Understanding ceramic and glass decorating - Inks
FESPA UK's Peter Kiddell provides a run-down of inks used in glass and ceramic printing, in the first of a two part series.
In the UK we have a history of applying images to all types of glass and ceramic surfaces mainly centred around Stoke on Trent where all elements of the techniques have been developed and refined.
Companies such as Wedgwood, Royal Crown Derby, Royal Doulton etc. have developed a proud history of printing onto ceramic ware using screen printing, pad printing and lithographic printing. It is screen printing and pad printing that will be considered in this article.
In more recent times digital printing technology has been adopted for ceramic tile printing and the creation of short run ceramic transfers. None of these processes are to be confused with the use of sublimation inks that are transferred onto polyester coated ceramics, glass and other materials.
In graphic applications mechanical abrasion is one aspect and resistance to chemicals is another. The favoured technique for many years has been to use pigments that are fused to the surface at high temperatures. These pigments were inorganic.
As the environmental impact of the process and the pigments make them fall out of favour organic pigments that are adhered to the surface are becoming more popular. Starting from the point that pigment is the part of the ink that gives the colour, what is the difference?
Inorganic Pigments
Inorganic pigments are derived from mineral compounds. They are normally oxides or salts of one or more metals. They are resistant to temperature, sunlight, chemical and mechanical attack. Their downside is that they used to be made from Lead, Cadmium, Chrome and other heavy metals along with Zinc, Tin etc.
This means they potentially present a health and environmental hazard. Some are still used but the heavy metals of cadmium, chrome and lead have been substituted with much safer materials. Inorganic pigments cannot be dissolved in conventional solvents.
Organic Pigments
Organic pigments come from plants either in their natural state or when they have been converted into oil and its derivatives. The pigments all contain Carbon which means an almost limitless range of colours can be formulated, these colours can be very vibrant, even fluorescent.
Organic pigments are not good at providing true metallic colour unlike inorganic pigments. Organic pigments will normally be formulated into inks that consist of resins and solvents or, in the case of Ultra Violet systems, without solvents.
Inorganic inks or enamels are a mixture of glass particles (frit) pigment, solvents, waxes or oils and additives.
It is possible to use metallic pigments in organic resins and the effects can be close to enamels but the mirror finishes are only possible in specialist applications where the metallic ink is printed on the back of a high gloss plastic sheet. This is not suitable for printing onto glass or ceramic. If you want true metallics on glass or ceramic you will have to use inorganic enamel (ink/colour).
Thermoplastic Inks
As well as the types of inks shown above; when using inorganic inks/enamels there is an option of using what is known as Thermoplastic Ink. This is an ink system that at ambient temperatures is a wax like solid.
When the temperature is increased to 65-70oC (sometimes higher) the wax liquefies and depending on its composition and temperature, will have a viscosity between 800 and 2000 Cp. Thermoplastic ink is particularly useful when printing multi-colours as when the warm ink contacts the cold ceramic or glass it hardens quickly so additional colours can be over-printed.
The normal method of heating the ink is to pre-melt it and pour it onto a stencil made from steel mesh. The mesh has a controlled electric current passed through it, it heats up and maintains the ink in a fluid printing state.
The system is so efficient that it is possible to print multiple colours on glass bottles at rates up to 7000 per hour. It is necessary to have the correct insulated frames onto which the mesh is mounted and proprietary equipment to control the electrical current passing through the mesh. Do not consider rigging this up without advice from a specialist!
This method is also used on ceramics. In both cases the printed item has to pass through a lehr in the case of glass or a kiln if it is ceramic. Both a lehr and a kiln must be very carefully controlled regarding speed, with a lehr, temperature profile and internal atmosphere, otherwise colours will change and images distort.
The use of inorganic enamels, that are either thermoplastic or liquid, can use a great deal of energy. A far cheaper alternative is to use organic pigment based inks that are not fused by glass frit onto the surface of the glass, ceramic or under the glaze.
Organic pigments would not withstand the temperatures to melt the glass frit in the ink but they require a fraction of the energy to cure.
Organic based inks that are cured by heat used in this application are reactive inks that use a catalyst to achieve a hard chemical resistant surface and baking inks that need elevated temperatures 120 to 150'C that trigger a chemical reaction.
Ultraviolet Curing Ink systems are gaining a considerable foothold in glass decoration. Instant UV curing means that multi-colours are possible and adhesion, along with chemical resistance, is such that items printed with this system will withstand dishwashing many times over.
Bottles, glasses and other glass objects are now printed this way but it will not give you the mirror gloss metallics achievable with inorganic metallic pigments. UV curing inks cannot be applied for under-glaze applications as the pigments would be destroyed by the firing of the glaze.
Topics
Interested in joining our community?
Enquire today about joining your local FESPA Association or FESPA Direct
Recent news
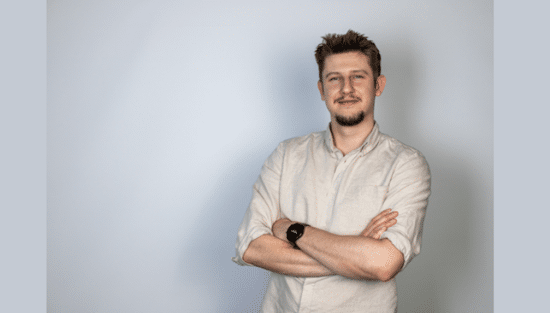
GenAI + POD: The Smartest Way to Add Personalised Products to Your Retail Offering in 2025
In 2025, GenAI and POD are transforming retail. Masterpiece AI empowers businesses to offer unique, AI-generated personalised products, from apparel to home decor. Customers use text prompts to create custom designs, streamlining production and boosting sales. This revolutionises customer experience and product offerings.
