of glass and ceramics printing. It is not easy but it can be a lucrative market.
There is a resurgence in the UK and European market as end customers want the exclusivity and cache of finely decorated glass and ceramics.
Topics
Interested in joining our community?
Enquire today about joining your local FESPA Association or FESPA Direct
Recent news
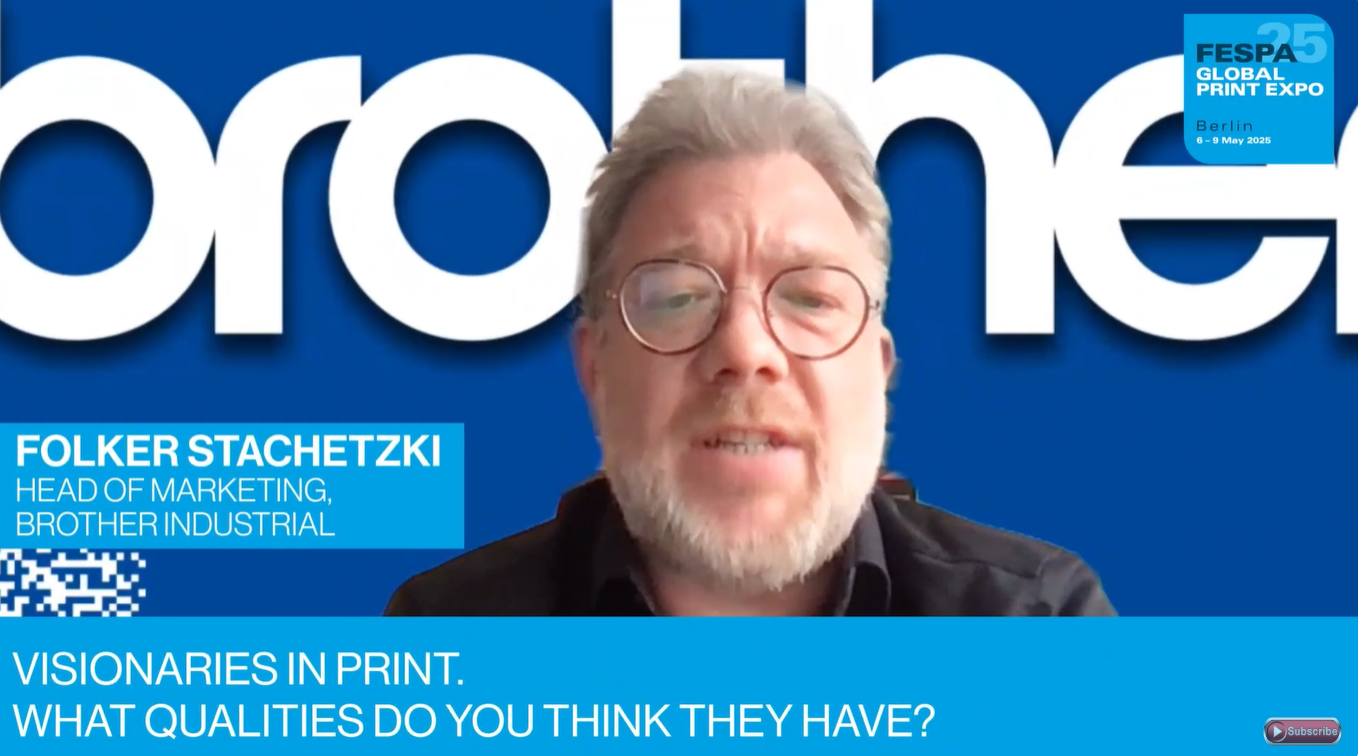.png?width=550)
What qualities should visionaries in print have? With Folker Stachetzki from Brother
We speak to Folker Stachetzki, Head of Marketing at Brother about visionaries in print.
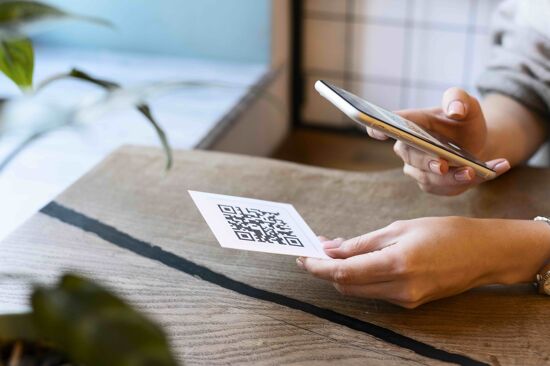
Bolstering personalisation by combining print and digital technology
Using printed material in combination with digital technologies offers more opportunities to those offering personalisation to customers. Rob Fletcher shares some recent examples of the print and digital working together to enhance the impact of personalised pieces.
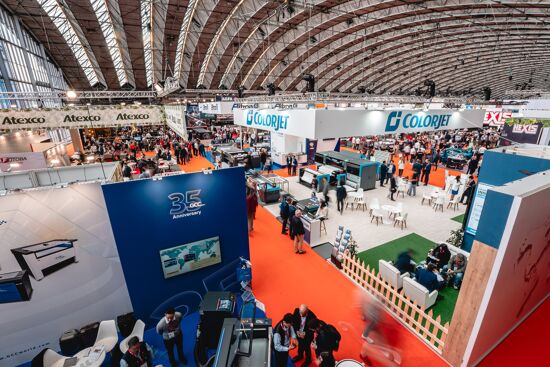
European Sign Expo to highlight developments shaping the future of signage and visual communications
European Sign Expo 2025 (6 – 9 May, Messe Berlin, Germany) is weeks away and a host of leading exhibitors are all set to welcome Visionaries from across the signage and visual communications industries to their stands.