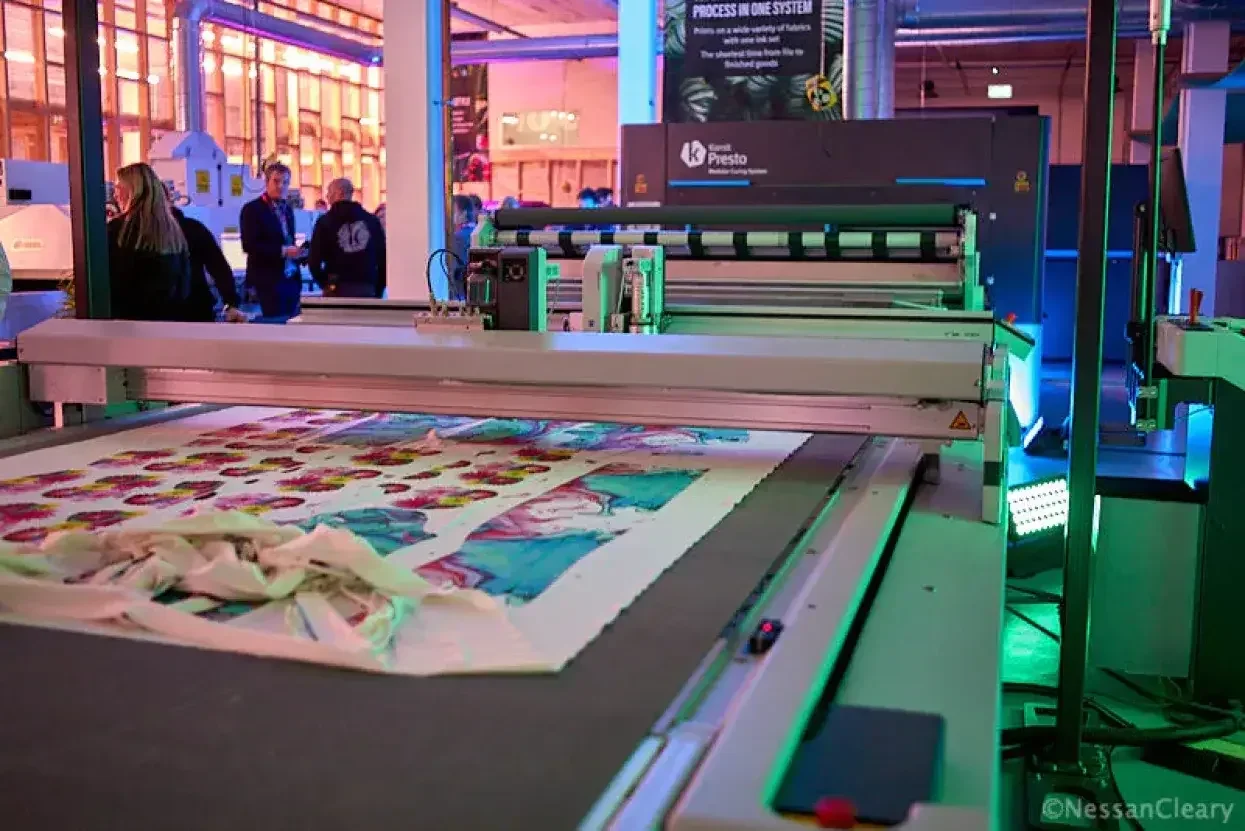
Nessan Cleary shares how the success of digital textile printing is dependent on the advances in finishing for textile production. The level of automation is a contributing factor to the efficiency of localised production and a more sustainable approach.
There have been enormous advances in digital textile printing but most of these are around the actual printing, particularly the inks and the range of fabrics that can be printed to. This has led to a new market segment, fast fashion, based around personalisation and short run printing, particularly direct to already produced garments. But for digital printing to become the dominant technology in textiles, it will have to be able to fit into a cost-effective production chain.
