The history of screen printing in Europe

Often called the "fourth printing process," screen printing has a rich history and a promising future. Sonja Angerer delves into its long history in Europe, separating myth from reality and exploring its market potential.
The early days of screen printing
The start of screen printing are thought to have taken place in Asia. This is because stencils were often used there to produce simple print patterns, especially on textiles. From the 18th century onwards, fabric stencils were thought to be used in Japan.
However, this is a rather simplified presentation, as the Swiss author Guido Lengwiler explains in his fundamental book "The History of Screen Printing", which was published in 2013. It is currently out of print but available as an e-book in German. The facts elaborately researched by Lengwiler for his book have also been incorporated into this article.
According to Lengwiler, open and perforated stencils have been used by many cultures to decorate a wide variety of objects. From the Middle Ages onwards, stencils were also used in Europe as an alternative to the hand colouring of long runs of simple woodcuts. The French Pochoir technique is also often believed to be a predecessor to screen printing. However, the process, which was mainly used by artists, was not completely replaced by screen-printing. As in 1947, the artist's book "Jazz" by Henry Matisse was published in stencil printing.
CAPTION: From left: Selectasine print from Berlin, 1930s, and exhibition poster Werner Arndt, 1953 (manual screen print). Photos: Archive Lengwiler, CC BY-SA 3.0, Werner Arndt, composition: S. Angerer
Screen printing in the 19th century
With the introduction of manufactories and the first industrial plants from around the middle of the 18th century, many new tasks for offices emerged. Therefore, in 1878 the "Typograph" and around 1880 the "Cyclostyle" photocopiers based on stencil printing were created. They were intended for the duplication of documents and considered the forerunners of modern screen printing. Until about 1900, countless other patents were granted, especially in the USA, for sometimes highly complicated systems for seamless stencil creation. Wires and wire mesh were often used for this purpose. They were quite versatile, being used for lettering for railway carriages as well as glass decorations and anything in between.
However, the first basic patents that marked the transition from marking to printing technology are attributed to Antoine Vericel and Hiram Deeks. Both were first-generation European migrants who worked on the US East Coast.
CAPTION: Production of felt pennants for souvenirs in the screen print (1943). Photo: Tom Parker, Public Domain
Screen Printing in the history of the 20th century
In 1902, Vericel patented a predecessor of the screen printing carousel, which was primarily intended for printing on home textiles. Deeks was already working with silk gauze for his "Stencil Duplicator", patented in New Jersey in 1903. This technology was also primarily intended for textile printing. In the same year, Deeks also had his technology protected in France and Great Britain.
These or similar processes were used in the USA until about 1915 mainly for printing felt pennants and other souvenirs. Often, these screen print pioneers seem to have understood their technologies as closely guarded trade secrets, so few details are known. However, it is quite certain among experts that graphic screen printing developed mainly in California.
Velvetone in San Francisco, founded around 1908 is therefore considered the first American screen-printing company. In 1915 and 1916, Selectasine in San Francisco and Vitachrome in Los Angelos followed. At that time, the first graphic works were already being created and reproduced using the screen print. Trade magazines such as "Sign of The Times" first reported on screen printing as early as 1916, so knowledge about the technology quickly spread throughout the booming advertising industry on the West Coast. "Sign of The Times" writer William Hugh Gordon, originally from Canada, also seems to have been the first to use a basic photochemical process to create his screens.
In the 1917 National Advertising Exhibition in St. Louis a special exhibition was showcased with about 200 objects produced using screen printing. Around the end of the First World War, companies in Australia, Canada and occasionally also in Europe began to produce screen prints as licensees of the US technology.
CAPTION: Screen printing plant in Finland, 1948. Photo: The Finnish Museum of Photography / Photographer unknown
Consumables as a technology driver
In the period between the two world wars, screen printing crafts and machines developed considerably, especially in the USA. For example, wooden frames would have been replaced by metal frames, especially in textile printing with water-based inks. Cheesecloth, the first, quite coarse screen fabric, had to give way to the finest Swiss silk gauze. Until after the end of the 2nd World War, silk gauze was widely used for screen printing. Then it was gradually replaced by Organdy and fabrics from Nylon and Polyester, as these are more robust and dimensionally stable.
