The future of industrial inks – from film insert moulding to haptics
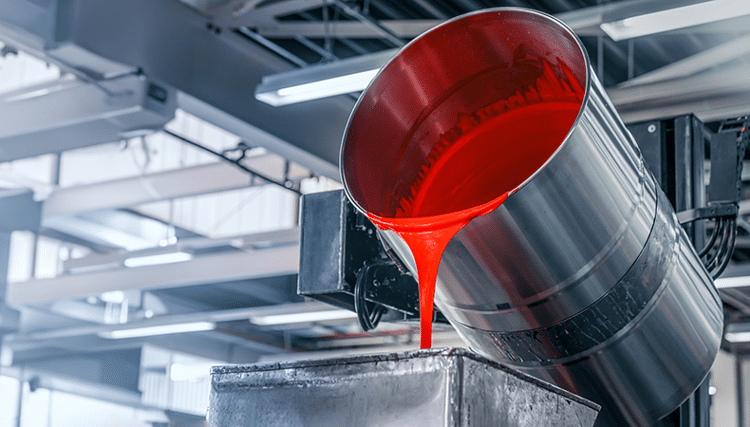
Marabu is a world-leading manufacturer of screen, digital and pad printing inks and creative colors, offering a wide variety of solutions for industrial and graphic printing applications. We spoke to the team at Marabu, near Stuttgart, Germany, as the firm celebrated its 165th birthday.
Could you give an example of the chemical differences in your range of inks and the regulations Marabu needs to comply with?
Friedrich Goldner, Sales Director, Key Account Screen and Pad Printing Inks: Marabu is a member of the EuPIA (European Printing Ink Association) and is following its exclusion policy for all its printing inks. Product safety is a top priority for our customers and employees. Printing inks for specific industries, e.g. Ultra Glass UVGL for drinking glasses and glass bottles need to fulfill specific requirements like dish washer resistance (household dishwasher: minimum 500 cycles; industrial dishwasher: minimum 700 cycles) and curing with the latest high-speed UV machines.
Pad inks for toys, like Tampa® Speed TPL, need to perform in highly automated pad printing production lines and need to cope with customer-specific exclusions lists plus additional toy safety standards like AfPS GS 2019:01 PAH: GS specification.
Marabu is committed to strict compliance with all EU REACH legislation and standards and is constantly seeking more sustainable and safer raw material alternatives. ©Marabu
How do you assist clients with their colour management?
Kathrin Zimmermann, Senior Manager Colour Management: Our free Marabu ColorManager software allows screen and pad printers worldwide to access colour formulae for all common PANTONE®, RAL® and HKS® colours or colour numbers and mix the corresponding colour themselves. You can also enter and save your own recipes. A dispenser or a selected scale can also be connected to the software. If a weighing error occurs, the software automatically compensates and adjusts the recipe accordingly. We are currently working on an update to the ColorManager, which will be released this month. In addition to the latest technical standards, the enhanced version will be a pure cloud version. Customers will be able to register once, access recipes, create and save their own recipes and then not have to worry about anything. Regular updates will be generated fully automatically.
What are the benefits, technical difficultites and versatility of film insert moulding (FIM)?
Claudia Bauer, Technical Project Manager FIM/ALU/OCP Screen and Pad Printing Inks: FIM is a special injection moulding process used to produce high-quality moulded parts in large quantities. The design is applied to a film that is ‘injected’ with a plastic melt. The largest market is the automotive industry with both small and large interior components. For small components such as buttons and sliders, function is important. For large components such as interior door panels or center panels, design variety also plays a major role. This process combines technologies such as high-pressure forming and injection moulding, all production steps must be coordinated with each other, and the screen printing ink system used must also be specially selected for this process.
To be able to test printing inks for FIM applications in a realistic way, Marabu has the same equipment in house as most of its customers. © Marabu
Friedrich Goldner: FIM can be compared to a triathlon: Printing – Forming – Moulding, and every single step must be mastered to achieve an excellent result. To test FIM applications in a realistic way, we have the same equipment as most of our customers with a Thieme screen printing machine, Natgraph dryer, Niebling forming and Engel molding equipment. Our latest FIM series Mara® Mold MPX was thoroughly tested in-house in several aspects such as peeling strength, environmental cycle test or hydrolysis ageing. Through this, we have gained a great deal of trust from our customers and won numerous projects. FIM originated in the automotive sector but found applications as well in medical and white goods. With new sectors, new challenges are coming up, such as new film and moulding resin combinations and moving from previously interior-only into new exterior applications.
How does the LED-curing etch-imitation LEDGL 913, in which there is no need for etching chemicals to print a matt design, work?
Alexander Suckfüll, Head of Technical Services & Projects Screen and Pad Printing Inks: LEDGL 913 can be used like a regular screen printing ink. The etching effect is visually and haptically close to real glass etching with the advantage of being an LED curable ink to save energy.
Real etching uses harmful chemicals and a lot of energy, whereas the screen printing process combined with LED systems is faster and more precise. As the etched areas can be defined using CtF [computer to film] or CtS [computer to screen] technology, the design can be as creative as possible. The opposite of LEDGL 913 is UVGL-WV. Our window varnish is specifically designed to be printed on etched or sprayed bottles to restore transparency where required.
With the new Marabu LED-curing etch imitation Ultra Glass LEDGL 913, you can print matt surfaces without the need for etching chemicals. © Marabu
What sets your inks apart from those of your competitors?
