Latest innovations for Apparel and Décor Roll to Roll Textiles using Pigment Inks
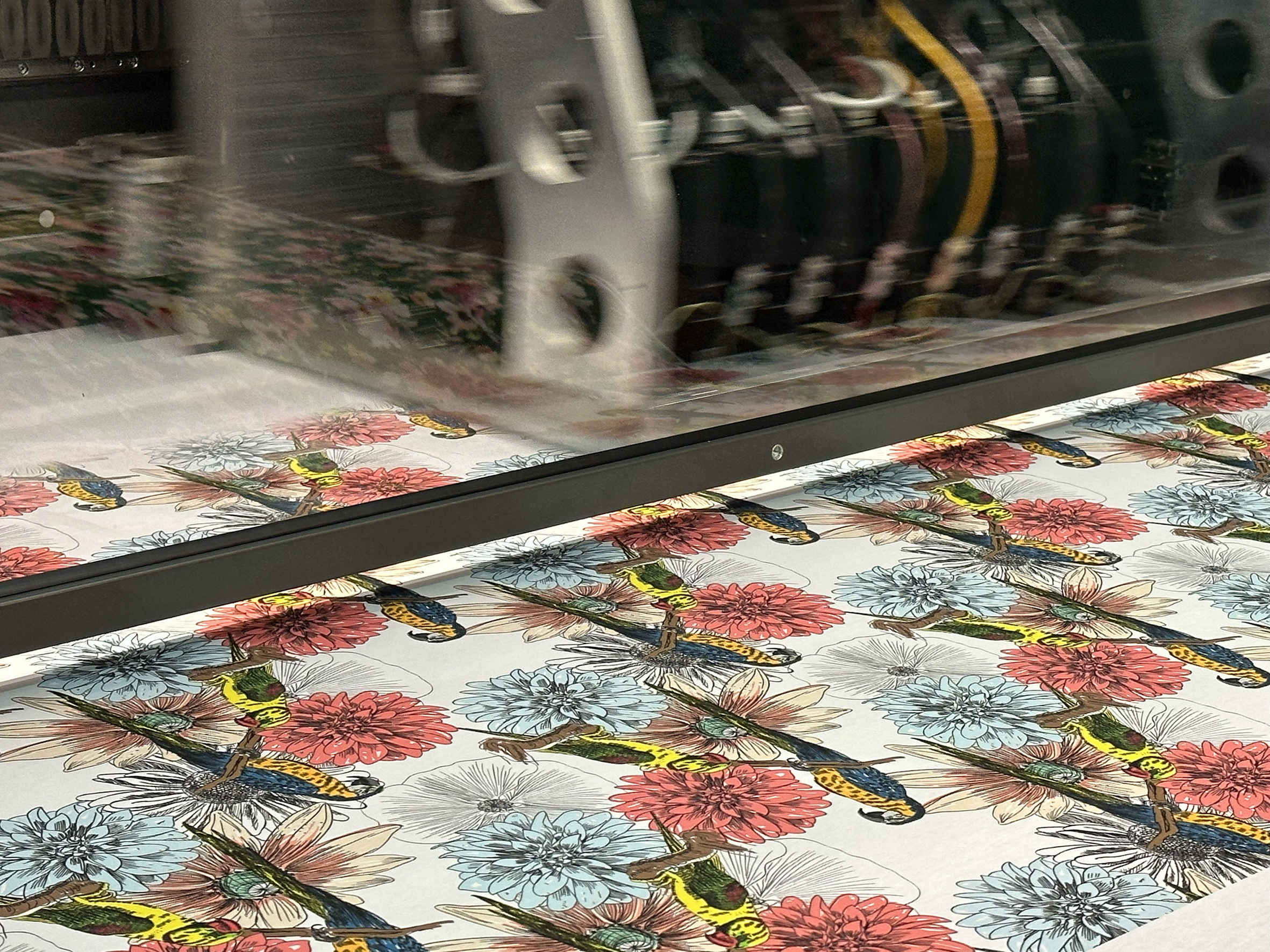.jpg?width=750)
As digital textile printing continues to evolve the technology and chemistry now facilitates high speed production across multiple ink sets. These Innovations now enable pigment inks to be jetted at high speed, and the sector is set for a disruptive chapter.
