Available substrates for outdoor sign and displays
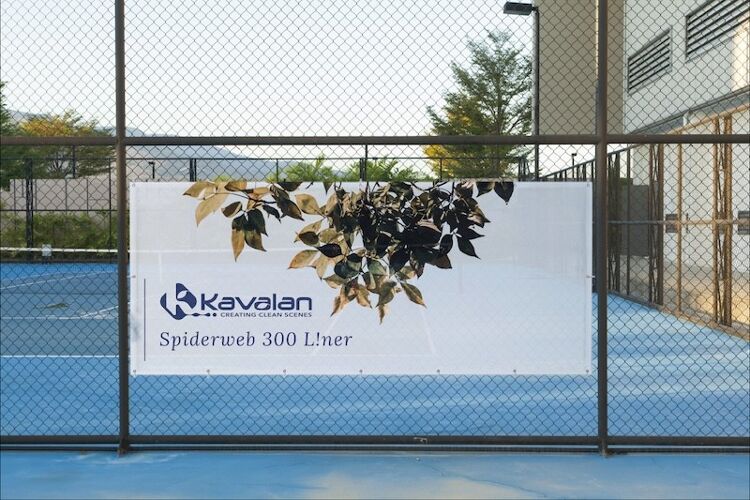
Nessan Cleary details the available substrates for outdoor sign and displays.
The weather plays an outsize role in the life of those signs and displays that are destined for use outdoors where conditions could range from sunny to below freezing, with plenty of wind and rain, with some regions having more extreme types of weather than others. This means that such signs need to be resistant to UV light, waterproof and robust enough to cope wind as well as surface abrasion.
This applies equally to both the ink and the substrate. However, inkjet ink will have been designed specifically for the printer and have benefited from huge amounts of R&D to cope with such challenges. This isn’t always the case with the substrates, many of which have been borrowed from other uses such as the construction industry. Regardless, a modern UV-curable ink should be able to cope with most substrates without requiring any special treatment. Many of these substrates can also be used for screen printing and latex or resin inks.
Caption: This outside wall covering by Creative Silhouettes in Canada made use of Drytac PolarGrip polymeric self adhesive vinyl.
One of the major considerations is the required life span for the display. Some materials will simply last longer than others. It’s important to pay attention to the properties of the substrate in relation to where the display is to be located, as some materials will suffer from exposure to sunlight, while others will offer better waterproofing or resistance to condensation and moisture.
Lamination has become less common now that it is straightforward to print UV-curable inks direct to rigid boards. However, there may be an argument for using a laminate to protect both the ink and the substrate from the elements to increase the longevity of the graphic. This will make it harder to recycle the graphic when its no longer needed, but there may be little alternative to guarantee that graphic a long service life. Besides, if lamination avoids the need to reprint and replace the display, then it may ultimately lead to less waste and a lower overall environmental footprint, as well as less cost.
The overall sustainability is increasingly a factor that customers will want to take into account. Some of these substrates are easier to recycle than others and in some cases you can use a recycled material though it may be harder to find a white recycled substrate.
There are far too many different substrates available to list them all here but it is worth breaking them down into types of materials. Polyvinyl chloride or PVC vinyl remains one of the most commonly used materials and is ideal for outdoor signage as its highly weather resistant. It does not have a good reputation for sustainability though you can use recycled PVC media, which contains a percentage of post consumer waste but without compromising the performance.
In terms of rigid materials, there are a number of foam boards, which are made out of compressed foam PVC and were originally developed in the 60s for use as insulated building panels. PVC foam board is a very common material that’s lightweight but with excellent strength to weight ratio. It’s waterproof and suitable for outdoor use. It’s available in various sizes and thicknesses as well as a choice of colours. Different vendors have their own brand names, such as Foamex, Foamalite and Palight and there are some variations in the material used, such as using foamed polystyrene.
Another variation is to use a foam composite board, which can be a little more robust, particularly in terms of UV resistance which can cause the white materials to yellow over time. Amari, for example, makes Smart-X foam board, which consists of an expanded polystyrene core sandwiched between white High Impact Polystyrene Sheet covers, which are said to be resistant to weathering and UV light, while polystyrene is not affected by moisture. It’s extremely lightweight and suitable for use outdoors for up to two years.
Kapa is another type of composite board, with a polyurethane foam core sandwiched between two covers. There are a number of different versions for particular applications that depend on the type of cover, some of which are not suitable for outdoor use. That said, KapaPlast has plastic coated covers and can be used for some outdoor applications.
The main alternative is to use a plastic board. Acrylic, which is sometimes sold as perspex, gives a similar look to glass but is considerably lighter and stronger. It’s also weatherproof and available in range of sizes and thicknesses. Typically its clear but there are different finishes, including frosted and tinted looks, as well as a mirrored effect and a choice of colours. There’s also a more sustainable version made of recycled acrylic.
Lumex A is sometimes seen as a cost effective alternative to acrylic. Its a clear thermoplastic sheet made of Amorphous Polyethylene Terephthalate or APET. It’s used in packaging and for display units as well as signage. It can be recycled and should last for up to four years outdoors.
There are also other types of plastic sheeting. Correx is a corrugated material made from polypropylene plastic that’s typically used for re-usable packaging as well as signage, particularly estate agents boards. It’s available in thicknesses from 3-5mm and in a range of colours. There’s also a version made of recycled plastics, but this only comes in black. It’s waterproof and weatherproof.
