How to integrate different softwares to build a more automated workflow
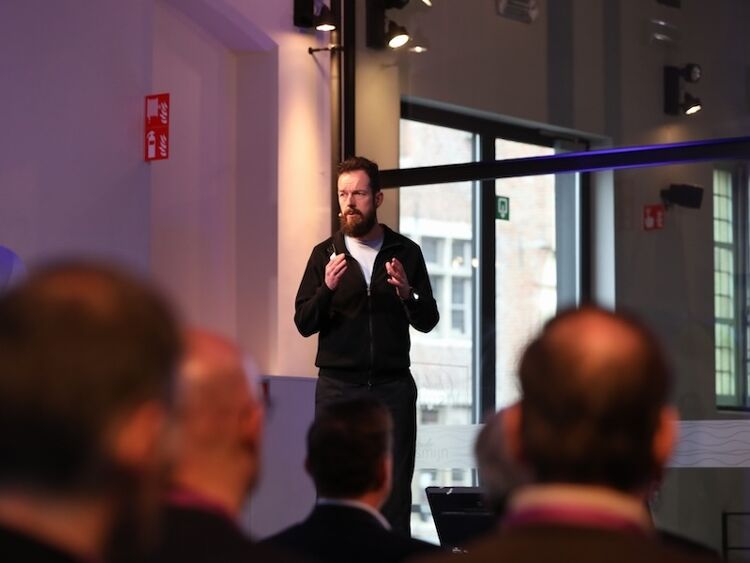
Nessan Cleary shares the trend that in recent years the print industry has become more willing to working with SaaS solutions as it reduces the need for upfront investment.
Every modern print business will accumulate a lot of different software packages, often from different vendors, each usually designed for a specific range of tasks. This software might come with a new piece of hardware, such as as RIP, or have been bought in to solve a particular problem. The trick is to integrate all these together to create a single automated workflow. Inevitably there will be some cost in doing this but more automation should lead to more output and less errors, which should justify the cost.
The most obvious way to integrate different processes together is through hot folders, which can be configured to have specific functions. You can set up hot folders, sometimes also called Smart folders, in either Windows or Mac systems and assign actions such as sending files to a particular print queue. Dropping a file into that folder will then trigger the action. Many print production programs also allow you to create hot folders with specific functions for those programs. This is a fairly common approach and works well for simple workflows, such as moving files from a colour server to a print queue.
However, there may be different outcomes from these processes, or some jobs might need more complex work. One option would be to write additional scripting to give a tighter integration between different programs. However, this will be expensive, and you will need to maintain the integration as the different programs are upgraded and other functionality is added to the workflow.
There are a number of solutions to overcome this without the need for bespoke software development. The most common of these is Switch, which has been developed by Enfocus, itself part of Esko. Switch is both easy to use and highly configurable. It allows users to build up their own workflow simply by dragging and dropping folders and icons to a blank canvas and then setting up connections between those items. The key to the system is the plug-ins that allow existing software from other vendors to connect to the system. These plug-ins used to be known as Configurators but these have now all been converted to apps and are available via an Enfocus Appstore.
It’s not by any means a new system and over the years Enfocus has built up a huge library of apps for most of the available production systems from many different vendors. This includes MIS and Web-to-Print solutions, as well as RIPs and design software plus production tools like preflighting, colour management and imposition. No matter what equipment you are running, there’s a good chance that you will find a corresponding app to connect it to Switch. These apps, which have often been created by third party software developers, allow Switch users to access much of the functionality in those tools in order to run them directly from Switch.
There are also a number of modules available that add further functionality. This includes a Metadata module that can integrate an MIS or Web-to-Print system into a Switch workflow, and then use metadata within a job ticket to route that job through the production system. Other modules allow connections to a database, or to allow customers to access the Switch workflow through a browser. There are also Switch Scripting tools that allow users to write their own connections, though this obviously depends on having some scripting knowledge.
This year we have also seen several cloud-based solutions being offered to help solve the issue of how to connect different production platforms together. Essentially these pick up on the growing trend of building an Integration Platform as a Service, or iPaaS, that can be hosted entirely on cloud services. This allows it to act as a central hub that can connect to all the other production software available. Since iPaaS is a variation on SaaS, or Software as a Service, it is also easily scaleable, without any overheads in infrastructure and license management. This makes it easier to keep up with the growing demands for shorter deadlines and smaller print runs.
Four Pees, which specialises in distributing and integrating software, has developed its own system which it calls Atomyx. There are three parts to it. Atomyx Manage is the main dashboard, and shows the workflow within a print service provider as well as the connections between print service providers, print buyers, and online print platforms. It offers seamless integration, order visualisation, automation, and manual intervention capabilities.
Then there is Atomyx Prepare, which is based around callas pdfToolbox technology. This includes a lot of prepress functionality such as preflighting, colour conversions and file preparation. The final part is Atomyx Layout, which is a print layout API optimizing media usage through automated layout planning such as imposition and nesting.
Atomyx will work with most print technologies, including wide format, labelling, packaging and commercial print. In addition, there are plug-ins available for the Manage part that should it allow it to connect to other systems, such as e-commerce platforms or direct to print devices. Tom Peire, managing director of both Four Pees and Atomyx, says: “One of our goals is to also to connect print buyers with print sellers and print manufacturers. This means that online print platforms and brokers are on our list to connect. We have also established connections to RIP developers and textile print machinery manufacturers to explore how we can connect to their systems.”
