Kornit: a new age in poly printing
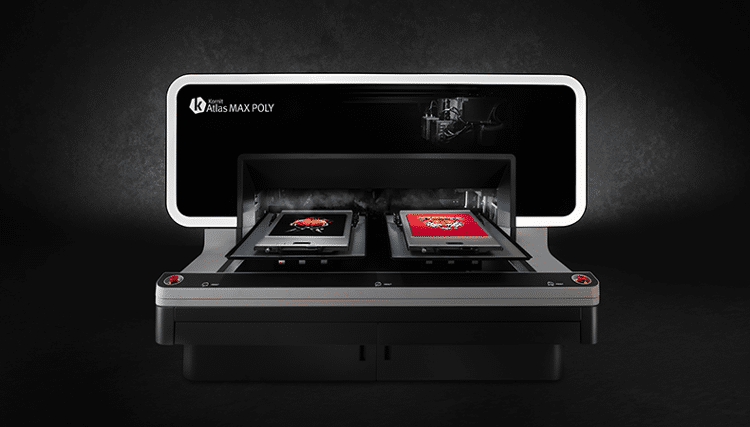
We look at Kornit’s Atlas Max Poly printer, which allows one-step DTG digital printing – including 3D effects and textures – on almost any fabric.
The digital printing industry moves at a rapid pace. Just five years ago, Kornit launched the Avalanche Poly Pro: the first digital direct-to-garment (DTG) print system developed specifically for polyester. However, almost two years ago, the firm took print-on-polyester capabilities a significant step forward with the Atlas Max Poly, a fully integrated machine that – thanks to its ability to limit dye migration – allows single-step printing even on dark polyester.
“We realised that there was a massive opportunity in that space,” Itamar Bartana, Kornit’s Director, Head of Business Segment, explains.
“Polyester is the second most common fabric in most categories today, behind only cotton, and it’s obviously very closely affiliated with sportswear. So with the Atlas Max Poly we have produced a system that uses our proprietary one-step printing process to allow people, for the first time, to print in a digital way on dark polyester on an industrial scale.
“But it’s not limited to that specific fabric. The Atlas Max Poly is our most versatile DTG system on account of the robustness of the chemistry that we use in our system. It can print effectively on many different types of fabric – polyester, cotton, blends, nylon, and many additional fabrics, both synthetics and naturals. We like to call it our Swiss Army knife – that’s a good analogy.”
Dye release
The challenge when it comes to printing on polyester is that dye can be released from the fabric when it is exposed to extreme heat as part of the final step of the fabric’s decoration process. Whether it’s the heat needed to cure screen printing, or the pressing required with heat transfer-based technologies, anything other than white polyester poses a risk.
“At Kornit, we developed a proprietary process, which is a dual-action protection mechanism against dye release,” Itamar says.
“First, the ink we use is cured at a very low temperature compared to other ink families and decoration processes: we cure our prints at 110°C, which is below the activation point of dye migration for most fabrics. Secondly, we developed something similar to a blocker layer, but it can be applied via normal printheads. So we have a blocker that we apply below the white underbase, and that acts as an additional layer of protection between the garment and the ink of the design.”
The creation of this technology is thanks to Kornit’s ability to develop and produce its own consumables. In this case, the Atlas Max Poly uses Kornit’s innovative water-based Neopigment Olympia ink. And it’s not only in conventional image printing where it is of benefit: 3D effects and textures – such as simulated heat transfer vinyl, high-density production and threadless embroidery – are also possible.
“When it comes to marketing these capabilities, we often need to differentiate between 3D applications that address fashion and 3D that addresses more functional applications,” Itamar says.
The Kornit Atlas Max Poly can make short runs profitable with high-throughput and automated single-step processes
“When we explain our 3D technology as a fashion type of application, we see a lot of excitement because it is viewed as a way for printers to differentiate themselves from their competitors.
“However, if we were to talk about digital 3D printing as a way to replace vinyl transfer, people understand the value very quickly once they see the end result is very similar to what they are accustomed to, but the process they need to implement to achieve it is much shorter and more efficient. In those spaces, we have a lot of interest because we can easily explain the value it has in making their lives easier by replacing many types of separate decoration processes.”
Perfect sense
That leads onto the economics of printing, particularly in a field like digital DTG that is ripe for personalisation and short-run printing. As well as reducing the cost and complexity of using multiple machines to achieve a range of different results, there are other benefits, such as production speed – irrespective of order size – and staffing.
“As with the output of any system, its speed depends on what you print. But most interesting about this system, especially with the market we have in mind – the sportswear market and adjacent markets – is the fact there isn’t any digital alternative. Most people would use heat transfer-based technologies, which are often slow. In that case, the comparison in terms of speed is very favourable,” Itamar says.
