What is the difference between labels and packaging regarding narrow web printing?
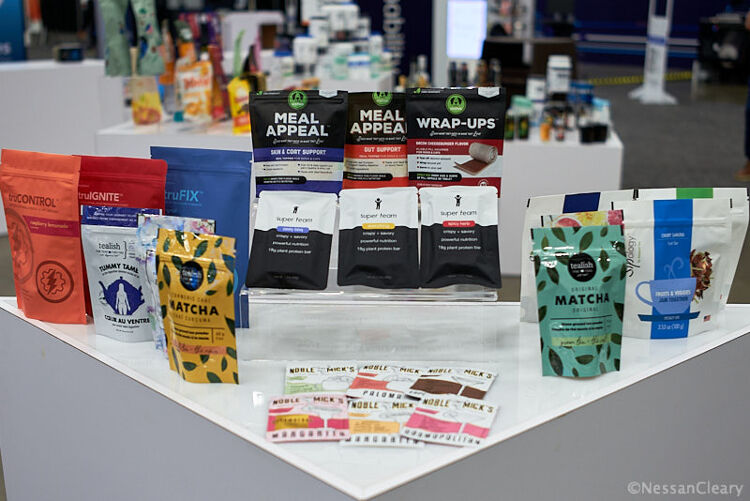
Nessan Cleary shares how labelling has always been distinct from packaging but increasingly lines are becoming blurred between them.
One of the more surprising aspects of recent Fespa trade shows is the number of label presses that have started to appear. This is partly because many vendors selling wide format equipment also serve the label industry, and partly because many print service providers see labelling as a viable path to diversifying their business. The first generation of digital labelling presses were narrow web machines that aimed to offer a short run capability to label converters. But many of the latest digital label solutions go beyond this and are now targeting the short run packaging market as well.
In terms of narrow web printing, the main differentiator between labels and packaging as applications lies in the print width. Early inkjet machines mimicked the 240mm width of older flexo label presses. But today most digital label presses are around 340mm in width and we are starting to see wider machines of 440mm and even 510mm. This allows for higher productivity as you can place multiple label tracks side by side. But more importantly, the wider the press the more packaging applications it can handle.
The most common of these applications is for pouches, which can be used for a wide variety of applications, from snacks and pet food to refills for liquid soap dispensers. Pouches are generally seen as a cost-effective form of packaging for liquid items, such as soups, but also for other foods like microwavable rice, and they can even be used for solid items such as ink cartridges for home printers. The pandemic proved the viability of digitally-printed pouches because it allows brands to switch their production quickly as consumer demands change.
HP's Indigo 200K is a web-fed B2 press suitable for both labels and packaging print. ©Nessan Cleary
Most pouches tend to be quite small, typically around the size of a crisp packet, so a label press with a print width of 330mm to 350mm is quite wide enough for many of these applications, and certainly a good starting point.
There are a number of technology changes that are filtering through label presses that will also benefit packaging. The most obvious of these is the anticipated switch from UV-curable inks to water-based inks. This will benefit food packaging because there is a risk with UV inks that some chemicals, mainly from the photo-initiators used, will migrate through the packaging to the food inside. Many label presses offer low-migration UV inksets to counter this but water-based inks would eliminate that risk. Several vendors have hinted at developing label presses with water-based inks but we have yet to see many such presses actually available yet. It’s worth noting that this will also drive the development of resin or latex inks for the wide format market.
The print speed of narrow web digital presses has improved but is still much slower than the equivalent flexo presses. So moving to wider widths can also help improve the overall productivity by imposing multiple label tracks side by side, as well as opening up the more profitable packaging applications. Nonetheless, the average print speed is around 70mpm, though some digital devices can reach 100mpm. However, many flexo devices can run at over 200mpm.
Another issue is print resolution, with most digital label presses printing at 600dpi. However we have already started to see a new generation that are capable of 1200 dpi resolution, and this is clearly the direction that the label industry is moving in. There are too many digital label presses to list them all here, but as an example, Durst makes the Tau range of industrial label presses, which includes the top of the range Tau RSCi. These use Fujifilm Samba printheads and can produce 1200 dpi resolution at 100mpm. The standard model has a 330mm print width but it’s also available in 420mm and 510mm widths. The base configuration uses CMYK inks, but there are also options to add orange, violet, green and white which are particularly useful for packaging as brands prefer to have the wider colour gamut to accentuate their product images.
Inkjet may be the dominant digital technology but there are alternatives. HP Indigo sells the 200K, a web-fed machine that takes media up to 762mm wide and bridges the gap between labels and packaging. It uses liquid toner rather than inkjet and will print to both flexible films such as PET, BOPP and PETG as well as PE label stocks.
The Oki 9542 toner printer forms the print engine on this roll to roll label solution. ©Nessan Cleary
At the other end of the scale, Oki has demonstrated printing to blank pouches on its Pro 9542 dry toner printer. This was designed originally as an affordable office copier but has proven quite adaptable to a number of commercial print applications. As with most toner printers, it’s not particularly fussy about the substrates though you should test the materials you want to use beforehand as some may be sensitive to the heat from the fusing unit. It won’t print full bleed, but does include white and there’s a reasonable range of blank pouches available.
