Packaging technology cuts emissions
That headline might suggest some major advance in printing methods, or perhaps some clever new substrates.
But in fact the way packaging technology can reduce emissions is by taking a machete to waste volumes.
There is a lot that can be done in the supply chain to cut waste, and this is where packaging advances come into the picture. As much as 35% of food produced ends up being thrown away, either because it is too manky to offer for sale or because it has gone off while sitting on the shelf.
According to the United Nations this amounts about 1.3 billion tonnes of food per year. Wasting food also wastes the resources used to produce it in the first place. Anything we can do to get more food to market and consumers in a fit state for use has to be a good thing. But it isn’t all we can do.
We can make much better use of the food we produce and do manage to get into the shops, especially in developed markets. For a start we can stop buying more food than we are likely to consume, so that we don’t let it rot in the fridge only to be thrown in the bin.
Apart from being a waste of money, overbuying of foodstuffs encourages us to eat more than we need, so we get fat as well as being wasteful.
Time is a constant series of changing events so the graphics industry needs to keep up with advances in packaging and of how packaging is perceived. Contrary to popular opinion packaging is not necessarily a source of waste. The primary purpose of food packaging should be to protect and preserve foodstuffs, so that they last as long as possible.
Shrink wrapping food prevents oxidation. Oxygen is a major cause of decay so if we can keep oxygen away from the food, it is likely to last longer. This applies to all types of foods from meat (which apparently gets tenderised as a result of being shrinked wrapped) and cheeses, through to vegetables packaged in individual portions.
An increasing number of food retailers in developing markets rely on shrink wrapping to lengthen the selling window for perishable goods.
The process involves heat applied with a heat gun or more commonly in a heated chamber, to polyolefin. This polymer is extremely heat sensitive so there is no risk that the food it contains starts cooking. It can be applied in several layers which may or may not cross-link depending on the material.
Either way the resulting package is robust, resistant to bugs and blocks exposure to oxygen, ensuring that foods is not contaminated.
With every tonne of food waste we produce, we increase the planet’s carbon footprint. Rather than seeing packaging as a source of waste, we should encourage people to recognise that it reduces waste and can ensure that more food reaches peoples’ plates. Something to chew on.
Topics
Interested in joining our community?
Enquire today about joining your local FESPA Association or FESPA Direct
Recent news
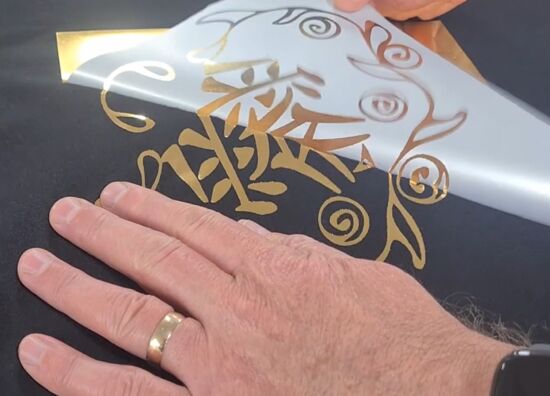
Special Effects in DTF Will Make Your “Prints” More Memorable
The DTF market is expanding with new vendors and innovations like multi-head printers enabling diverse ink options (spot, neon). Decorative films offer streamlined special effects. Keypoint Intelligence tested metallic and glitter films, noting varied ease of use and wash durability. New technology using adhesive and foil directly promises further creative advancements in DTF.
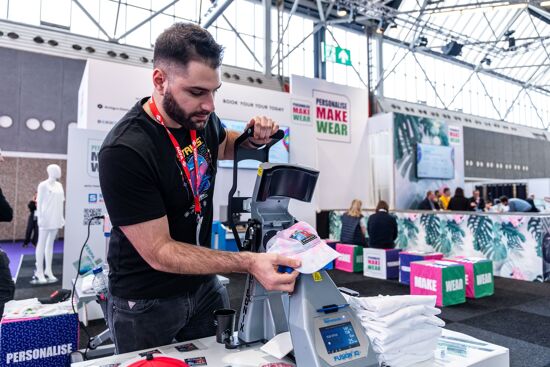
SmartHub – Expectations, opportunities and why you should attend!
The SmartHub at Personalisation Experience 2025 in Berlin will showcase personalisation and smart production opportunities across industries like textiles. Featuring a Smart Factory Trail with brands like Inkcups and Trotec, and a conference with experts discussing AI, mass customisation, and profit strategies, it offers insights into reducing waste and boosting efficiency through digital methods. Panel sessions will explore growth, automation in textiles, and smart manufacturing.
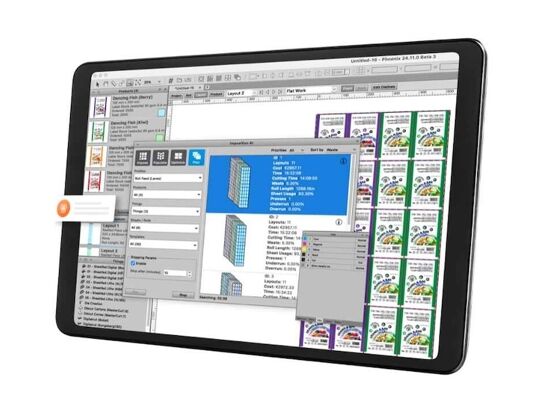
How is AI revolutionising Large Format Print?
Nessan Clearly discusses how AI in print relies on data pattern matching, already enhancing software for large format providers. He predicts that this will result in increased AI integration in workflow planning, job queue management, colour correction, image upscaling, and predictive maintenance via sensors and vision systems, ultimately streamlining operations and offering greater flexibility.
.png?width=550)
Why are FESPA events the ideal place for visionaries to meet? With Harold Klaren from EFKA
We speak to Harold Klaren, International Sales Manager at EFKA about visionaries in print. Harold shares why he believes FESPA events are the ideal place for visionareis to meet.