Pigment inks represent the largest opportunity for conversion from analog to digital process and as such offers the digital sector an unrivalled opportunity. Offering environmental efficiency, the pigment ink print process provides a truly one-step solution to the print process, delivering a massive hike in speeds from 50 metres/hr just a few years ago - to over 1800 metres/hr using the latest scanning machines.
Previously, with anything up to seven steps, digital textile printing was a complex and technically demanding process, demanding high energy and pre and post-finishing equipment. When using Reactive, Acid and Disperse inks, digital printing still requires pre-coating, drying, printing, steaming, washing, drying, finishing and drying again, a truly involved process which not only consumes time and energy, but also water and effluent.
As stated, In the larger world of analog textile printing, pigment inks already enjoy the lion’s share (over 65%) of the inks used, however to date – this is not yet replicated in digital textile printing, where less than 10% of machinery currently uses pigment inks. Historically, this was because the original pigment inks available had large particle sizes that were incompatible with available printheads, as well as not giving good fastness results, and in, all cases a separate pre-print coating had to be applied as well as a post-print thermofix and softener. These extra processes combined with the slower speeds made digital pigment printing unattractive.
Caption: “Epson’s Monnalisa range of machinery continues to develop and meet the challenges of printed production stating “Reliability is a key factor when it comes to the real world of daily production.” Credit: Epson
Yet as the years have passed, innovations in Inks, process and printheads have made a one -step digital printing process a reality that is now taking the market by storm. The sector is primed for digitisation.
With the development of novel pigment ink formulations by companies such as Kornit Digital and Dupont Artistri, the homogeneity, stability and volume velocity issues attached to early pigments have been overcome. Below we highlight the growth of the sector and the machinery available.
Kornit’s patented NeoPigment™ ink which delivers a one-step pigment printing process, with no need for pre or post treatment has been developed in-house by chemistry experts specifically for use in digital fabric printers and provides an unprecedented colour gamut, the ability to print any design, in any number of colours, on any fabric base.
At Dupont,the new Artistri® P5500 ink set delivers improved wash fastness with both press or oven curing and with faster curing times. This high gamut volume aqueous-based inks package is designed to work in printers with low-viscosity piezo-electric printheads and is suitable for all DTG applications, including DTF (direct to fabric) printing.
Yet, the largest leap forward has been in the development of printheads, here Xaar, Epson and Ricoh are driving the adoption of inkjet.
Xaar’s Ultra High Viscosity Technology the Aquinox is capable of jetting fluid viscosities of up to 100cP. By enabling a wider colour gamut and fluids with larger particles and more pigment for higher opacity, colours are more vibrant and whites and blacks.
Meanwhile the new Epson I3200(8)-S1HD and S800-S1 printheads are compatible with a wide variety of inks used for industrial applications. In addition to aqueous, UV-cured, and eco-solvent inks, they support oil-based, solvent, and other types of inks for digital printing applications in production printing. The I3200(8)-S1HD can handle up to eight colours of ink and deliver resolutions up to 1200 dpi, enabling the rendering of high-resolution images in a variety of situations. The S800-S1 is equipped with only one chip. Its compact design helps to improve productivity in printing environments where space is limited.
At Ricoh three newly developed industrial-grade inkjet printheads, RICOH MH5422, RICOH MH5442, and RICOH MH5422 Type A, provide high image quality and productivity by utilizing Ricoh's high-precision technology. They feature a wide range of ink compatibility and improved durability through enhanced nozzle surface abrasion resistance. Ricoh has also improved system compatibility by applying separate cables and high-precision surface alignment features.
Finally, beyond inks and the printheads - the industries machinery manufacturers now offer the pigment printing market a number of innovative solutions that address key challenges. Resetting printed pigment production in-line with sustainable, efficient manufacturing.
Caption: The next generation of COLARIS printers comes with the Seiko RC1536 printhead generation with lower energy consumption. Credit: Zimmer Austria
At Kyocera the FOREARTH eliminates virtually all water usage from the textile printing process, but it also reduces energy consumption and CO2 emissions during printing because it does not require the largescale equipment traditionally used for pre- and post-treatment of textiles. It is an all-in-one printing system that uses new patented inks, pre-treatment fluids, and finishers that are sequentially applied by inkjet printheads to the material.
