Processless plates take over
Processless plates make economic and environmental sense. Laurel Brunner believes the tipping point has finally been reached.
2014 was a watershed year for computer-to-plate (CtP) production: processless platesetting shifted up a gear, with all three major manufacturers making substantial headway in the market.
Processless plates make economic and environmental sense, because you simply image the plate and mount it on press. Simple. There are no chemical disposal costs or waste water to deal with, so significant reductions are to be had in water usage, waste production and energy consumption. Equally important you save time producing plates and the latest generation achieves decent results on press. What’s not to like?
The market now has a choice of three excellent direct on press plates, so printers really have no excuse for not making the move to processless. These plates aren’t quite as simple to output as a page from a desktop printer, but all they basically need is a thermal imagesetter imaging at 800 to 850nm. The convenience, cost savings and throughput improvements are why growing numbers of printers are going processless.
All three major plate manufacturers claim to be the market leader. Agfa has been in this sector for many years, with well over 10,000 installations, and recently introduced the new Azura TE, a direct on press plate for run lengths of 75,000+.
Most of the Agfa installations so far have been for the chemistry-free Azura offline plates. These require a clean-out unit before being ready for press, rather than being direct on press plates. Fujfilm has 3000 sites worldwide producing its PRO-T plate and is seeing consistent growth in customer numbers.
According to a spokesman “it is safe to say that PRO-T is still the number one processless plate in the market by a considerable margin”. That could start to change, given the speed with which Kodak’s Sonora has been adopted and the large installed Agfa customer base, many of whom are making the move to Azura TE.
Of the top three, Kodak is the most keen to publish installations data, and last July announced that there were 1000 customers using Sonora processless plates. Earlier this year Kodak said that there were over 1800 companies using the plate and that strong growth is expected to continue worldwide. The company’s North American customer base grew by 400% and its European one by 200% last year, as new customers invested in Sonora and existing ones switched from Kodak Thermal Direct.
Kodak is investing into new manufacturing facilities, anticipating that 2015 will see accelerating growth in its installed base. In Asia the company has over 200 customers and has upgraded its factory in Xiamen, China. In Latin America Sonora News plates account for some 35% of Kodak plate sales.
2015 will be the year of processless platesetting. We expect to see growth in conventional thermal plates plateau as more printers go processless. This can only help improve print’s already positive environmental impact.
Source: This article was produced by the Verdigris project, an industry initiative intended to raise awareness of print’s positive environmental impact. This commentary helps printing companies keep up to date with environmental standards, and how environmentally friendly business management can help improve their bottom lines. Verdigris is supported by the following companies: Agfa Graphics, Spindrift.click, EFI, FESPA, HP, Kodak, Kornit Digital, Ricoh, Splash PR, Unity Publishing and Xeikon.
Topics
Interested in joining our community?
Enquire today about joining your local FESPA Association or FESPA Direct
Recent news
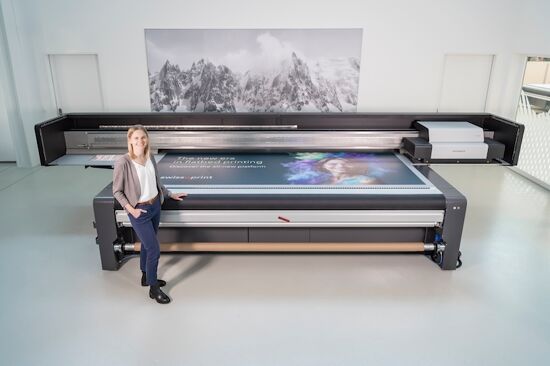
The importance of ink for large format printers
Ink is crucial for large format inkjet printers, influencing substrate compatibility, productivity, and cost. Nessan Cleary discusses the three main types which include UV-curable ink, latex ink and eco-solvent ink. Each ink type has specific strengths and weaknesses, making printers choice dependent on budget and intended applications.
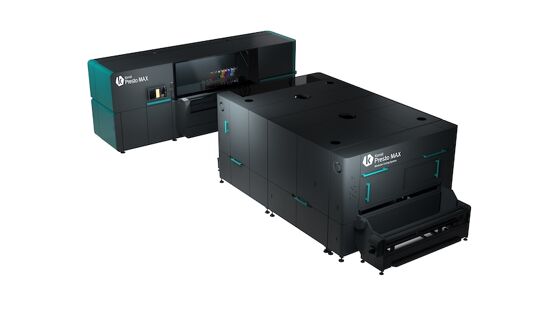
What are the benefits of Direct-To-Fabric printing?
Direct-to-fabric printing is gaining popularity for high-volume textile production, enabling on-demand, customized short runs. These printers offer ink flexibility, accommodating various fabric types like cotton and silk, though ink development focuses on faster turnaround by reducing pre- and post-processing. Compared to traditional methods, direct-to-fabric inkjet printing is a more sustainable option due to reduced water and chemical usage, and localized production.
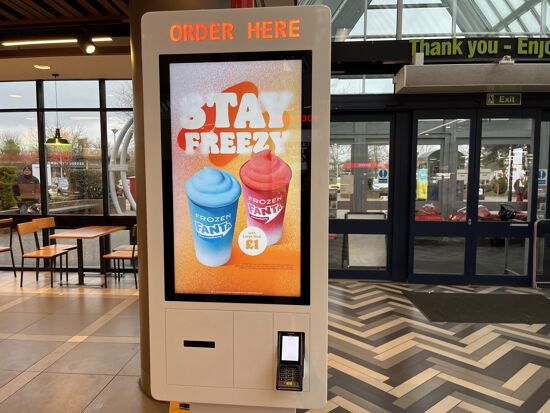
What are the opportunities for large format providers regarding digital touch screens?
Digital touchscreens are becoming increasingly common, offering businesses opportunities to improve customer engagement and streamline operations. Nessan Cleary shares, while more expensive to implement than standard digital displays due to complex software and integration needs, touchscreens provide self-service options, multilingual support, and can reduce staffing costs in various settings like retail, transportation, and healthcare.