Another common trend is towards more hybrid presses that combine digital with flexo units, particularly so with wider label presses. Often the digital print is used to provide the basic CMYK colours with the flexo units then adding special effects such as foiling. Thus Bobst has developed a hybrid label press, the Digital Master, which uses inkjet printing for the colours with customers free to specify which flexo units they want for special effects and some converting. This is available in both 330mm and 510mm widths.
Besides the printers, you’ll also have to factor in the converting machinery. There are a number of label converting devices that offer an all-in-one approach with a number of different converting processes. But when it comes to packaging, you’ll likely need a dedicated converting line for each type of packaging.
The most common packaging application for label presses is pouch making, which includes several steps. Once the graphic has been printed onto the base layer, the next step is to laminate a further layer, which will vary from one application to the next. Typically these layers will add specific functionality, such as adding oxygen inhibition to preserve the shelf life of foodstuffs. This will be followed by slitting, to split the individual pouches from the roll. Then the pouch is formed, folding the material to form the two sides and then sealing those sides. From here the empty pouch can be sent to the filling line, where it will be filled and a closure added. That might involve adding a base so that the pouch stands up, or a spout for easy pouring.
In conclusion, investing in a label press is not a simple affair. Apart from the press, you will also need the design and workflow software and the finishing line. But the potential rewards are huge, particularly if you factor in the packaging market as well as labelling so it certainly makes sense to consider this as an option to diversify and future proof a business.
To discover the latest content that covers a wide range of sectors including label printing and packaging sign up for FESPA’s free monthly newsletter FESPA World available in English, Spanish and German.
Topics
Interested in joining our community?
Enquire today about joining your local FESPA Association or FESPA Direct
Recent news
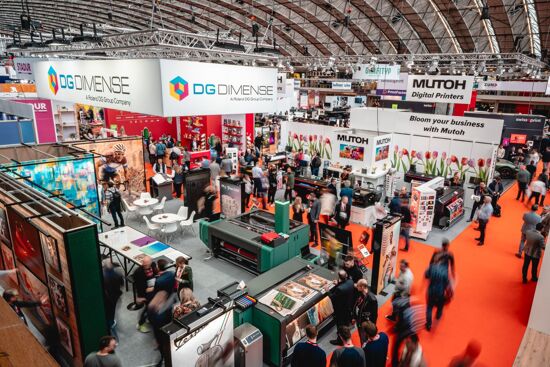
FESPA 2025 Feature Programme confirmed: both new and returning
FESPA Global Print Expo 2025 is set to introduce its newest editions to its feature programme, SmartHub and the ESE Pavilion, as well as welcome the return of existing features: the 2025 FESPA Awards; the high-adrenaline World Wrap Masters competition; and the Club FESPA Lounge.
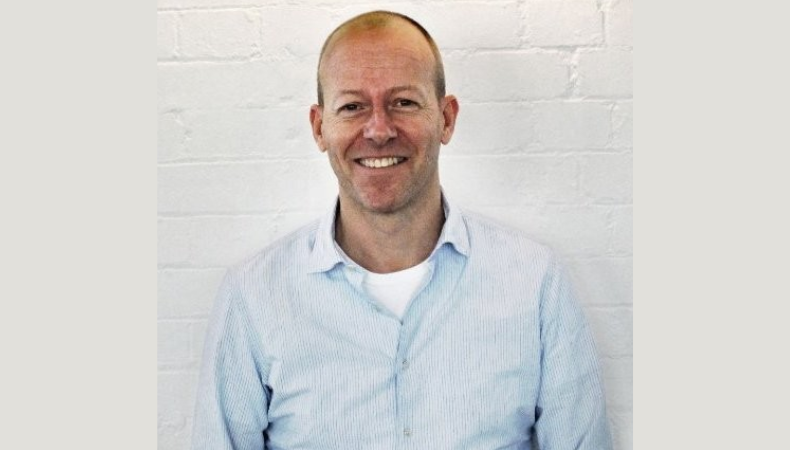.png?width=550)
My Personalisation Experience
Richard Askam, a pioneer in Personalisation, transitioned from the drinks industry to creating iconic campaigns like Coca-Cola's "Share a Coke." His speaking career, includes leading a TEDx talk, becoming an ambassador for FESPA . In the past, he has led the conference sessions for the Personalisation Experience" conference, and will return this year to speak in a panel discussion.
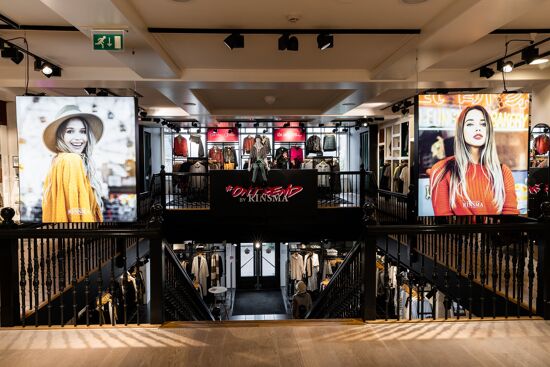
What Does LED Lighting Do for Your Textile Frame?
LED lighting transforms textile frames, enhancing visibility and colour vibrancy for impactful displays. At European Sign Expo 2025, EFKA will showcase innovative illuminated and non-illuminated frames, including 3D and modular designs. LED's energy efficiency and storytelling potential make them crucial for modern visual communication.