How to manage print queues and improve productivity for your print shop
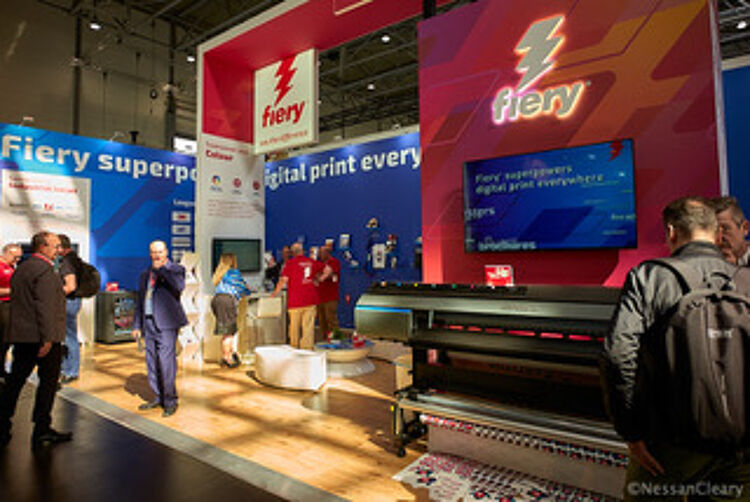
Nessan Cleary shares how print shops can increase both their productivity and profitability and the importance of automation to ensure files are printed as quickly as possible to generate the maximum income.
Traditionally, commercial offset litho printers have always separated the prepress from the printing, mainly because of the need to make plates before printing anything. But large format printing was one of the first sectors to fully embrace digital printing, and right from the start the RIP developers simply folded the file preparation into the RIP, eliminating the need for a separate prepress stage.
However, here we are, more than a quarter of a century since wide format digital printing became firmly established. The biggest issue for most print shops today is how to increase their productivity and their profitability. The easiest way to do that is to separate the job preparation from the production in order to keep the printers running at full capacity.
Ideally this means automating as much of the file preparation as possible, from the moment the job arrives to the point where it’s sent to the printer. The first stage is usually preflighting, sometimes known as quality control, to ensure that the file the customer sends in can actually be printed. This means checking the format, resolution and colour space as well as the fonts and ensuring that any lines are thick enough for the required viewing distance. Most preflighting systems can automatically correct some of these issues but for others you’ll have to request that the customer updates the artwork, or have a designer do it to save on time.
Other file preparation tasks will include tiling and nesting items around each other, either parts of the same job, or grouping different jobs together to save on media wastage. You’ll also need to include any special effects, such as creating a mask for a varnish layer, or set up multiple layers for a backlit. This preparation should also include adding cut lines and eyelet holes as well as any positioning marks. You might also want to add notes that can be printed on the back of a graphic as a guide for installing the final job.
Most jobs will require some degree of proofing for a final sign-off. In many cases this can be done online with a softproof, freeing up time for the complex jobs where it might be necessary to produce a mock-up or hard copy proof.
The prepress department is also responsible for routing the job to the print queue, based on the attributes of the available equipment, since some printers will, for example, handle skin tones or high resolution photographs better than others. It’s best to group similar jobs together, either to save on consumables, or simply on time switching from one substrate to another.
There’s no simple formula for optimising prepress as this largely depends on a number of factors including the mix of print technologies, the number of wide format printers, the scale of the business and the overall business model, not to mention simple personal preferences.
Most large format RIP vendors also offer a standalone prepress or workflow software that can be used to prepare files before sending them on to the RIP.
All Agfa printers come with the company’s Asanti RIP, but this is only part of the Asanti software. Asanti was conceived as a large format version of its Apogee prepress workflow, which had been developed over many years for offset litho printing. Agfa was one of the first software vendors to recognise that the same principle, of separating out the prepress work to improve throughput on the printer, would apply equally to large format. Asanti is currently sold via subscription in a choice of three levels. The Core version includes basic preflighting and colour management as well as the RIP, but you need the Advanced and Expert variants to get nesting, tiling and other features.
Fiery’s large format offering includes JobFlow, which can be used to automate a number of tasks before the printing stage. This includes preflighting, based on Enfocus Pitstop Pro, and image enhancement, as well as routing the jobs through to the correct workflow. It also allows jobs to be archived for later re-use. Fiery’s suite of large format tools includes Color Profiler, for the colour management, and Prep-It for adding cut marks.
Caldera has developed PrimeCentre specifically for handling prepress tasks. This includes preflighting files before they reach the PrimeCenter queue. From there the software runs through all the main prepress tasks, including nesting, arranging bleeds and creating annotations. It can also be used to set up cutting paths and to create positioning marks for a camera system. PrimeCenter is sold via an annual subscription in three different levels, each offering greater degree of automation. Once the files are ready for printing, they can be exported as PDFs that can be used with any large format RIP so that you are not tied in to using Caldera’s RIP. The latest 3.1 version supports direct to film for textile printing, as well as double-sided banners.
