Solve problems early with preflighting
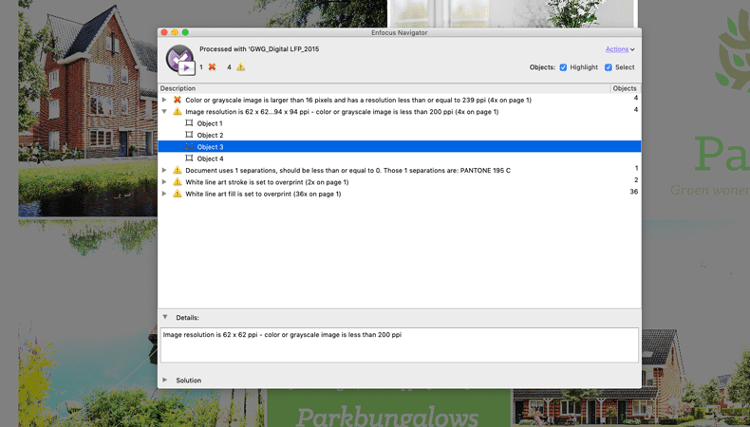
Post-COVID, making efficiencies is more important than ever. Andrew Bailes-Collins of Enfocus on how effective preflighting systems are essential.
What is the importance of preflighting in workflow processes to print service providers' efficiency?
Everybody is under pressure because of margins and turnaround times. You want to identify and remove any possibilities for error and inefficiency in the production process, reduce spoilage and retain as much margin as possible. You also want to find out about any errors and potential issues and either fix them, preferably automatically, or you want to identify them early enough in the process so that you minimise the impact they will have.
Finding out about issues early means you have options. You can have a discussion with your customer on how to resolve them, receive a new file where needed, capture any additional costs where possible and also renegotiate any schedules if applicable. If you find out about a problem once the file has entered production or while printing or finishing then you have an issue that has already cost you time and materials.
Preflight is the way to ensure that your raw materials for manufacturing (a PDF file) are fit for purpose before the manufacturing process starts
Also, if an issue is found at this stage, you are fighting an uphill battle to maintain the production schedule and meet customer expectations. Another way to look at it is that these days, automated print production is often referred to as a manufacturing process. Preflight is the way to ensure that your raw materials for manufacturing (a PDF file) are fit for purpose before the manufacturing process starts.

How is the wide format industry getting along with preflighting? In an interview at FESPA 2016, you said that it was just getting to grips with the problems commercial print had already tackled? Have new problems arisen since then? Or are the problems fundamentally the same?
I think the problems are fundamentally the same, but what’s changed is that preflight vendors have added more functionality specifically related to large format printing (LFP) since 2016, and I think that trend will continue for some time.
We are also seeing a real push to automation in the LFP market, and that changes the way we have to think about preflight software working as it needs to aid and be an enabler for automation, rather than relying on an operator to resolve issues and make decisions manually. There are production aspects of wide format that are unique, and therefore require specific functionality.
Isn’t the cost of automating workflows prohibitive?
To be honest, in some markets and regions, if your users are not already automating now, they are too late and are probably already at a disadvantage competitively. Automation need not be expensive to get started with, but starting an automation journey can be a little daunting.
I call it a journey because it’s not something you implement and finish – it will be an evolutionary process that develops and changes as your business and your work changes.
The ideal way to start the journey is to identify bottlenecks, excessive manual processes and pain points in your current method of working and look at how automation can help resolve them. Once you overcome those issues then you can move onto the next ones.
It’s possibly a misconception you have to make a large investment, flick a switch and completely change the way you work when you want to start automating
With this approach you get an immediate return on your investment, your employees start to see the benefit of the process and are not scared by it, you gain experience, and more importantly you tackle issues in small bite-sized pieces, rather than trying to implement a complete brand-new way of working overnight. I think it’s possibly a misconception you have to make a large investment, flick a switch and completely change the way you work when you want to start automating.
What is the Ghent Workgroup's role in all this?
The Ghent Workgroup (GWG) (www.gwg.org) was founded in 2002 and is an international organisation made up of graphic arts users, associations, and developers building best practices for graphic arts workflows. The member companies are all industry names that readers will be familiar with: FESPA is one of them.
The group came into being in the early days of PDF, when everybody was doing their own thing regarding how to supply a PDF file for production and how to check it. As a result creators found themselves needing to make different types of PDF files for different publications or printers, often in the same country. Not the most efficient way of working.
The GWG helped standardise PDF creation and also standardise PDF preflight, which made the whole process of creating and receiving PDF files much more efficient and transparent.
Since then, the group has diversified into other aspects of print production such as colour and job ticketing, and has produced new standards such as its PDF format, which has gained acceptance in new markets such as sign and display and packaging. Over the years, the group has also been heavily involved in promoting other ISO printing standards as well such as PDF/X. I think you’d be hard-pushed to find a better group of printing industry experts who sit together in a room three times a year and try to move the industry forward.
Most importantly, everything we do – educational white papers, application configuration files or output test suites – is free and available to download from our website.
Can you tell me a little about the Ghent Workgroup beta profiles. How did they come about and what are they aimed at achieving?
The GWG responds to trends and needs in the market and if we see a situation where a standardised preflight profile could be needed, we try and fill that gap.