Caption: Kavalan has developed this Spiderweb 300 liner as a biodegradable complement to its existing Spiderweb 300 mesh substrate.
Another option is to use aluminium composite boards. The best known brand name is Dibond but there are several similar suppliers. They use a lightweight core, typically polyethylene, with thin aluminium sheets on either side. This makes for a lightweight rigid board that is structurally strong and easily machined. The aluminium sides give a very smooth and distinctive finish. There is a choice of effects, from different colours to a mirrored finish. This kind of board typically last for five years outdoors.
Wood is widely used for graphics, both indoors and outdoors. It stands up well to weathering and is easily cut and shaped and makes for a very sustainable material. The most common type of wood for display graphics is probably plywood though MDF is particularly suitable for hoardings around construction sites.
Finally there are a number of different banner materials such as tarpaulin with varying degrees of performance. One of the most common banner materials is mesh, which is particularly good for outdoor displays as the surface has many holes that allows any wind to blow through it. This makes the banner very lightweight as well as practically windproof, which significantly cuts down on the level of stress that the graphic will have to cope with outside. They are usually made of PVC or a similar plastic material. They can be easily finished with hems, pockets or eyelets.
Naturally, anyone producing outdoor displays wants the best balance between high performance and low cost from their substrates. The choice of substrate will have the biggest impact on the pricing, but will also make the most difference to the overall success of the project. After all, as with death and taxes, the weather is hard to avoid and can be quite unforgiving.
Interested in joining our community?
Enquire today about joining your local FESPA Association or FESPA Direct
Recent news
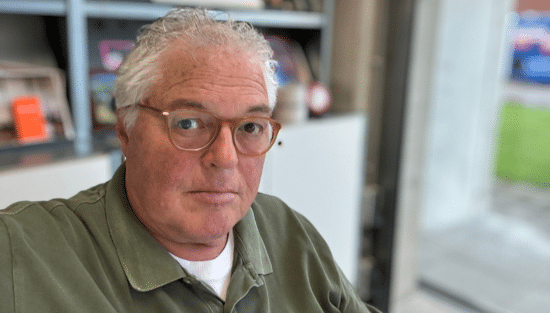
The importance of Personalisation in Direct Mail - The Power of Print
Jeroen van Druenen, CCO of Jubels discusses how personalised direct mail, especially print, boosts engagement and ROI by tailoring content to individual recipients. Using variable data printing (VDP), marketers create unique designs and offers, enhancing relevance and fostering stronger customer relationships. Physical mail's tangibility and lasting impact further amplify personalisation's effectiveness.
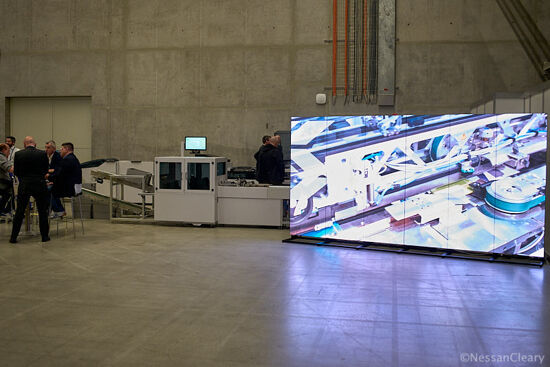
What are the current trends for digital screens?
Digital screens are evolving rapidly, moving beyond simple signage. MicroLED technology improves resolution and efficiency, while 3D and AR displays offer immersive experiences. AI is transforming content creation and analytics, personalising interactions and optimising screen placement. Larger, wall-sized screens and temporary rentals at events are becoming more common. As screens become ubiquitous, innovation focuses on eye-catching solutions to maintain audience engagement.
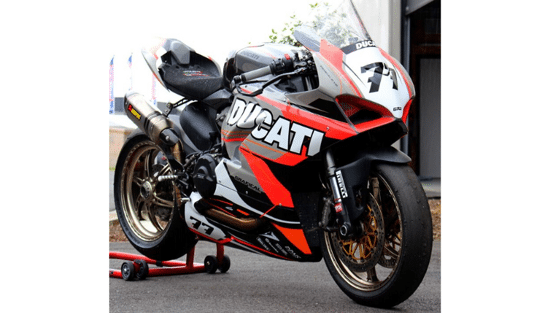
Hints and tips for vehicle wrapping success
While rising demand for vehicle wrapping is good news for the industry, this is placing more pressure on companies to deliver quality work at a solid pace. Here, Rob Fletcher picks up some tips from several experts in this sector to help wrappers operate smoothly.
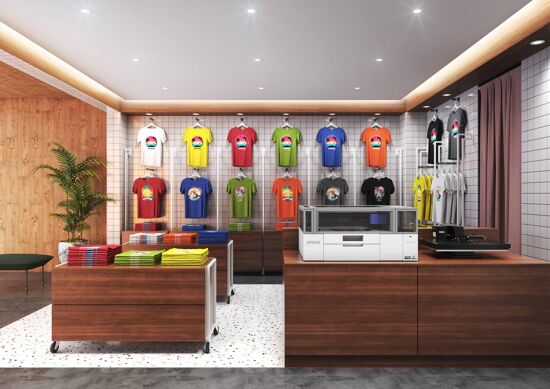
What are the opportunities in Personalisation for Sportwear and Signage?
Rob Fletcher discusses the growing importance of personalisation and digital innovation across sectors. Major brands use personalised print to engage customers and boost sales. Personalised sportswear demand is increasing, and companies like Eurojersey embrace sustainable manufacturing and digital transformation.