From silkscreen to inkjet, technology to art with Jon Cone

We speak to Jon Cone, one of the great fine art and photography print innovators, about the story behind his revolutionary Piezography monochromatic inkjet system.
Printing is an industry that requires a multifaceted range of talents. The genesis for many printers’ careers is an appreciation of visual aesthetics. But to make that reproducible, an understanding of the technology is also required. And then, to make it a viable business, you need a level of financial acumen.
Few people have explored all three facets as thoroughly as Jon Cone. Starting out as master printer’s apprentice in early-1980s New York, Jon has worked with some of the world’s most demanding artists and photographers; he has successfully run his Cone Editions studio for more than 40 years; and he has developed industry-leading monochromatic inkjet technology.
But the foundation for Jon’s success was partly inspired by something quite different: the famous Apple advert during the 1984 Superbowl.
“I thought, I want that – although we couldn’t afford it!” Jon laughs.
With the support of his wife, Cathy, who has worked alongside Jon ever since his earliest print days, Jon did manage to buy that early Mac. “That started my interest in using a computer as a tool and, by doing so, it also introduced me to a younger generation of painters and sculptors,” Jon says.
Jon silk screen printing in around 1983 © Jon Cone
“I encouraged artists of my generation who were conceptual in their thinking and who were really excited by the possibilities of computing. I began to make art using a computer and that art made its way into relief prints, silkscreen prints, photogravures – the traditional mediums.”
The mother of invention
Things changed further in the 1990s.
“An artist I knew in California saw an inkjet print that he thought was really quite good. He called me up and said I had to find out more about an Iris printer,” Jon says.
“I had to go to the library at Dartmouth College and use microfiche to read newspapers to find out about Iris Graphics. A salesman visited us. He said: ‘You do know that these cost $123,000?’ We had no idea, but to save face, we said, ‘Oh yeah.’
“I financed the printer for $6,000 a month and took delivery of an Iris printer in 1990. I couldn’t afford it but its potential was extraordinary.”
With an initial diet of commercial work, Jon and Cathy managed the payments before they turned solely to fine art. But when some of the software and hardware they had been loaned for it needed to be returned, Jon decided to develop his own interface between the Iris and his Apple Mac.
Early digital printers in 1991 © Jon Cone
“Such an interface didn’t exist at the time, but Iris became very keen that I might be helpful to them to develop this technology for the fine art and photo market, so I became a developer for Iris. In fact, I even brought the Iris over to the Royal College of Art in London in 1994 or 1995. They flew the printer in and I made prints with the students.”
At the same time, Jon was doing his own studying – in his case, of the Iris’s operating literature. He came to the conclusion that the only way to develop the potential of the system was to make his own inks and software.
“I thought I could develop things that were important for photographers and important for my studio. That became a mission,” Jon says.
Experimentation
The first thing Jon focused on was colour. The inks that Iris used at the time only lasted one or two years in daylight before starting to fade.
“I looked at another problem that was prevalent back then: plastics. Plastics were colourised but they would oxidise quite quickly in the sun,” Jon says.
“However, there was a compound called HALS [hindered amine light stabiliser] that stabilised dye molecules. I knew you could use an ultraviolet light absorber to absorb the ultraviolet light that causes dye molecules to vibrate and break apart, which is what causes fading. But I found that if you used a water-miscible HALS as well as UV absorbers, the dye molecules became much more stable that either one used on its own. I got a colour ink set to last at least as long as a photographic c-print, which with Wilhelm testing was around 23 years. That was really significant in those days.”
Putting this technology to the test, Jon was even selected by legendary American photographer Richard Avedon to produce his ‘In Memory of the Late Mr and Mrs Comfort’ portfolio for the New Yorker magazine.
In Memory of the Late Mrs Comfort © Richard Avedon, courtesy of Jon Cone
However, Jon’s development in colour dye stabilising was not his greatest innovation. By replacing the coloured dyes with different shades of black, he realised a breakthrough in monochromatic printing was also possible.
“For photography, I started thinking about creating four dilutions of black ink – light grey, medium grey, dark grey and black,” Jon says.
“Normally, inkjet printing prints black perfectly. But when you want to print very light grey, it takes the black dots and spreads them far apart. Your brain mixes them with the paper white and you see light grey. But I had light grey ink, so I could print a lot more dots together, and I also a medium grey and a very dark grey and a black. That meant I was able to make very continuous tone, black and white photographs where you couldn’t see the inkjet dots.”
The value of Piezography
Coining the technology, ‘Quad Black Printing’, Jon used his knowledge of the Iris system to write software sophisticated enough to control all four inks on an Iris machine. But while Iris technology was still prohibitively expensive, the introduction of Epson into the inkjet world opened up the possibility to reach a wider market. Evolving Quad Black into what is still his business’s flagship product – ‘Piezography’ – Jon tapped into the Epson customer base and became a developer for a second time.