Pigment inks, according to the company, provide soft prints and high durability on a wide range of fabrics. In addition, FOREARTH achieves a soft hand-feel for prints – an essential feature for the fashion and textile industries – and enables highly detailed printing on diverse fabrics, including cotton, silk, polyester, nylon, and blended fabric.
Epson’s Monnalisa range of machinery continues to develop and meet the challenges of printed production stating “Reliability is a key factor when it comes to the real world of daily production. Every issue/inefficiency causes downtime or quality flaws, all costing you money and credibility. Monna Lisa's features help you keep production going: selectable channel configuration, high accuracy, PrecisionCore print head array, ink management, continuous wrinkles check and head cleaning, RGB auto balancing, fabric feeding system... Every single piece of technology is designed to solve real problems and rearrange on your needs, to give you the smoothest manufacturing experience.”
MS Printing Solutions and JK Group’s new system have put the technical excellence of their JP7 Digital textile Printer together with the patent pending JK Digistar Pigment 4K inks.
Since the new JK ink formula doesn’t require pre or post treatment it reduces the printing process steps by 50% while at the same time reducing water consumption by 95% against comparable Acid or Reactive printing. With a huge reduction in CO2 emissions, these inks provide excellent wash and rub fastnesses, as well as being kind to the environment with full Eco-passport certification.
The re-born JP7 for Pigment ink printing now boasts an Ink Recirculation System, and a novel Nozzle Shooting System that protect inks from flocculation which, when combined with the new Gradus dryer give a completely efficient one-step Digital Textile Printing System.
Now, with the new NeoPigment™ Robusto Softener, the Kornit Presto is a complete solution for printing, softening and drying in a single step. With no water waste and in the most smart and sustainable way, the Presto gives a solid market reach to a wider range of applications. From fashion, baby textiles to home décor, the Presto provides high quality prints, vivid colours and great hand-feel to multiple fabric types, on-demand. With the addition of the Robusto Softener application, the Presto now combines soft handle with vivid colours across the widest range of fabrics including natural fabrics and blends.
From Optimum Digital – the Nirvana Belt, offers a waterless textile printing solution without pre and post treatment, and contributes to the protection of rapidly decreasing clean water resources and reduces the production costs for the printer. The new technology eliminates the need for pre-treatment (paste) and post-printing processes required by traditional textile applications, thus completely avoiding the intensive chemical use and water consumption during these processes. This sustainable textile printing solution is stated to reduce the overall print cost by 50% and energy and chemical costs by 80% in addition to conserving natural resources and preventing wastewater generation.
The EFI Reggiani ecoTERRA machine continues to disrupt analogue production. Environmental efficiency is at its core. With a small footprint this machine delivers an extremely efficient solution for industrial scale production supported by high-tech design, on-board workflow, environmental efficiency, alongside analytics and data capture. Supported by a suite of ink options, the ecoTERRA offers (and highlights) the redesign of textile production. Speaking of the ecoTerra Micol Gamba commented “The EFI Reggiani ecoTERRA is the all-in-one solution for pigment printing that requires no ancillary equipment for pre- and post-treatment.
The solution gives customers competitive advantages by dramatically cutting energy and water consumption of the overall process for a more sustainable direct-to-fabric printing experience. Eco-friendly design, and water-based ink delivers excellent wet and dry fastness properties, remarkable sharpness in detail and extraordinarily high durability while also yielding longer printhead life with reduced maintenance costs. Thanks to our enhanced polymerisation and finishing unit, EFI Reggiani ecoTERRA also provides the fabric softer hand feel.”
Zimmer Austria recently introduced the new Colaris printer series with around 16 color groups. The next generation of COLARIS printers comes with the Seiko RC1536 printhead generation with lower energy consumption. A newly designed ink circulation system without need for a vacuum ensures a stable print run and high-quality print results. With the COLARIS Printing System from Zimmer, an outstanding pigment print can be achieved, as well as effective pre- and after treatment.