Alexander Suckfüll: Continuous innovation and reduction of harmful substances as well as energy consumption at the same or better quality level make Marabu inks unique.
What trends are you seeing in the screen printing and digital printing industries that are influencing ink development?
Matthias Schieber, Digital Transformation Manager Digital Inks: Ink development has been influenced by the capabilities of the application technology and the requirements of the application itself in terms of performance and product safety. With faster machines, the trend towards LED and tighter specifications, we’re following the demands of the market. In terms of the key trends in printing, ink seems to be the key component: it is elementary if new applications are to be realised in print. This is a fact that increases the importance of providing reliable, predictable development work.
As an innovation leader, Marabu is at the forefront of using AI to deliver the best possible service to the customers. © Marabu
How is Marabu preparing for the future of printing technology?
Matthias Schieber: With over 165 years of successful experience, Marabu has learnt to adapt and integrate technology trends to follow the needs of the industry. This touches every angle of the company in order to remain competitive. Marabu is already practising the use of leading-edge analytical tools, AI-supported ink development and has worked out more efficient and sustainable production methods. The future will challenge our products and our services around the products. We are already moving forward and have our minds set on the future.
What initiatives or technologies you are using to reduce the environmental footprint of your ink manufacturing process?
Alexander Suckfüll: Environmental protection has always played an important role for us. As a company in the chemical industry, we feel a particular obligation to actively protect the environment and to promote sustainable production methods. In line with our company-wide sustainability strategy, we avoid and reduce emissions wherever possible: through green electricity, energy-saving programmes, the use of climate-friendly materials and resource-efficient production methods. As part of the Climate Alliance Baden-Württemberg, we have pledged to reduce our CO2 emissions by a further 20% in the coming years. To this end, we are converting our production facilities and investing in new machines and technologies.
Become a FESPA member to continue reading
To read more and access exclusive content on the Club FESPA portal, please contact your Local Association. If you are not a current member, please enquire here. If there is no FESPA Association in your country, you can join FESPA Direct. Once you become a FESPA member, you can gain access to the Club FESPA Portal.
Recent news
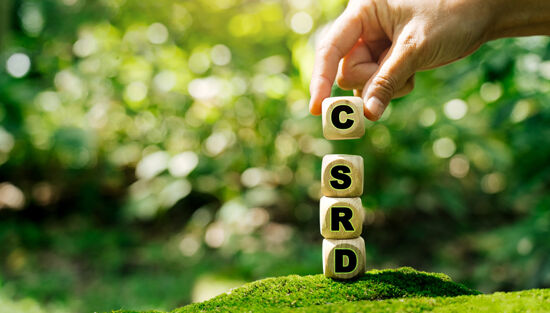
Regulation guidance: Corporate Sustainability Reporting Directive
The Corporate Sustainability Reporting Directive (CSRD) is now in effect, but with further changes on the horizon, what does it mean for printers? Sustainability consultant Rachel England outlines everything you need to know and talks to Apigraf about how your business may be affected.
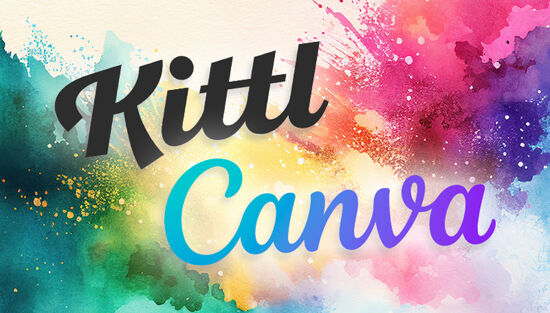
Web-to-print design: Canva versus Kittl
We look at popular design packages Canva and Kittl to determine how they compare regarding graphic design and print on demand.
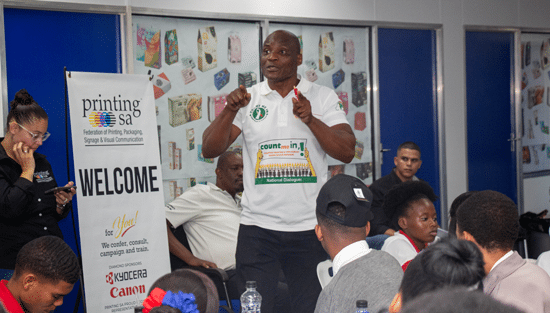
FESPA in South Africa: the print skills to thrive
Printing SA’s Career Day inspired young Cape Town learners to explore printing and packaging careers.
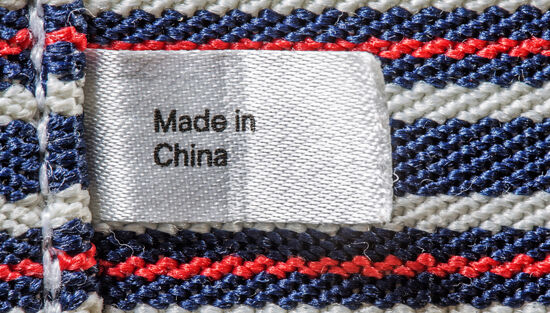
The rise of Chinese printers
Chinese printing companies are on the rise, and have their eyes set on the UK and EU marketplace. Some have made an instant impact; others are running into issues with maintenance and language barriers. What does the future hold for Chinese printing firms, and how can you navigate working with them?