“Because with this technology, economies of scale don’t play a role, it also means that financially it is very favourable when you look at the customised garment market. We identified several spaces in the market where it is common that the average order size is one unit, or 10 units, or 15 units. But it doesn’t end there as using the Max Poly also brings value in longer runs at scale.
“With only one person required to operate the Max Poly, our customers also have the benefit of very favourable ratio of labour costs to output. You end up with something that I like to call a mini-factory: a system that, if it were put to constant use, would deliver more than 100,000 printed garments a year.”
Built for the future
With the demand for customisation, personalisation and on-demand printing only likely to grow, Kornit has ensured the Atlas Max Poly is as future-proofed as possible to meet emerging trends and challenges.
“We release our systems with factory set-ups to address use cases that we believe are popular and required by our target audiences now,” Itamar says.
“However, we understand people are looking for additional capabilities, or they want to offset between different elements. For example, if you are willing to compromise on through-put, then you gain the benefit of higher quality. So we are constantly engaged with the notion of introducing new set-ups and new applications to address the needs of our customer base. We work very closely with existing users to better understand how they look at the value that the system brings, and how we can develop new features.
“But I think the key element people are looking for, regardless of which sector they work in or the type of business they have, is versatility and robustness of the technology. Digital printing has made very significant progress in the last 10 or 15 years, but people are still looking to be sure that the results will be consistent across different fabrics, garments, and so on. It that regard, the Atlas Max Poly is an important step forward.”
Become a FESPA member to continue reading
To read more and access exclusive content on the Club FESPA portal, please contact your Local Association. If you are not a current member, please enquire here. If there is no FESPA Association in your country, you can join FESPA Direct. Once you become a FESPA member, you can gain access to the Club FESPA Portal.
Recent news
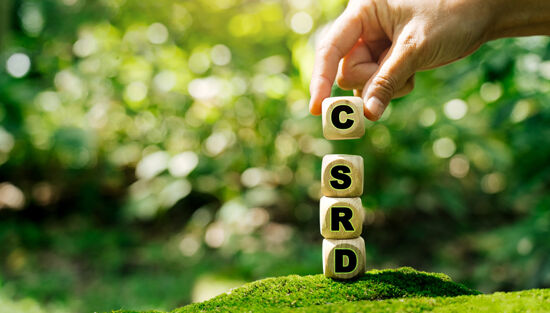
Regulation guidance: Corporate Sustainability Reporting Directive
The Corporate Sustainability Reporting Directive (CSRD) is now in effect, but with further changes on the horizon, what does it mean for printers? Sustainability consultant Rachel England outlines everything you need to know and talks to Apigraf about how your business may be affected.
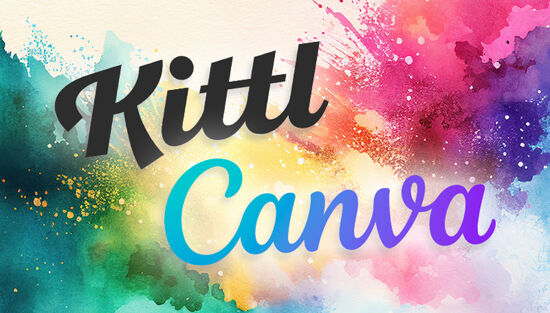
Web-to-print design: Canva versus Kittl
We look at popular design packages Canva and Kittl to determine how they compare regarding graphic design and print on demand.
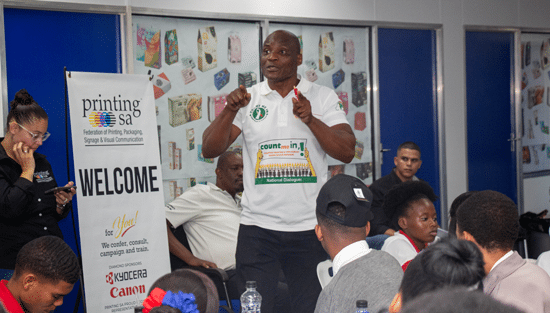
FESPA in South Africa: the print skills to thrive
Printing SA’s Career Day inspired young Cape Town learners to explore printing and packaging careers.
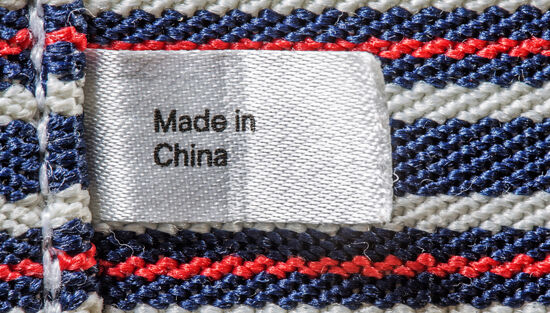
The rise of Chinese printers
Chinese printing companies are on the rise, and have their eyes set on the UK and EU marketplace. Some have made an instant impact; others are running into issues with maintenance and language barriers. What does the future hold for Chinese printing firms, and how can you navigate working with them?