That in turn requires some automation throughout each textile manufacturing stage. For now, we are starting to see some automation being introduced to certain areas. Thus there are highly effective online ordering and payment systems. There is also reasonably good production print software so that ordering through to printing can easily be automated. This works well for Direct-to-Garment printing, where the blank items have already been manufactured so that the printing is just the final decoration stage. Even here, we are seeing automation in the material loading together with large drying tunnels to complete production.
However, when it comes to roll-fed printers there is a bottleneck around the post-print processes. But even here we are seeing some automation starting to become more widespread. Most roll-fed printers are supplied with some form of drying or curing system so that the fabric can be wound onto a take-up roll direct from the printer.
The next step is to cut the pattern out of the printed roll, which can be done with a digital cutting table. Some of the established vendors have embraced the textile market and adapted the material handling and software around their cutting tables. Zund, for example, offers a turnkey textile cutting solution. The company has developed a number of material handling systems that can feed the material to a cutting table without subjecting it to tension that might cause the fabric to stretch. This is matched by software developed specifically for automated textile cutting, including a database of different materials with specific parameters. Zund’s MindCut Studio software includes options for matching cutting patterns to the fabric that can cope with repeating print designs. It can also colour code different parts to make it easier to pick and sort the parts after they have been cut. More importantly, Zund uses an open interface that allows it to integrate with other vendor’s equipment such as roll-fed printers.
This micro factory has prints coming off an MS textile printer, through a cutting table, and straight to sewing.
©Nessan Cleary
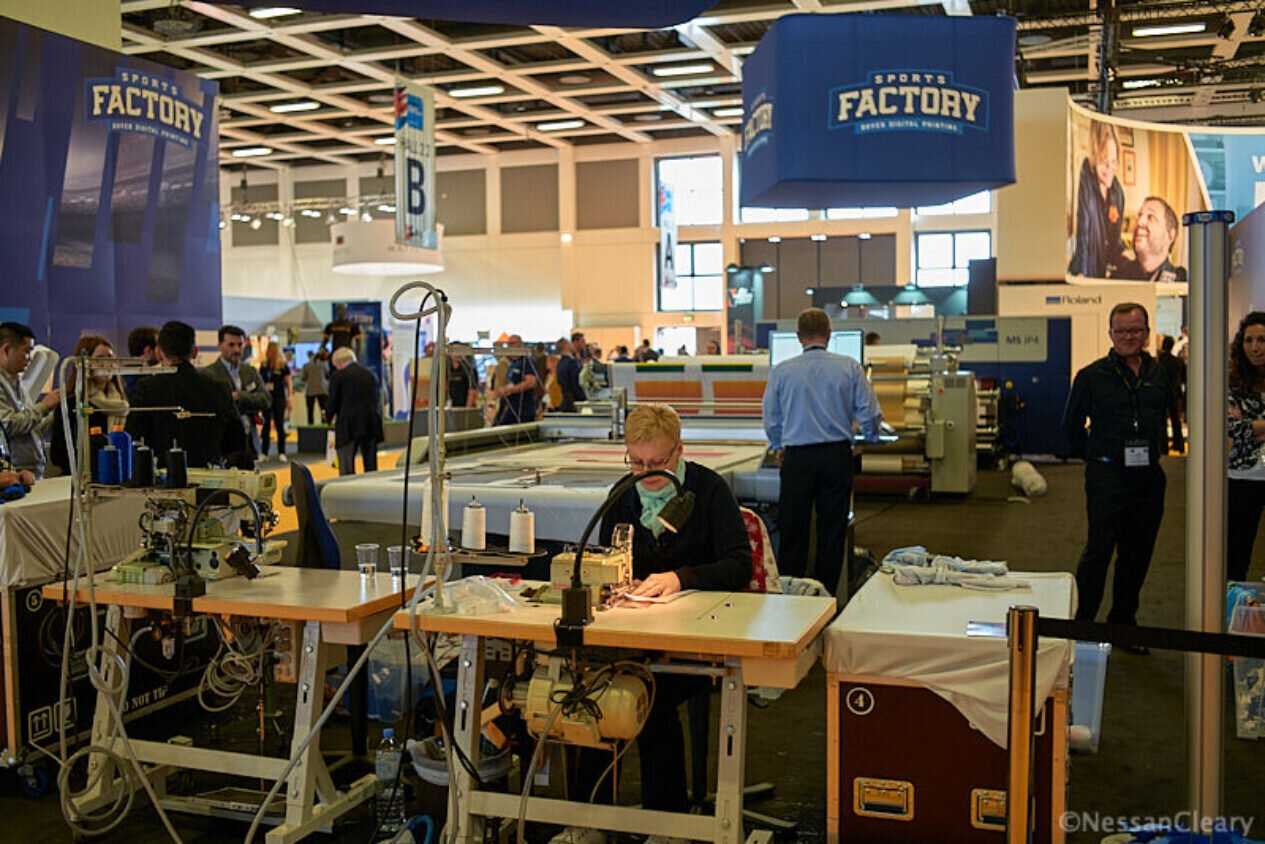
This has led to production lines that pair a cutting table complete with a conveyor system, working together with a roll-fed printer. This set-up means that the fabric roll, complete with printed patterns, can be fed directly from the printer through the cutter. You could even add a robotic system to collect the cut pieces leaving the waste to be dumped by the conveyor into a collection bin.
The next step is to sort and sew the parts together into finished garments. For now this is still a largely manual process that requires a roomful of people armed with sewing machines. This is because there is a great deal of dexterity required for good quality sewing as materials may stretch or become misaligned within the sewing machine. Nonetheless, there are some sewing robots that are starting to automate this area as well.
