Why LED curing is important for your print shop
As part of our Learning Curve series, Simon Eccles investigates the increasing use of LED light arrays for ultraviolet curing of photopolymer inks in large format inkjets.
LEDs are an attractive technology that generates intense light with minimal power consumption, while emitting very little heat and usually enjoying very long lifetimes. They are starting to replace power-hungry, hot and short-lived mercury vapour lamps (aka metal halide) on modern UV inkjets.
Low power consumption, cool running, great flexibility in use, long life and little problem with disposal means that LEDs are a very attractive technology in both practical printing terms and as a much more environmentally friendly alternative to mercury lamps.
Precisely what the savings are varies depending on the systems, and LED cost-performance and power outputs are changing all the time. However as a rough guide, Mimaki says that a typical UV-LED unit for a large format printer, that outputs 10W of UV energy, consumes about 60W of electricity for the lamps plus about 20W for the cooling fan and the output control circuitry. So, 80W in total, a bit less than the old generation of 100W tungsten filament domestic light bulb.
By comparison, the total power consumption of a traditional metal halide lamp is about 1.2KW, which is rather more than a single bar electric fire heater. These lamps run very hot – between 600 to 800 Deg C internally – and they generate radiant heat which transmits to the rest of the printer components, including the heads, ink and most critically, the media.
Like-for-like then, a metal halide lamp uses about 15 times as much electricity as a UV-LED curing system. However, because UV-LEDs can be switched on or off near-instantly, printers only need to switch them on during the actual printing cycle. Once a metal halide lamp has been turned off, it cannot be turned on again until it cools down.
Thus, it is generally left on constantly while the printer is in use. With a 50% operation cycle a UV-LED array consumes only 1/30th as much electricity as metal halide. This doesn't mean that the whole printer is 30 times more efficient with LED.
All printers have common elements such as motors, control electronics, ink supplies and vacuum pumps. So the actual difference in power consumption of the printer as a whole would be less. Even so, a printer with a metal halide lamp consumes three to ten times as much electricity as the one with UV-LED, says Mimaki.
Mimaki launched its roll-fed UJV5-160 at FESPA last year, with LED curing.
Using UV-LEDs doesn't make a lot of difference to the purchase price of a printer, so over time the LEDs just save more and more money, as a combination of less electricity usage, lower maintenance and virtually no replacement costs. Apart from the obvious reduction in electricity bills, this can be an important factor for companies that are trying to reduce their carbon footprint or get a certificate for carbon neutrality, and may have some relevance to carbon credits.
Cool components
LEDs (Light Emitting Diodes) are solid state electrical components that are widely used in modern lighting applications, with new uses appearing all the time. The UV emitting type (generally called UV-LED) are just more specialised and expensive. For ink curing purposes they are built into arrays of multiple LEDs.
They produce a relatively narrow range of wavelengths of UV, compared to the wider range of mercury vapour lamps. It's best to use inks that have formulated been for maximum sensitivity in those wavelengths. Printer manufacturers will be able to supply own-label inks for LED use on their own printers, but it's a factor to be aware of if you use third party inks.
Unlike mercury lamps, UV-LEDs don't emit infra red light or radiant heat. This means that the print media doesn't heat up significantly during printing, so heat-sensitive materials can be used.
Alternatively, you can use thinner plastics such as vinyls than you would with mercury lamps, as they won't buckle under the LEDs. Thinner media means savings on materials and lighter weight rolls, with benefits throughout the supply chain from delivery trucks to waste disposal. The driver electronics to LEDs do heat up, so large array lamp housings still need some water or fan cooling, but as we've seen, this needs a lot less power than mercury.
Lower lamp temperatures may also mean less ambient heating in the pressroom. Normally this is a good thing, though in some cold climates this may mean you have to turn the factory heating up a bit in the winter to compensate, so you lose some of the cost benefits.
On the other hand, in warm climates the operators will appreciate a cooler pressroom, and you won't need as much air conditioning power if you have that fitted. The lamp life of a MH lamp is normally considered to be about 1000 hours (up to the time of 30% light reduction). If the lamp operates for 8 hours per day, it will have to be replaced in 125 days (about 6 months with 20 operation days/month).
Longer life
The service life of a single chip with UV-LED is about 10,000–15,000 hours depending on the heat dissipation. If a UV-LED operates for 8 hours a day, with 10,000 hours service life, it lasts for 1,250 days (about 5 years assuming 250 working days per year).
Since the UV-LEDs are turned off in non-printing mode, the actual service life would be longer. Most UV-LEDs would never need replacement during the service life of the printer. Old high pressure mercury lamps generated ozone gas, which is hazardous to operators and needs to be extracted by ventilation.
However, this is largely overcome by using a glass that filters out the specific ozone-generating wavelength. LEDs don't generate ozone either. Mercury is poisonous so lamps need to be disposed of in line with environmental regulations. There are no significant hazardous materials LEDs, and because they last longer there is lower waste anyway.
Fast switching
Another big benefit is that LEDs can be switched on and off rapidly, or varied in intensity, without damage. Mercury lamps work by in effect striking a short-circuit arc through the mercury in the lamps. It takes specialist electronics to fire them up and once fired, you want to keep them running, so they are normally left on throughout the shift, using power and generating heat whether you are printing or not.
Printer speeds vary so the energy requirements of the UV curing vary too. There's only limited scope for varying mercury lamp output intensity by changing the power input, so they are in effect on full power all the time and mechanical shutters are used to control the amount of light reaching the media, or to shut it off completely.