Screen printing was such an attractive market niche for the producers of silk gauze that they co-financed a Selectasine licensing office in Berlin in 1928. However, Selectasine Berlin not only sold licenses, but was also a manufacturer of graphic screen prints itself with cylinder printing presses borrowed from Selectasine's London office. Around 1934, Selectasine Berlin got into financial difficulties and had to close.
Although screen printing was not yet widespread in Europe, the Hermann Pröll company had been producing oil-based inks for sign printing since about 1926. To this day, Pröll GmbH in Weißenburg is considered a world leader in the development of special screen printing inks. Marabu, a paint manufacturer for more than 150 years, today at Tamm (near Stuttgart), only launched its first line of screen printing inks, Marapid A, in 1952.
CAPTION: A member of the 1st Topographical Survey Unit, screen printing maps of the province of Phuoc Tuy (1968) Photo: Copyright expired - Public Domain
Screen printing in the war
The Great Depression of the 1930s initially proved to be rather positive for graphic screen printing in the USA. Many people who could no longer afford original art decided to use cheaper screen-printed art reproductions instead.
But when the USA entered the Second World War in 1941, the advertising industry was hit hard. Important raw materials were immediately rationed, skilled personnel drafted. In the war economy, however, many new applications quickly arose for the versatile screen printing process. This ranged from lettering for vehicles, ships and aircraft to maps and camouflage patterns for uniforms. Even simple electronic circuits were already manufactured in the USA from 1943 onwards with the help of screen printing.
In addition, many screen print posters for military and civil purposes were created in the USA and in Great Britain. These are probably the reasons why in continental Europe it is widely assumed that screen printing arrived only with the US troopers.
CAPTION: Contemporary screen printing line with multiple inking units. Photo: S. Angerer
Screen printing after the Second World War
In Western Europe, screen printing gained traction in the early years after the end of the Second World War. Especially in the 1950s, 1960s and the 1970s, many screen printing printers were founded focusing not only into graphic arts but also serving the growing textile industry.
In addition, industrial screen print established itself as part of the production of consumer and capital goods, e.g. in automotive and mechanical engineering. Later, Screen printing also proved to be ideal for printing on promotional items as promotional gifts grew more important in the advertising mix, especially from the 1990s onwards.
Quite a few established printers were originally founded as screen printing companies one or two generations ago. In addition, new manufacturers of screen printing machinery such as Alraun, RokuPrint or Thieme emerged in Germany, until the 1990s.
CAPTION: Signage made with screen printing process. Photo: S. Angerer
Conclusion: Screen printing is still a popular printing technique
From the mid-nineties, screen printing lost a lot of its volumes as wide format digital photo, and later digital printing took over. These technologies were better suited for many popular applications, more flexible and cost-effective. As a result, until the 2010s, many screen printing lines in the graphic arts industry were replaced by fast, industrial grade digital printing machinery.
Even Serigraphy (art screen printing and art reproduction) faced considerable competition from inkjet Fine Art Printing. Today, the demand for screen printing seems to have stabilised. This is especially true for industrial screen printing. In many cases, special pastes or coatings are still very hard to use in inkjet printing.
But screen printing has also been able to defend some niche in the graphic arts industry, for example in finishing with special coatings. Rotary screen printing is also still in high demand for large textile printing run-length.
In recent years, hybrid combinations of screen printing and digital printing have led to appealing results, for example in the production of packaging. So, it looks like the history of screen printing will continue to unfold well into the 21st century...
Discover the latest innovations in screen printing at FESPA Global Print Expo 2025, Europe's leading print and signage exhibition taking place from 6 - 9 May at Messe Berlin, Germany. It will showcase the most innovative products, visionary concepts, and latest developments in the future of print. Register to visit here and use promo code FESJ505 and only pay 50 euros for your entrance ticket.