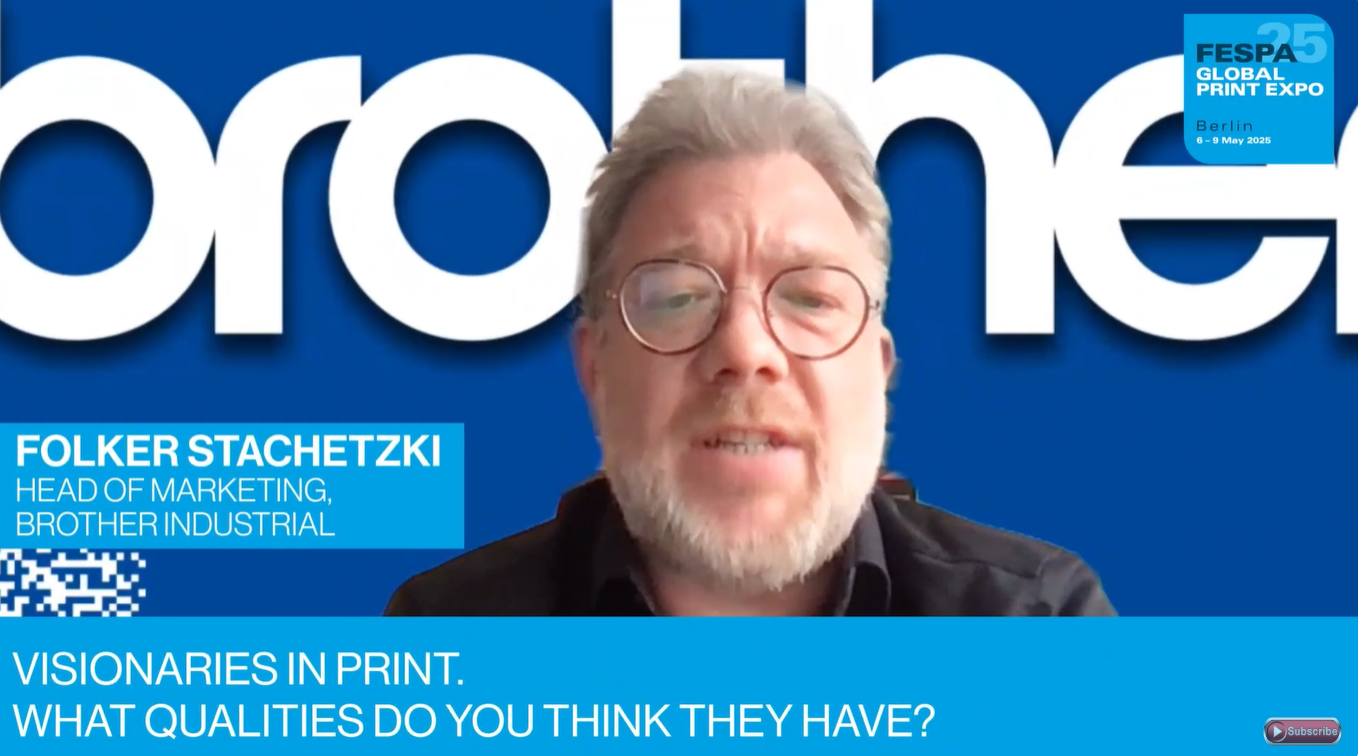.png?width=550)
What qualities should visionaries in print have? With Folker Stachetzki from Brother
We speak to Folker Stachetzki, Head of Marketing at Brother about visionaries in print.
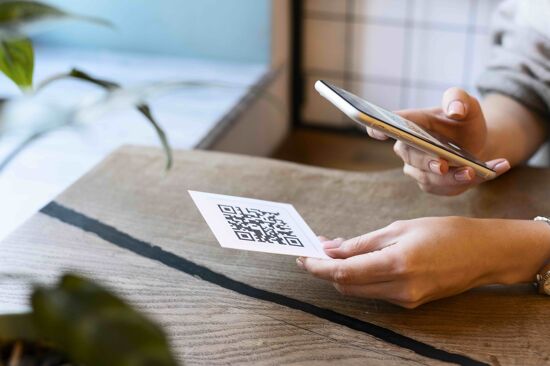
Bolstering personalisation by combining print and digital technology
Using printed material in combination with digital technologies offers more opportunities to those offering personalisation to customers. Rob Fletcher shares some recent examples of the print and digital working together to enhance the impact of personalised pieces.
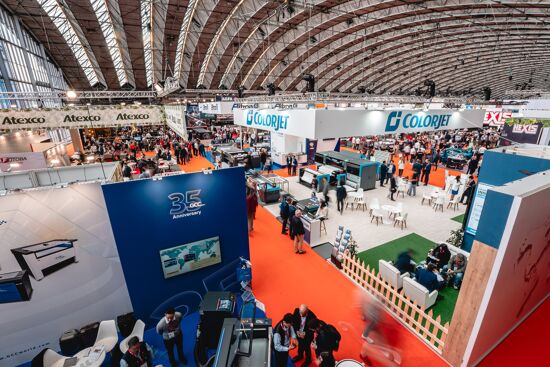
European Sign Expo to highlight developments shaping the future of signage and visual communications
European Sign Expo 2025 (6 – 9 May, Messe Berlin, Germany) is weeks away and a host of leading exhibitors are all set to welcome Visionaries from across the signage and visual communications industries to their stands.