Caldera’s PrimeCenter can handle large format prepress and will work alongside RIPs from other vendors. ©Nessan Cleary
There are plenty of integrated workflows, which we’ve covered in other stories this year, from vendors such as Durst and OneVision. But another alternative is to build your own workflow by investing in separate tools that can handle each of the main steps. The advantage is that you can tailor the workflow to exactly suit your needs and can put more weight into certain aspects such as the preflighting.
Two of the most widely used preflighting solutions are Callas PDFtoolbox and Enfocus PitStop Pro, both of which are also available as server-based programs and can automatically catch most problems.
Equally, solutions such as GMG’s ColorServer can be used to automate the colour management and ensure the best conversion between colour spaces, with the right profiles for the printer and media combination.
There are several options for automating nesting, such as Tilia Griffin, which is now sold through Esko. This allows users to set up their own rules to automate the layouts, and can feed back to help produce more accurate estimates.
In conclusion, the prepress set up will ultimately reflect the philosophy behind the print shop. Regardless of how you approach this, automating where possible to get the files into the print queue as quickly as possible will keep the printers running, which in turn should generate the maximum income.
Interested in joining our community?
Enquire today about joining your local FESPA Association or FESPA Direct
Recent news
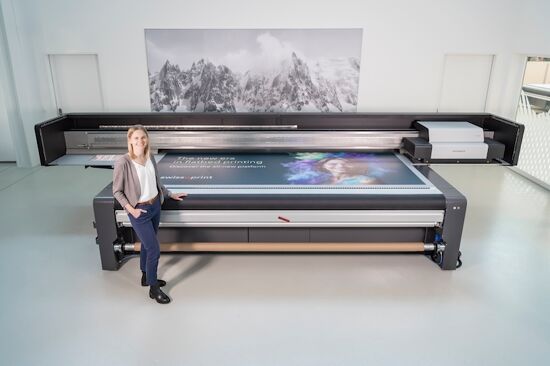
The importance of ink for large format printers
Ink is crucial for large format inkjet printers, influencing substrate compatibility, productivity, and cost. Nessan Cleary discusses the three main types which include UV-curable ink, latex ink and eco-solvent ink. Each ink type has specific strengths and weaknesses, making printers choice dependent on budget and intended applications.
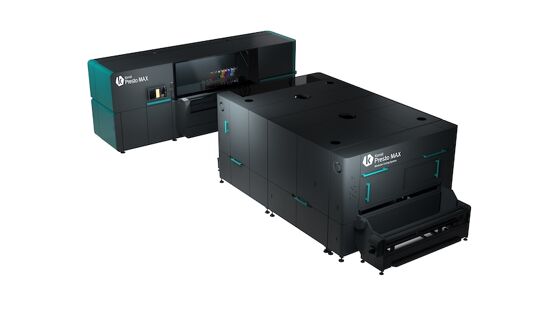
What are the benefits of Direct-To-Fabric printing?
Direct-to-fabric printing is gaining popularity for high-volume textile production, enabling on-demand, customized short runs. These printers offer ink flexibility, accommodating various fabric types like cotton and silk, though ink development focuses on faster turnaround by reducing pre- and post-processing. Compared to traditional methods, direct-to-fabric inkjet printing is a more sustainable option due to reduced water and chemical usage, and localized production.
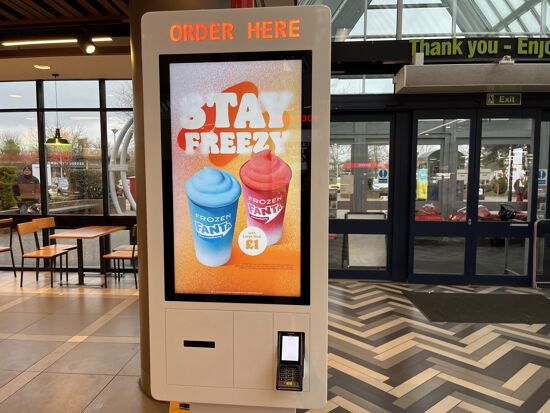
What are the opportunities for large format providers regarding digital touch screens?
Digital touchscreens are becoming increasingly common, offering businesses opportunities to improve customer engagement and streamline operations. Nessan Cleary shares, while more expensive to implement than standard digital displays due to complex software and integration needs, touchscreens provide self-service options, multilingual support, and can reduce staffing costs in various settings like retail, transportation, and healthcare.