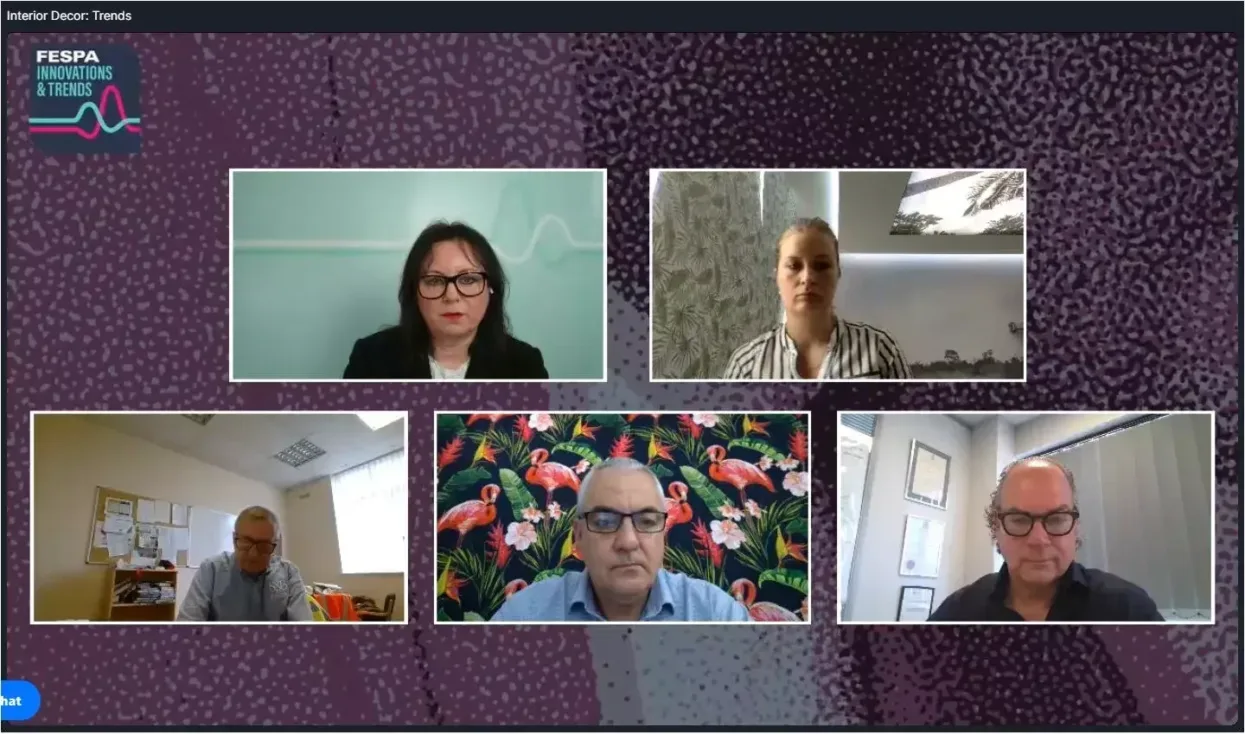
In our recent FESPA Innovation & Trends (FIT) virtual event we brought together four printers from across the world to discuss the latest trends in digital print for interior design applications.
The host: Debbie McKeegan, FESPA’s Textile Ambassador and CEO of Texintel has spent her entire career in the textile industry working with both analogue and digital production.
The experts: Stephen Thomas, Managing Director at Standfast & Barracks, an interior décor printer based in the UK, who has moved from being a conventional rotary and flatbed printer to 60-70% of their business today being digital.
Tony Attard, CEO at Panaz a global designer and manufacturer of high-quality fabrics and wallcoverings. Tony has been involved in the textile industry for many years and started Panaz in 1987.
Denise Lang, Managing Director at Lang + Lang, an Austrian based manufacturer of high-quality prints for installation in architecture, interior design and POS (point of sale) with a focus on the hospitality sector.
Magnus Mighall, Managing Director at RA Smart, a UK company celebrating almost 50 years as a supplier of speciality textile printing equipment.
Colour management can be a big issue in the textile industry. As we move on to using faster data speed of manufacture, we have to get this right, otherwise, we’re creating waste. We’re increasing waste if we’re using poor colour management. I’d like to ask all of you, how do you control sampling in printed production to increase efficiency and reduced waste resources?
Stephen: Yes, it’s quite remarkable the difference between a reactive and a pigment machine and how it has a massive improvement in your technology and your efficiency. It takes us a third of the time to get a colour right on a pigment machine compared to a reactive. When you think of a reactive machine, you’ve got to steam and wash it as well. If you think of the energy requirements to get the product right and the fabric you waste, the operating efficiency of our pigment machines are significantly better. We’re not brilliant at it yet – we’ve got lots to improve on.
The other thing is the technology improvements in RIP software and things like that are improving predictability on cloth. We want to get to a point where we can just pass the product off and print it without checking it for volume. Now, we’re not there yet, because that’s a big gamble, but if we can get to that stage, we’re automatically going to reduce our waste as well. That’s our challenge in our business, improving RIP software, moving to pigment technology and improving our skill base.
Magnus: Yes. I think colour profiling is key. We’re reliant on good RIP software, for sure, but we’re also very reliant on the skill of our operators and designers to create colour profiles that we can rely on day-in, day-out. I think we have probably over 45-50 textile bases that we print on as a mission printer. It simply isn’t practical that we actually sample every design before we print the production.
We are very much reliant on the RIP software, the colour profiling and the skill of our operators to know what that end result might be with whichever process we’re using, whether it be reactive, acid, dispersal, or pigment. Absolutely key and we like to think we get it right most of the time, but I’m sure we’re not getting it right 100% of the time.
Denise: For us, the topic of colour, of course, is very important, because it needs to fit the overall design scheme. The way we try to reduce waste here is to get a basic understanding of the colour first, so to get a RAL reference or Pantone reference or just anything already from the client. That of course, reduces some possible samples in the first instance, and then we really try to match just the colour first by printing some different small squares on the overall width of the row. We then send this to the customer, put it in the right room or next to the chair or wherever it will be and let them decide on the right colour. We then add the design to it and make a final sample and then we’re basically done.
Tony: I think that colour management is so important. Obviously, I echo everybody else’s views on RIP software. Magnus, I’m amazed. We obviously specialise in sublimatic disperse and we have enough problems. If we move one design to another machine, we even have problems. Colour management is absolutely massive.
You can see the whole conversation here, and for more information on Day Two of the FESPA Innovation and Trends Wide Format Graphics and Interior Décor event, visit here.
Discover the latest innovations in digital textile printing at the Global Print Expo 2021, Europe’s leading exhibition for screen and digital wide format print, textile printing and signage. Discover the latest products, network with like-minded individuals and explore new business opportunites. Register now and use promo code FESH101 to receive a discount of 30 euros.