These systems essentially consist of a robotic arm that can grasp the fabric and move it through the sewing machine. A central control system can read the pattern for the garment to be produced and map the movements required from the robotic arm to complete that pattern. This has to be paired with a vision system and sensors that can be used to guide that arm and can pick up issues such as stretching of the material as well as correcting for any misalignment.
The technology isn’t yet good enough for more specialised applications such as high quality embroidery work but can handle day to day tasks such as seams and cuffs. Sewing robots are particularly suitable for relatively straightforward tasks such as curtains and furniture. For now, these robotic systems are usually built for particular customers and their material handling elements are bespoke to those customers’ needs.
Consequently, it will be a while before robotic sewing systems become widespread, partly because of their high cost, but also because there is considerable programming required for each new pattern. That said, some providers are developing cheaper alternatives. Sewbo, for example, uses a water-soluble agent to stiffen the fabric and make it easier for a robotic arm to control the material and pass it through an existing sewing machine. The company, which is based in California in the USA, claims that this eliminates most of the difficulties of handling fabrics and allows off the shelf industrial robots to be used for sewing, which takes out most of the cost. Once the garment has been sewn together, the stiffening agent can be rinsed out in hot water.
The final step is to fold and bag the finished items, and there are a number of existing machines that can do this and are routinely paired with screen printing garment production lines.
It obviously follows that if all of these processes were combined it should be possible to set up a completely automated production line capable of taking in white rolls of fabrics at one end, printing the design as needed and producing the finished garments at the other end. This sort of end-to-end production already exists in other areas of commercial printing, notably for book printing down to a production run of one.
This level of automation could bring fully-automated micro factories for garment production a step closer. That in turn would allow for highly localised production, which is a much more sustainable approach than transporting goods all over the world. It may even become more cost-effective in some markets to print graphics to a roll and then automate the t-shirt production for local sales rather than buy and ship blank t-shirts half way around the world. That would bring with it the flexibility to offer a wider range of products and for brands to offer more personalisation in their product lines.
To discover the latest content that covers a wide range of sectors including textile printing and finishing sign up for FESPA’s free monthly newsletter FESPA World available in English, Spanish and German.