Smart finishing with automated cutting system

Elitron has unveiled its new next-generation Kombo TAV system, which leverages AI to anticipate more demanding customer needs.
Visitors to the FESPA Global Print Expo in Amsterdam in March 2024 were able to experience a preview of Elitron’s new Kombo TAV system, intended to adapt to all possible cutting requirements, from sample-making to larger production runs with integrated or stand-alone automation to guarantee a high-performance production workflow. Club FESPA Online spoke to CEO Giuseppe Gallucci at Elitron.
How will Kombo integrate with AI in the future, and how will this increase productivity?
Elitron currently uses artificial intelligence (AI) in its Stressless Working Technology System; this automatically uses an algorithm to project digital dies on materials on the working area to obtain the best possible yield and keep material waste to a bare minimum.
This system creates immediate samples and is ideal when working with cardboard, corrugated and self-coloured or patterned media. We also implement AI when cutting banners, which automatically allows for any print distortion to create a banner cut to perfection every time.
Looking towards the future, we are developing an AI system that will be able to automatically identify all printed reference points immediately without having to centre these individually.
What does the new cutting system mean for savings in workforce – how completely automated is it?
Stressless Working Technology is completely automatic; however, it can be overridden by an operator should any last-minute changes be necessary.
Using Elitron’s AI for continuous, non-stop banner production is completely automatic, so there are considerable savings in manpower and zero errors.
What are the increases in speed and efficiency?
Reduced set-up times and increased precision, with savings in both manpower and material.
How much more sustainable is it?
The sustainability of AI can be measured in the notable reduction of material waste that would occur when manually placing the digital dies on the material. Regarding the banner material, the system would have to be constantly manned to check for any print deformation before cutting.
How does the Spark cutting system differ from previous cutting systems?
Spark is a compact range of cutting systems, which come in different lengths, from 80cm up to 2.5 metres, with the gantry over a width of 1.6 metres.
Loading and unloading options increase automation for this range of fixed and conveyor, compact, multi-tool cutting systems. In addition, it’s also possible to implement both Stressless Working Technology and Elitron’s proprietary vision technology, Seeker System.
Elitron Kombo TAV system. © Elitron
There is much discussion currently about the ‘smart factory’ with just in time manufacturing: how does Elitron tech fit in with this?
Elitron’s Kombo TAV, fully automatic cutting system with integrated loading, cutting and creasing, and unloading has been engineered to be fully integrated into a smart factory setting. This system incorporates a patented, fully integrated pallet management system, for non-stop, unmanned, high productivity, with unlimited pallet height.
This roll-in, roll-out pallet management system can extend out to connect with other machinery in the factory, for seamless productivity from printer to finishing and beyond.
This system comes with Seeker System vision technology, which automatically identifies the references points and printed images from both the top and underside. In a lights-out production workflow, customers can opt for Elitron’s Reversa Sheet Turning System, which can also be incorporated in the smart factory workflow.
What has been the feedback at FESPA Global Print Expo?
As Elitron were the first to introduce a fully automated cutting system, with two cutting heads, back in 2012, there is always a lot of interest to find out about our new product launches.
We recently unveiled the NEXT GENERATION Kombo TAV cutting system, which marks a new era in automatic, digital cutting: up to 35% faster, up to 40% greater production efficiency and up to 30% energy consumption savings.
This is possible due to the implementation of Hyper Speed Cutting Technology, developed by Elitron, a new next-generation control board, redesigned electronics, and a new motion control system with a faster communication protocol to take the brainpower of this already state-of-the-art cutting system to a completely new level.
With hundreds of Kombo TAVs currently installed worldwide, we’re happy to share that we have numerous orders for this new system that will perhaps not create a smart factory for all customers, but it certainly does mean smart finishing for everyone!
Feedback at FESPA Global Print Expo was positive. At FESPA we launched the new Kombo SDC+ cutting system with optional new smart automatic loading and unloading systems. Feedback for this new, multi-function system has been great and many customers have welcomed the flexibility to add automation as they require.
Become a FESPA member to continue reading
To read more and access exclusive content on the Club FESPA portal, please contact your Local Association. If you are not a current member, please enquire here. If there is no FESPA Association in your country, you can join FESPA Direct. Once you become a FESPA member, you can gain access to the Club FESPA Portal.
Topics
Recent news
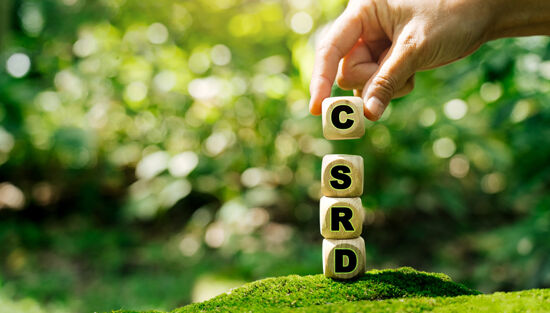
Regulation guidance: Corporate Sustainability Reporting Directive
The Corporate Sustainability Reporting Directive (CSRD) is now in effect, but with further changes on the horizon, what does it mean for printers? Sustainability consultant Rachel England outlines everything you need to know and talks to Apigraf about how your business may be affected.
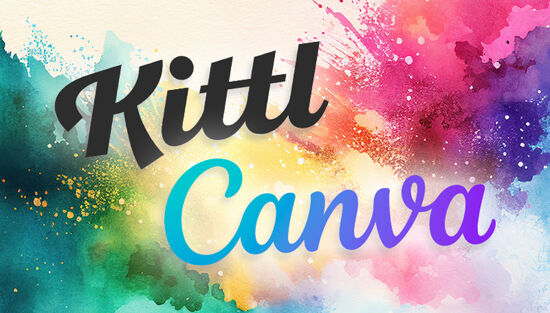
Web-to-print design: Canva versus Kittl
We look at popular design packages Canva and Kittl to determine how they compare regarding graphic design and print on demand.
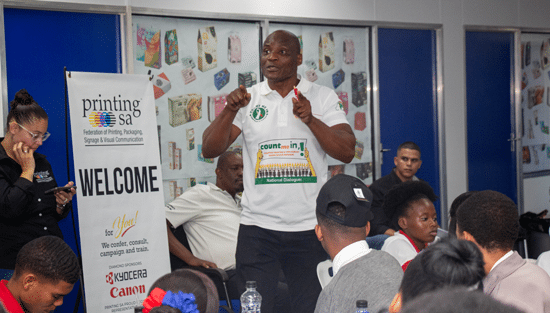
FESPA in South Africa: the print skills to thrive
Printing SA’s Career Day inspired young Cape Town learners to explore printing and packaging careers.
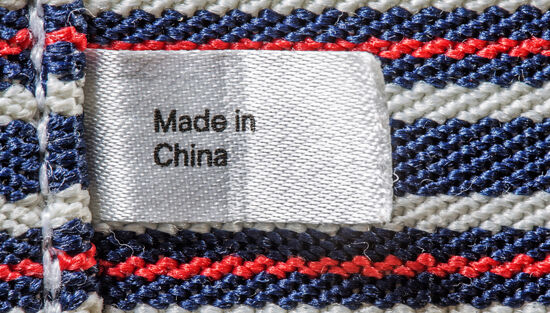
The rise of Chinese printers
Chinese printing companies are on the rise, and have their eyes set on the UK and EU marketplace. Some have made an instant impact; others are running into issues with maintenance and language barriers. What does the future hold for Chinese printing firms, and how can you navigate working with them?