There’s a new player on the block offering connectivity called CoCoCo, which has grown out Zaikio, a subsidiary of Heidelberg that is now being shuttered. This also takes a cloud-based SaaS approach, promising to connect different software and hardware devices together regardless of who originally developed them. It’s a modular system made up of three products that work together.
The heart of the system is CoCore, which connects to all the other systems such as MIS, printing machines and finishing devices. As such it can provide an overall dashboard view of all the connected systems, including jobs, delays and bottlenecks.
The actual connections are handled by CoConnect through pre-configured integration kits, which creates a data link between your systems and the CoCore module. Since the CoCore module is cloud-based it’s easy to scale up as needed and there are no hardware costs.
The third part is CoCollab, which allows companies to send their job data to other companies they are working with. That could be, for example, sending the job details to an outsourced specialist dealing with the display installation. It also allows for data to be returned, for example, to confirm that a job has been completed. Equally, this could allow a brand or retailer to send orders from their procurement system to the print service providers production workflow.
In conclusion, Switch is a proven solution while the iPaaS concept is relatively new and both Atomyx and CoCoCo will take time to establish connections with other software. However, the print industry has become much more willing to work with SaaS solutions in recent years because it cuts down on the need for upfront investment. In any case, every print company is unique in its own way, and will have to figure out their requirements and the level of investment they are comfortable with.
To discover the latest content that covers a wide range of sectors including software in print and automation sign up for FESPA’s free monthly newsletter FESPA World available in English, Spanish and German.
Topics
Interested in joining our community?
Enquire today about joining your local FESPA Association or FESPA Direct
Recent news
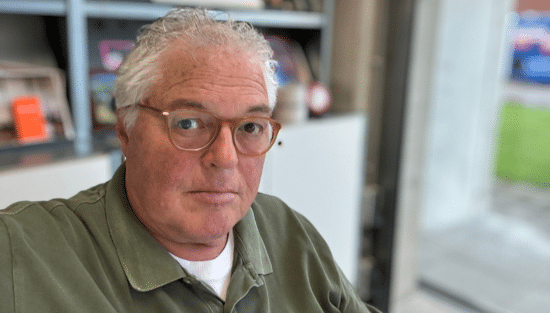
The importance of Personalisation in Direct Mail - The Power of Print
Jeroen van Druenen, CCO of Jubels discusses how personalised direct mail, especially print, boosts engagement and ROI by tailoring content to individual recipients. Using variable data printing (VDP), marketers create unique designs and offers, enhancing relevance and fostering stronger customer relationships. Physical mail's tangibility and lasting impact further amplify personalisation's effectiveness.
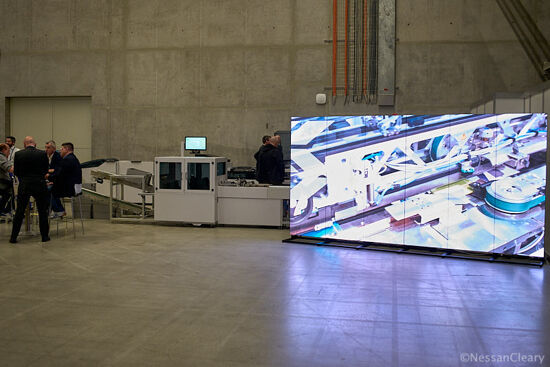
What are the current trends for digital screens?
Digital screens are evolving rapidly, moving beyond simple signage. MicroLED technology improves resolution and efficiency, while 3D and AR displays offer immersive experiences. AI is transforming content creation and analytics, personalising interactions and optimising screen placement. Larger, wall-sized screens and temporary rentals at events are becoming more common. As screens become ubiquitous, innovation focuses on eye-catching solutions to maintain audience engagement.
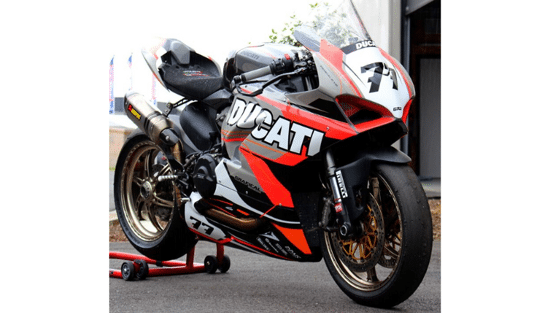
Hints and tips for vehicle wrapping success
While rising demand for vehicle wrapping is good news for the industry, this is placing more pressure on companies to deliver quality work at a solid pace. Here, Rob Fletcher picks up some tips from several experts in this sector to help wrappers operate smoothly.
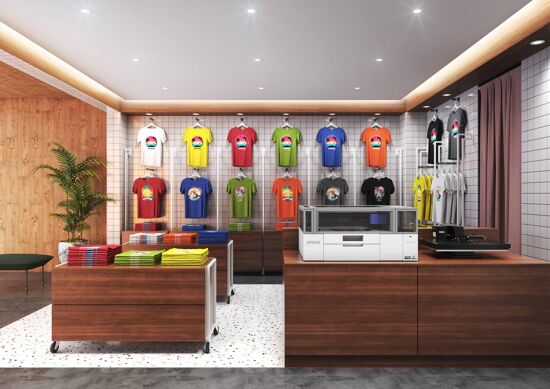
What are the opportunities in Personalisation for Sportwear and Signage?
Rob Fletcher discusses the growing importance of personalisation and digital innovation across sectors. Major brands use personalised print to engage customers and boost sales. Personalised sportswear demand is increasing, and companies like Eurojersey embrace sustainable manufacturing and digital transformation.