The sign and display profiles came out of recognition that PDF was now heavily used in this market, and that a standard preflight profile would be useful.
The profiles are now no longer in beta and now are publicly available – we would welcome any feedback your readers have on these preflight profiles, as once a profile is released we are typically already thinking about the next version and where improvements can be made.
These profiles contain specific handling for viewing distance on several of the preflight checks, so the target preflight values adjust based on the specified viewing distance
The preflight profiles were developed with input from the GWG members and are focused on the specific requirements of digital sign and display, which are very different to those in some of our other preflight specifications. One unique aspect of these profiles compared with those used for other production techniques is that they contain specific handling for viewing distance on several of the preflight checks, so the target preflight values adjust based on the specified viewing distance.
How were Universal Proofs of Preflight developed and how can they help our readers?
Universal Proof of Preflight is quite an old concept, and I think it’s fair to say it never really gained much traction globally, although it is successfully used by individual companies and some regions.
The idea is that embedded within a preflighted PDF file is an preflight audit trail. This is information about a preflight check that has been carried out for the PDF, and contains information about the preflight profile used as well as what the outcome of the preflight check was. In addition, the user can verify that the file has not been altered since the preflight was executed through the use of a digital signature.
The idea behind it was that if you received a PDF that had this audit trail, you did not need to preflight the file again, as you knew it had already been checked, and had not changed since that check had been carried out. It was particularly interesting for publication workflows as it made the process more efficient. It’s also cross-vendor, so a PDF with an audit trail from one preflight vendor could be handled by a preflight solution from another vendor. It’s a very useful technology and is still supported today, it’s used by some companies to verify files in their internal workflows so it’s definitely worth investigating for use in an LFP environment.
Become a FESPA member to continue reading
To read more and access exclusive content on the Club FESPA portal, please contact your Local Association. If you are not a current member, please enquire here. If there is no FESPA Association in your country, you can join FESPA Direct. Once you become a FESPA member, you can gain access to the Club FESPA Portal.
Topics
Recent news
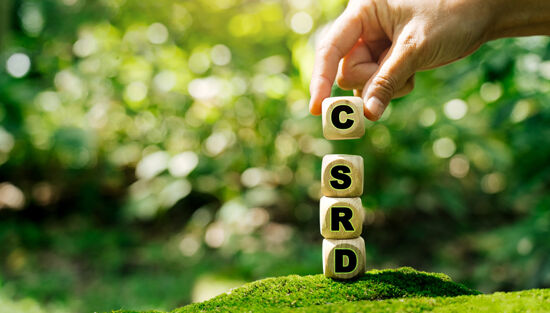
Regulation guidance: Corporate Sustainability Reporting Directive
The Corporate Sustainability Reporting Directive (CSRD) is now in effect, but with further changes on the horizon, what does it mean for printers? Sustainability consultant Rachel England outlines everything you need to know and talks to Apigraf about how your business may be affected.
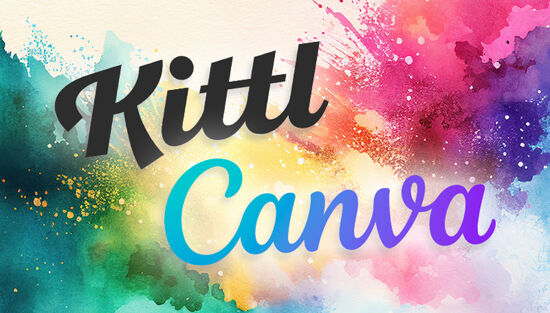
Web-to-print design: Canva versus Kittl
We look at popular design packages Canva and Kittl to determine how they compare regarding graphic design and print on demand.
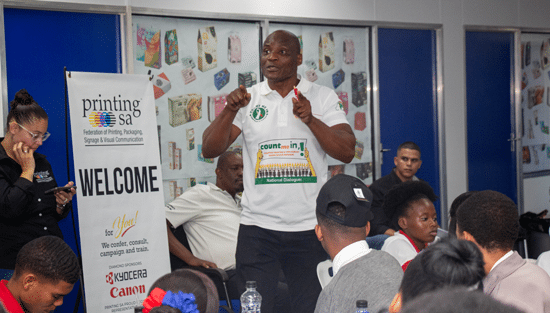
FESPA in South Africa: the print skills to thrive
Printing SA’s Career Day inspired young Cape Town learners to explore printing and packaging careers.
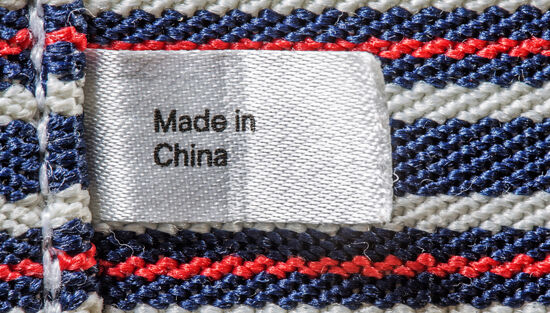
The rise of Chinese printers
Chinese printing companies are on the rise, and have their eyes set on the UK and EU marketplace. Some have made an instant impact; others are running into issues with maintenance and language barriers. What does the future hold for Chinese printing firms, and how can you navigate working with them?