Reshoring to the rescue? Sustainable resilience in supply chains
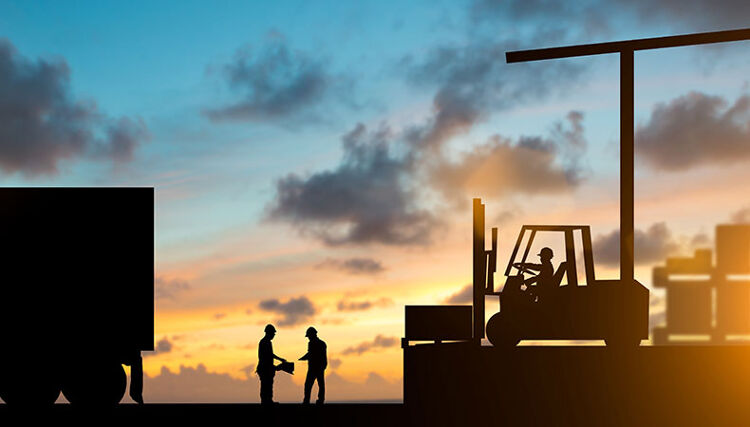
Supply chains across the board have been hit hard in recent times. With sustainability also high on the agenda, is it time for companies to bring operations home?
If the events of the last two years have taught businesses anything, it’s that resilience is clearly a top priority. COVID-19 and increasing climate change have both contributed to weakening supply chains and threatening operations around the world. Companies are therefore increasingly thinking about building supply chains that shift focus from ‘just in time’ to ‘just in case’, and many are looking to reshoring to reduce these risks.
The latest report from the Reshoring Initiative foresees the US adding more than 224,200 jobs from abroad in 2021 – 38% more than the 161,000 added in 2020. Meanwhile, a Thomas survey of 878 US manufacturing and industrial sector professionals shows that 64% are preparing for imminent reshoring.
Reshoring has been on the cards for many businesses even before the global pandemic. Research carried out in 2019 from Lloyds Bank indicates that more than a third (37%) of UK firms said they were planning on moving manufacturing processes back to the UK, giving as their reasons improved quality of production, reduced costs, and shorter supply chains as primary motivators.
Bringing it home
On paper, it’s an attractive prospect. Reshoring has the potential to reduce the need for expensive freight expenses, give greater flexibility when revising manufacturing processes, result in shorter waiting times for parts and components, reduce logistics issues and fulfil a growing demand for locally-made products.
Plus, as illustrated in recent times, reshoring boosts self-reliance and resilience when fragile global connections break down. For printers in particular, being closer to the point of consumption means they can quickly scale production based on real-time demand, thereby saving on unnecessary warehouse space.
Sustainability is another key driver. As businesses across all sectors feel the pressure to make their businesses more sustainable, bringing them closer to home can reduce carbon emissions and contribute to the closed-loop systems needed to alleviate materials shortages and other environmental impacts. This was demonstrated by the latest Smithers report, The Future of Green Printing to 2026, written by Ghent Workgroup chairman David Zwang.
Environmentally-friendly printing, he makes clear, is a key industry trend for the 2020s, and reshoring is a practical application of the circular economy.
The Ellen MacArthur Foundation (EMF) – vocal proponents of the circular economy – finds that one key barrier to circularity is the geographical dispersion of manufacturing sites and suppliers, “compounded by the complex, multi-layered bills of materials of today’s products, reflecting increased materials complexity and proliferation”.
Why reshoring is not a silver bullet
However, while circularity is easier to control closer to home, and shorter and more regionalised value chains will be a key part of the green transition, reshoring cannot be viewed as a silver bullet for resilience and sustainability challenges.
For a start, bringing work back behind your borders can’t guarantee protection from future disruption. Then there are other questions:
- Does the infrastructure exist to make the move worthwhile?
- Do the competencies exist at home for the products being made?
- Can the right materials be obtained at a feasible price point, and in the face of increased demand?
And then on the sustainability side, does reshoring tangibly improve your carbon impact, or could it in fact make it worse? From a circularity perspective, for example, products can’t readily be shipped around the world to be repaired, refurbished, or disposed of. Are there local assets that can manage this?
Parallel supply chains
Back in April the UK’s International Trade Committee began an investigation into the relationship between the global pandemic and international trade and touched on the idea of parallel supply chains as an alternative to total reshoring.
In the parallel supply chain model, companies source both locally and globally. For example, perhaps 10% to 20% of business runs through the parallel supply chain during normal circumstances with the majority going through the mainstream supply chain. When circumstances call for it (in the middle of a pandemic, for example), the supply allocation to either supply chain can be turned up as the situation requires.
In theory, the parallel supply chain would help to minimise future disruptions and potentially mitigate some carbon impacts without requiring a complete reshoring.
But it’s not feasible for everyone. Duplicating suppliers, distributors and manufacturers requires duplicate management staff, and while there are some economics of scale, running a parallel supply chain is a big investment. Plus, the supply chains of many printers are built on intellectual property, unique materials, processes, and components that provides a competitive advantage. The cost of replicating, tooling and diversifying access to this can be expensive.
Digital and automated ways forward
At a recent FESPA Innovations and Trends event, Standfast & Barracks Managing Director Stephen Thomas noted that while there’s a lot of interest in reshoring in the fashion industry, those in the industry are concerned with the price per metre of materials and are “still not looking at the lifecycle cost of a product”. In other words, printers need to take a holistic view of their supply chain, and for that reason talk of reshoring, and even parallel supply chains, may be premature.