“Epson moved into six-ink printers, so I moved into six shades of black. Then they moved into seven, eight and now we have 10 shades. Piezography is always producing tens of thousands of more grey level separations than Epson normally can, because they only have three blacks. Our prints are smoother, they have higher acuity – what we perceive as detail – and they have higher shadow detail. And it’s affordable,” Jon says.
“With a regular inkjet printer, you have a dithering of dots – similar to what a half-tone is to a newspaper. That’s where humans see detail. We can’t see detail in the solid black but as the image gets lighter and lighter, our eyes perceive detail, but they also pick up on those dithering dots.
Dawn, Shepaug River at Steep Rock: the split-tone evident in this print moves from silvery cool highlights to chocolate brown shadows © Carl Weese courtesy of Jon Cone
“With an Epson printer having so few shades of black ink to use, it has to make the dots smaller and smaller to make the image lighter. With my system, I actually have lighter shades of black ink with which to print lighter shades of tone. Therefore, I am able to move those dots of ink much closer together – I print a lot more ink than an Epson printer normally does. That means the brain doesn’t see those dots, and we can print the space between dots in much more detail. My system actually increases the resolution of a printer by about three times.”
And perhaps the best thing is – underlining Jon’s mission to save photography – to enjoy the benefits of Piezography, it doesn’t even require an expensive camera.
“Most people use an iPhone today – that’s more than adequate,” Jon says. “Having said that, a number of customers that we print for have $60,000 Phase One cameras – and, when we see those files come in and the prints we make from them, it’s quite extraordinary.”
Header image: Gregory Colbert prints produced with Piezography using 110-inch Roland printer modified from six-ink to 12-ink. @ Jon Cone
Become a FESPA member to continue reading
To read more and access exclusive content on the Club FESPA portal, please contact your Local Association. If you are not a current member, please enquire here. If there is no FESPA Association in your country, you can join FESPA Direct. Once you become a FESPA member, you can gain access to the Club FESPA Portal.
Recent news
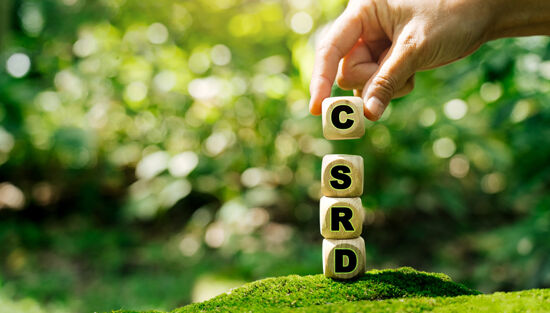
Regulation guidance: Corporate Sustainability Reporting Directive
The Corporate Sustainability Reporting Directive (CSRD) is now in effect, but with further changes on the horizon, what does it mean for printers? Sustainability consultant Rachel England outlines everything you need to know and talks to Apigraf about how your business may be affected.
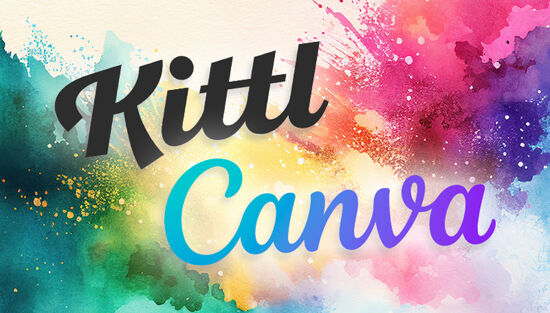
Web-to-print design: Canva versus Kittl
We look at popular design packages Canva and Kittl to determine how they compare regarding graphic design and print on demand.
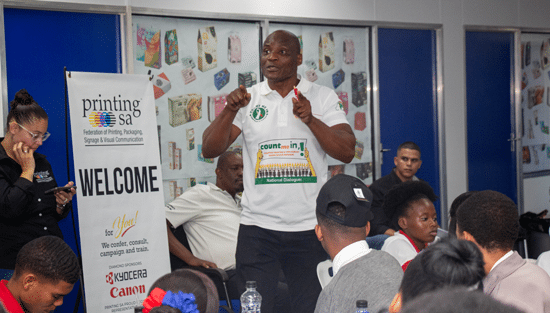
FESPA in South Africa: the print skills to thrive
Printing SA’s Career Day inspired young Cape Town learners to explore printing and packaging careers.
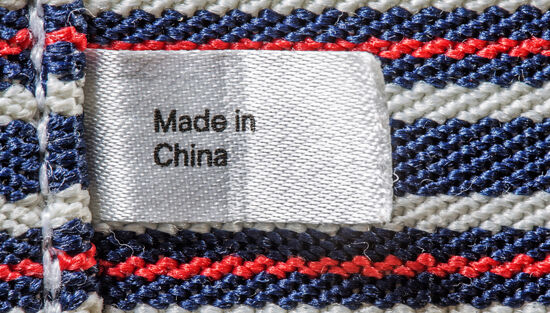
The rise of Chinese printers
Chinese printing companies are on the rise, and have their eyes set on the UK and EU marketplace. Some have made an instant impact; others are running into issues with maintenance and language barriers. What does the future hold for Chinese printing firms, and how can you navigate working with them?