In summary – Digital Pigment printing is to disrupt the textile printing sector, as more manufacturers onboard the move to one step digital textile printing as a means to achieve speed to market and speed of production.
Speeds and fastnesses are up, overcoming some of the main barriers to growth in the pigment ink market for digital textile printing. And with industrial printers everywhere wising up to the harness the advantages of pigment over reactive/acid/disperse printing, at the current rate of growth - over 16% p.a – Pigment printing is expected to advance significantly in the coming years.
Discover the latest innovations in interior décor and textile printing at FESPA Global Print Expo 2024, Europe’s leading print and signage exhibition. Taking place from 19th – 22nd March 2024 at RAI Amsterdam, Netherlands. Register here to visit and use promo code FESJ401 for a 55 euros discount.
Recent news
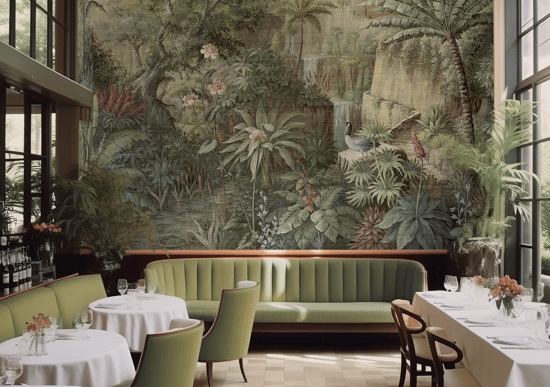
Industry Insights, Design Trends and Disruptive Innovations for Interior Decoration
Debbie McKeegan shares key trends and innovations in the interior decoration industry taking place and demonstrated at recent European exhibitions in Germany and France. The interior decoration industry is adapting to challenges like overstock and supply chain disruptions by integrating digital and traditional methods, aiming for more agile and environmentally friendly solutions.

Bridging Design and Technology: The Story of Western Sensibility an interview with Kathryn Sanders
In this podcast episode, Debbie McKeegan interviews Kathryn Sanders, the CEO & founder of Western Sensibility, a US based company that merges interior design with digital printing technology. They discuss the origins of the business, its innovative services, and the importance of sustainability in the textile industry.
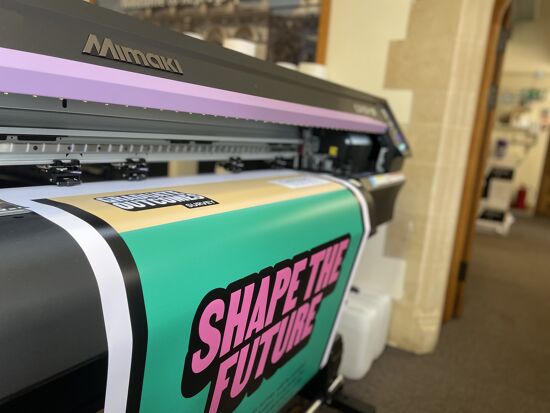
How to choose the right machine for indoor print
With interior print one of the stand-out growth areas of the industry in recent years, it is crucial printing companies select the right equipment to achieve the best quality results. Here, Rob Fletcher picks out some of the machines best suited to this work.
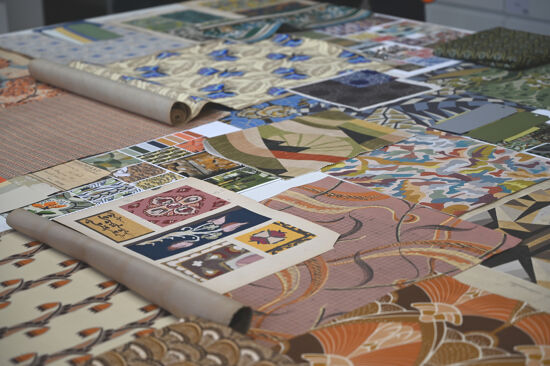
Resilience, Innovation and Heritage: The 100-Year Journey of the Standfast & Barracks
Renowned textile printing facility, Standfast & Barracks celebrates 100 years who are known for their expertise in rotary, flatbed and digital printing techniques. Debbie McKeegan looks at the history of the company and speaks to Lisa Montague, Managing Director about how they have adapted over the years and their future plans.