Instead, businesses should look to build supply chain resilience and sustainability through digitisation. As Guy Alroy, co-founder of apparel workflow solutions company Early Vision, writes in a blog post for TexIntel: “The cost of labour, both in Europe and the US, is high, and reshoring the same processes won’t cut it. The key for cost reduction is the usage of emerging technologies and automation, coupled with reduction in material waste and adoption of an on-demand model, that keeps inventory levels adjusted to market demand.”
Technology has the potential to leverage the benefits of reshoring, without the commitment of relocating. Some industries are deploying digital innovations to replace factory man hours, while automated workflows bring major cost savings and production efficiency gains, especially to wide format printers.
Closed loops
Technology can also be harnessed to improve multi-way collaboration. For instance, the rise of cloud computing has opened new avenues for collaborative work, allowing print businesses and clients to work together from many parts of the world at the same time, without requiring the physical movement of staff or goods. Advanced digital inventory management, can ensure stock doesn’t devalue, meaning companies don’t need to be located near their main point of consumption to ensure adequate rotation. And, as the EMF notes, closed loops can be formed around a company’s regional areas – not just around the entirety of its global operations, which is much more difficult.
Ultimately, the sustainable solution lies not necessarily in reshoring – choosing what’s best for your business given the assets and requirements at hand. The pandemic has highlighted the critical, fragile nature of supply chains, but a reflexive decision to ‘bring operations home’ would still expose businesses to heavy dependence on a simplified but more vulnerable supply chain.
Instead, effort towards diversification through sustainably-informed digitisation will help printers and the sector as a whole become more resilient, agile and responsive.
Become a FESPA member to continue reading
To read more and access exclusive content on the Club FESPA portal, please contact your Local Association. If you are not a current member, please enquire here. If there is no FESPA Association in your country, you can join FESPA Direct. Once you become a FESPA member, you can gain access to the Club FESPA Portal.
Topics
Recent news
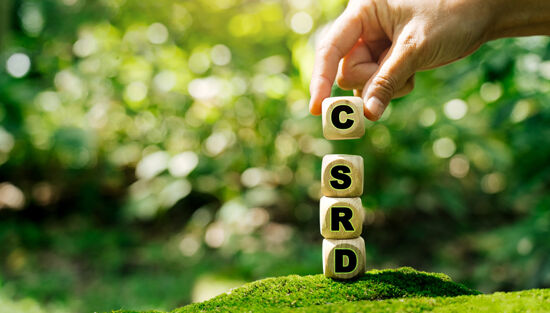
Regulation guidance: Corporate Sustainability Reporting Directive
The Corporate Sustainability Reporting Directive (CSRD) is now in effect, but with further changes on the horizon, what does it mean for printers? Sustainability consultant Rachel England outlines everything you need to know and talks to Apigraf about how your business may be affected.
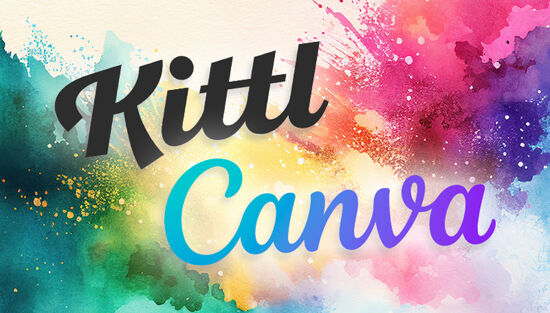
Web-to-print design: Canva versus Kittl
We look at popular design packages Canva and Kittl to determine how they compare regarding graphic design and print on demand.
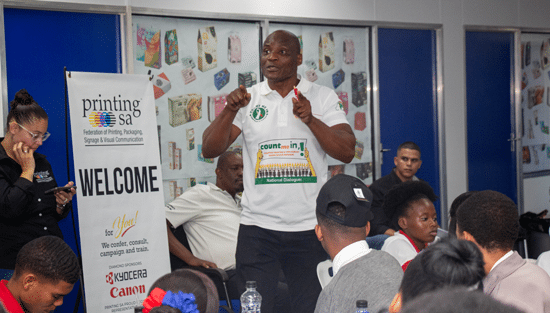
FESPA in South Africa: the print skills to thrive
Printing SA’s Career Day inspired young Cape Town learners to explore printing and packaging careers.
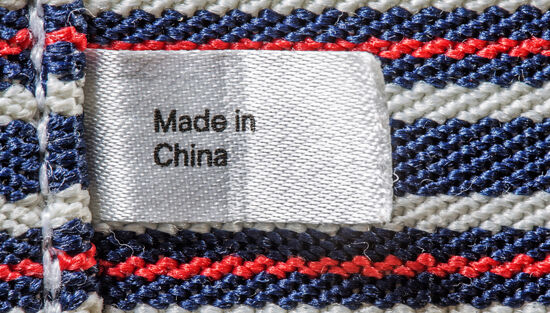
The rise of Chinese printers
Chinese printing companies are on the rise, and have their eyes set on the UK and EU marketplace. Some have made an instant impact; others are running into issues with maintenance and language barriers. What does the future hold for Chinese printing firms, and how can you navigate working with them?