A preview of FESPA’s Technical Guides: an introduction to colour management and reproduction
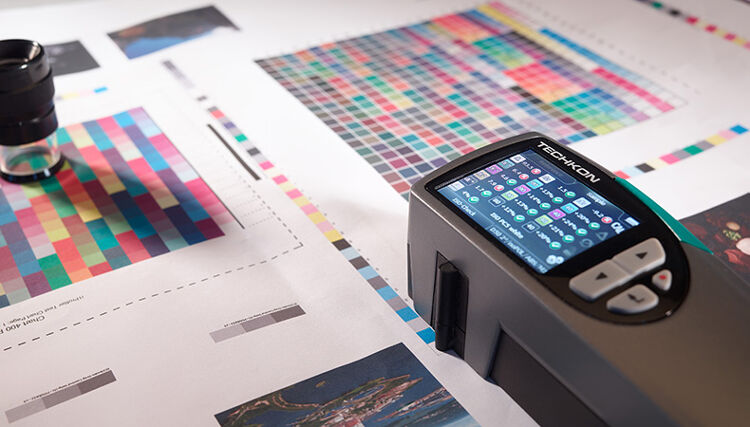
We take a look at colour management and reproduction in this preview of the second edition of the FESPA Technical Guides.
Colour management is one of the most crucial considerations in the printing process and a fundamental part of production. Accurate colour management is needed to transfer your job successfully from an initial file, through the process of digital editing, to its final form as a printed product.
At each stage, as the artwork file transfers from computer screen and through its workflow, accurate colour management presents a challenge. It is during the final element, reproduction – where colour management truly proves its worth: get it wrong, and your printing run could become expensive waste. However, the continuous advances in digital printing, inks, substrates and printing technology are making colour management more achievable and provides a basis for high quality predictable results.
FESPA’s introductory Technical Guide series aims to provide some useful insight for those who are considering entering new market segments or where their employees would benefit from a better understanding of the print landscape.
Light and colour
To fully understand colour management for the print industry, it’s important to realise how our eyes receive colour for our brains to interpret, and the influence of lighting conditions or colour temperature.
Colour is simply a function of how a surface absorbs and reflects light waves. In darkness, colour is irrelevant. However, as light is added, so shapes, textures and – crucially – colours become more discernible.
But it’s not entirely straightforward. Adding ink or varnish affects surface characteristics, leading to changes in colour appearance. Of equal importance, different lighting conditions influence our colour perception. Controlling the viewing conditions for both quality control and end use are essential for printers. Without an accurate understanding of lighting conditions prints become vulnerable to metameric changes. Therefore, establishing whether you need D50, D65 or TL84 becomes critical for successful printing quality control.
Understanding the spectrum
Under normal daylight conditions, the human eye can see a visible spectrum of colours starting with dark violet, then blue, green, yellow, orange and ending with dark red. But our individual understanding of colour is subject to how our eyes receive the wavelengths of light that our brains reveal as colours.
The human eye can distinguish more than 10 million colours, but the range of colours that can be printed with CMYK inks is more like 450,000 for most offset printing processes, with wide format digital printing systems using CMYK + OVG inks a gamut volume of almost 900,000 colours is possible.
While, for example, computer monitors use the Adobe RGB gamut when printing with CMYK inks the purity of their transparency impacts on the range of colours that they can produce when overlapping one another.
Digital colour
Understanding colour behaviour requires knowledge of the observer (viewer), the object (print) and its illuminant (light source) as they are the fundamental requirements to measure colour. The different variables in the production process, such as the white point of the substrate, ink colour shade and other printing parameters, need to be known and stable before creating ICC colour profiles. These profiles facilitate the conversion of colour from one device to another – that is, from a monitor to a printing press.
A spectrophotometer allows us to measure colours which can then be assigned as L*a*b* values that can be used in the colour management system. It’s the combined use of custom-made ICC colour profiles and an effective colour management system that enables quality matching across devices.
Making colour work
In 1993, to encourage industry-wide open colour management, Adobe, Agfa, Apple, Kodak, Microsoft, Silicon Graphics, Sun Microsystems and Taligen established the International Color Consortium. Now better known as ICC, this group created the system that uses ICC profiles for sharing characterisation data between colour input devices, output devices and colour spaces.
ICC device profiles simplify the translation and sharing of colour information between systems, helping with colour management and making colour accuracy more predictable and reliable. The use of ICC profiles embedded in images and PDFs across systems is now commonplace, and ICC characterisation data is regularly assigned to images and PDFs to ensure that they have the correct colour values.