Topics
Interested in joining our community?
Enquire today about joining your local FESPA Association or FESPA Direct
Recent news
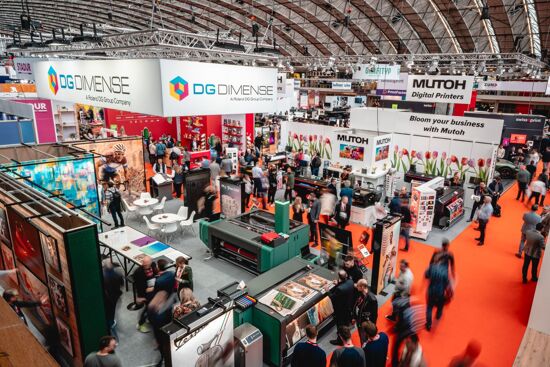
FESPA 2025 Feature Programme confirmed: both new and returning
FESPA Global Print Expo 2025 is set to introduce its newest editions to its feature programme, SmartHub and the ESE Pavilion, as well as welcome the return of existing features: the 2025 FESPA Awards; the high-adrenaline World Wrap Masters competition; and the Club FESPA Lounge.
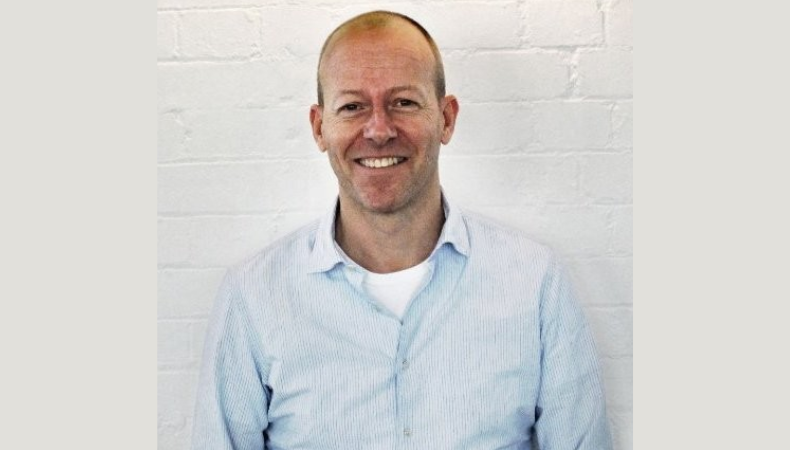.png?width=550)
My Personalisation Experience
Richard Askam, a pioneer in Personalisation, transitioned from the drinks industry to creating iconic campaigns like Coca-Cola's "Share a Coke." His speaking career, includes leading a TEDx talk, becoming an ambassador for FESPA . In the past, he has led the conference sessions for the Personalisation Experience" conference, and will return this year to speak in a panel discussion.
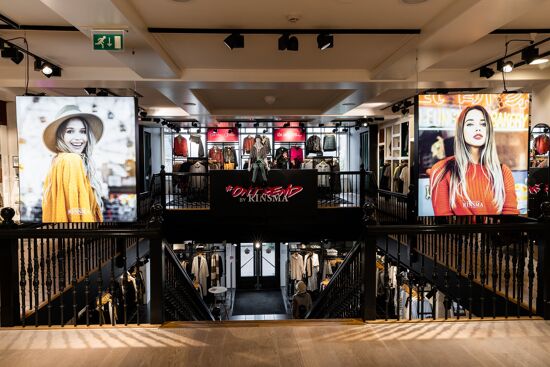
What Does LED Lighting Do for Your Textile Frame?
LED lighting transforms textile frames, enhancing visibility and colour vibrancy for impactful displays. At European Sign Expo 2025, EFKA will showcase innovative illuminated and non-illuminated frames, including 3D and modular designs. LED's energy efficiency and storytelling potential make them crucial for modern visual communication.