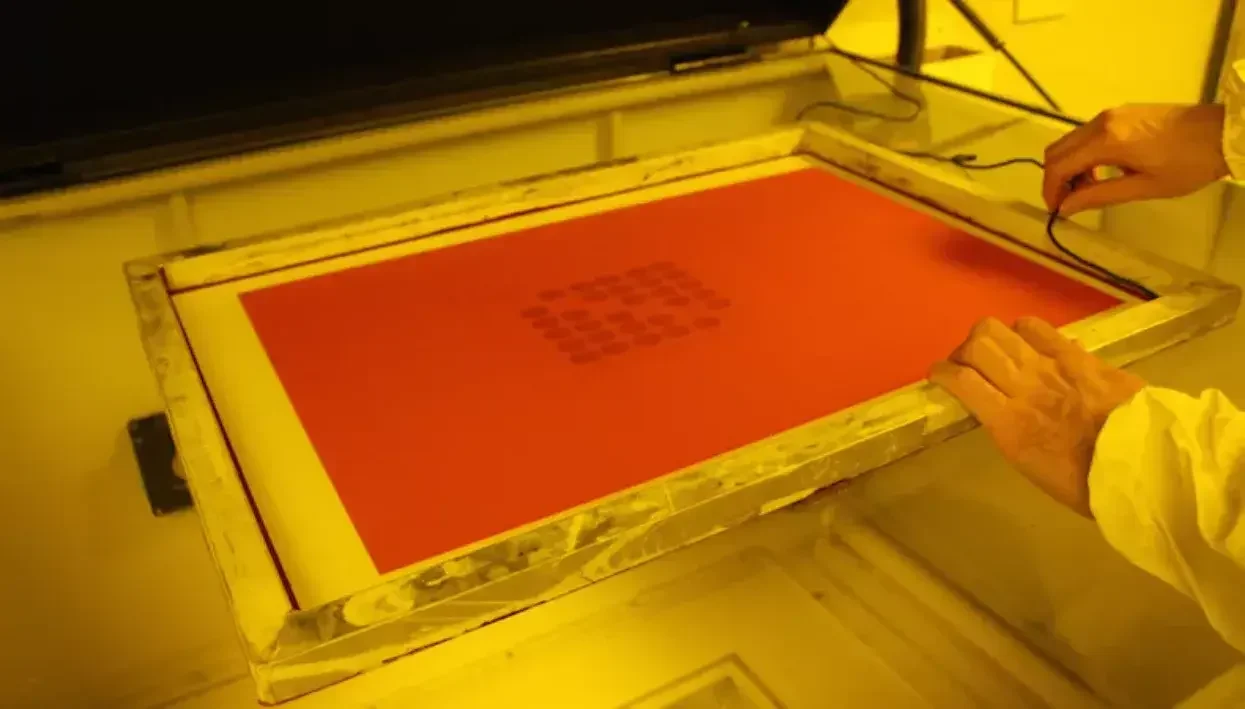
It has been well documented that full exposure of any emulsion guarantees the best durability on press.
However, what happens when you back off on the exposure time in an attempt to resolve fine detail and use post-exposure to try and restore durability? William Shorter, product manager of CPS – Chemical Products and Services, explains.
Firstly, why is full exposure so important?
If you expose your emulsion at only half of its optimum exposure, the UV light will penetrate the stencil layer but won’t harden all the emulsion. Therefore, during washout the stencil will likely stay on the mesh, but some of the under-exposed emulsion on the squeegee side will have washed away, and the stencil will quickly break down on the press.
If, for example, you expose at three quarters of the optimum exposure, more of the emulsion around the mesh fibres will become hardened and the stencil will then have a greater durability. However, on the squeegee side of the mesh the emulsion has still only been partially hardened and will be attacked by the solvents or water in the inks.
Fundamentally under-exposure is one of the most common mistakes in screen making and will always compromise stencil durability to some degree.
#ScreenprintingTopTip: If the emulsion feels slimy on the squeegee side during washing out, this is a clear sign that you haven’t achieved full exposure and print durability will be compromised.
But surely I can just post-expose it?
Trying to post-expose emulsion that isn’t there is a waste of time. So post-exposure of any grossly under exposed stencil simply will not work.
Post-exposing of Diazo sensitised Dual Cure emulsions that have been slightly under-exposed may have some effect, but will only give minimal improvement to durability. The exception is photopolymer emulsions where the light sensitive molecules are an integral part of the emulsion polymer structure. These will slightly benefit from post-exposure, but will never be as tough as one that has been given optimum exposure in the first place.
In summary
To guarantee durability on the press, it’s all about optimum hardening of the emulsion on the mesh. Under-exposure results in the emulsion being washed away from the squeegee side taking the under-exposed Diazo and cross linkable components with it. Therefore, post-exposure will have very minimal effect on the durability of the stencil system.
With regards to pure Photopolymer emulsions, these can show some benefit from post-exposure due to the molecular structure of the emulsion, but again the best durability comes from an emulsion that has been exposed to its optimum.
If you feel you are having to under-expose to reproduce fine details you should re-evaluate other parameters first, such as quality and specification of artwork, emulsion type and coating regime, mesh count and colour, design and specification of exposure equipment.
#ScreenprintingTopTip: It is really important to check the exposure time of your emulsion periodically, especially if the exposure equipment is in constant use. Ideally, this should be done every month using an Exposure Calculator.
#ScreenprintingTopTip: Where possible, and specifically when wanting to print fine detail, it is better to use yellow or orange mesh rather than white due to the reflection of the light during exposure. This means you shouldn’t have to under-expose in order to resolve fine detail.