ICC profiles are also used to define the characteristics of printing hardware and how colours can be expected to appear. Device calibration and characterisation makes sure that colour managed workflows can be automated for optimal performance, reducing colour errors and ensuring high quality prints, even across a variety of printing methods. It’s worth noting that there are alternative colour profile formats such as MMX that operate beyond the ICC standard and create very high-quality print production.
The five Cs of colour
Effective colour management can be ensured by applying the five Cs: Consistency, Calibration, Characterisation, Conversion and Checking. These stages should be used throughout the workflow – including with customers and agencies – starting with the monitors used to view colour files and ending with print output.
Consistency is about controlling processes and adhering to them. Calibration requires complete understanding of how your devices perform – for example if you specify a 40% cyan tint , the output device should print that. You then characterise the device by measuring output for different paper types, optimising the screen settings, ink amount and black generation for each one. Conversion involves using the device profiles in different scenarios. And the final stage, checking, ensures you have completed the previous steps correctly.
Only then can you be confident that your colour management processes are robust and colour reproduction consistent with the highest possible quality. However, with FESPA’s help and guidance, this complicated subject can become significantly clearer.
The second-edition Technical Guides are available free to all members via their FESPA Association or FESPA.
Become a FESPA member to continue reading
To read more and access exclusive content on the Club FESPA portal, please contact your Local Association. If you are not a current member, please enquire here. If there is no FESPA Association in your country, you can join FESPA Direct. Once you become a FESPA member, you can gain access to the Club FESPA Portal.
Topics
Recent news
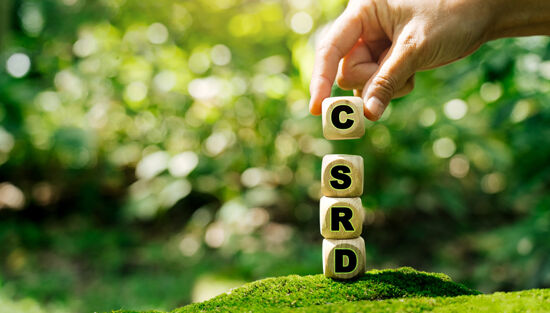
Regulation guidance: Corporate Sustainability Reporting Directive
The Corporate Sustainability Reporting Directive (CSRD) is now in effect, but with further changes on the horizon, what does it mean for printers? Sustainability consultant Rachel England outlines everything you need to know and talks to Apigraf about how your business may be affected.
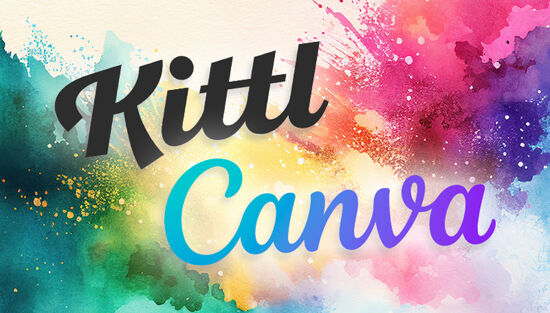
Web-to-print design: Canva versus Kittl
We look at popular design packages Canva and Kittl to determine how they compare regarding graphic design and print on demand.
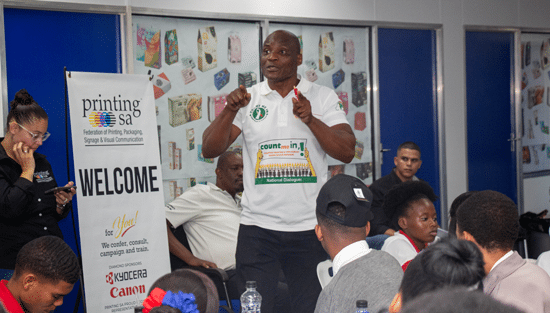
FESPA in South Africa: the print skills to thrive
Printing SA’s Career Day inspired young Cape Town learners to explore printing and packaging careers.
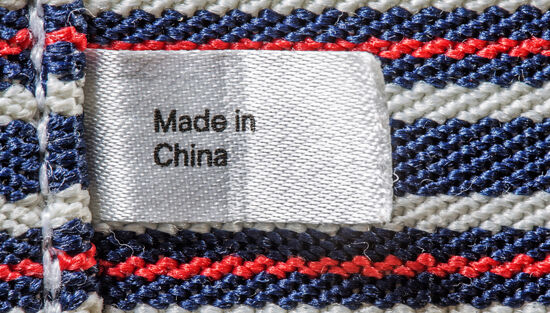
The rise of Chinese printers
Chinese printing companies are on the rise, and have their eyes set on the UK and EU marketplace. Some have made an instant impact; others are running into issues with maintenance and language barriers. What does the future hold for Chinese printing firms, and how can you navigate working with them?