By contrast, LEDs can be switched so rapidly that this can be used to vary the light output, though it's also possible to vary the brightness by changing the input power levels. As the LEDs are only switched on when needed and can be pulsed to reduce their power output, their lifetime can be extended to years, potentially more than the lifetime of the printer.
Higher light emissions are being developed all the time, pointed out Chad Taggart, vice president of marketing and development at Phoseon, a US based developed of LED curing lamp arrays. "The power of LEDs in terms of radiance and energy density or dose, is increasing dramatically," he said. "Every two to three years we're doubling the output capability. For instance we went from 4 Watts per cm2 in 2008 to 8 in 2010, to 16 in 2012. There's no reason it can't hit 24 or more in future.
"We believe that the perception of low power is from people not staying up to date with our technology. We have many customers in large format today that are using LEDs for the highest speeds available. Some printers are air-cooled, some are water-cooled. Typically our highest powered products are water cooled. If you keep them cool they'll last 20,000 or 30,000 hours."
Although the electronics, firmware and other issues mean that it's unlikely that end users could modify an existing UV mercury lamp printer to use LEDs, it's getting easier to manufacturers to build them in without major modifications.
For example Integration Technology Ltd (ITL) in the UK introduced MZero LED lamps at FESPA 2012. These are a straight component swap for its MZero mercury lamp units, which are already used on head carriages in wide format printers.
Printers that are designed from the start for UV-LEDs can be smaller, as there is less need to build in space for cooling and extraction fans.
Which printers use LED?
Inkjet manufacturers are increasingly fitting LEDs to new UV printers as they are launched.
Mimaki claims to have been the first to introduce LEDs for wide format, on the UJV-160 in 2008, having first started development in 2003.
At FESPA Digital in London last year the same company introduced a pair of fast LED cured printers, the flatbed JFX500-2131 and the roll-fed UJV500-160. Fujifilm's roll-fed Acuity 1600 LED and Roland's roll-fed VersaUV 640 LEJ and flatbed 640 LJF are also among the printers that use LEDs.
EFI VUTEk using UV-LEDs as it introduces new variations of its HS and GS printer ranges. However, for its very fastest flatbed, the HS 100 Pro, LEDs alone are not powerful enough. Instead they are used in a hybrid curing system, where the LED are mounted on the head carriage and pin the ink immediately after printing to keep the dots sharp, while more powerful mercury lamps perform the full cure.
The EFI VUTEk HS100 high speed flatbed uses a mix of LED and mercury lamps to cope with high throughput
Varying the relative timing of the two lamp sets allows EFI to vary the adhesion and gloss levels of the inks.
At FESPA Digital in Munich this year Mutoh introduced three new printers with UV-LED lamps.
These are the compact 24 inch ValueJet 628, the more conventional ValueJet 1626UH for rigid and roll materials. The third is a new "desktop" A3 format flatbed, the ValueJet 426UF, to rival Mimaki's UJF-3042/6042 family and Roland' LEF-12 and LEF-20 small flatbeds, which also use LED lamps.
What they don't work for
The initial build cost of very large, high output LED arrays means they're not yet suitable to the very fastest UV flatbed presses such as the biggest HP FB machines or Inca Onsets, or to full-width arrays on solvent-UV hybrid ink presses.
However, given the increasing power outputs and falling prices of UV-LED over recent years, it seems inevitable that this trend will continue to the point where it's affordable to replace mercury vapour on all new printers within a few years.
So far LEDs aren't cost-effective for full-width arrays either. This prevents them being used in the solvent-UV hybrid ink printers that are currently being shipped by Mimaki (the JV400SUV), Fujifilm (Vybrant F1600) and Colorific (which sells conversion kits for Roland, Mimaki and Mutoh eco-solvent printers).
In this case a small amount of solvent is used in the ink, which flashes off on the printer bed to pin the ink, which is then cured by a full-width UV lamp array about 60 cm downstream from the print carriage. A 40 to 60 inch LED array would cost a fortune.
However, a lower UV light output is needed than for the lamps used on scanning print carriages (which need to transfer more energy as they only illuminate a small area as the carriage passes over it), so light pressure UV tubes can be used. These use less power than mercury lamps, and generate less heat with no ozone.
Visible and wireless futures
Although not directly relevant to UV presses, visible wavelength LEDs are seeing more and more use for general lighting, including printing factories. It's likely they will gradually replace conventional incandescent and fluorescent lamps for room and exterior lighting over the next decade.
They not only have the power saving, cool running and longevity benefits discussed above, but by building them in RGB colour clusters it's possible to vary the colour output. Ultimately LEDs may be built into glowing wall and ceiling panels so that conventional bulb or strip lamps may disappear completely.
Today's LED lamps fit into standard light bulb sockets,. Right now they are much more expensive than the energy-saving fluorescent lamps that have become common across Europe in the past few years. However, prices will fall as adoption rates go up, while their lower power consumption and longer life will make them popular with users. Unlike energy-saving 'CFR' (Compact Fluorescent Reflector) lamps, which contain mercury, there's less of an end-of-life disposal problem with LEDs too.
Bright white LEDs are an increasingly familiar sight as running lights on cars, and are just starting to be offered as main headlamps too, though they cost more than even gas discharge headlamps today.
There's a computing aspect too. LEDs are currently being developed into a form of wireless data transmission system, called Li-Fi. This could be built into LED lamp units in future and works by switching the LEDs on and off thousands of times per second, so the eye doesn't notice. It has the potential for very much higher bandwidths than today's radio-frequency Wi-Fi.
Summary
So, LEDs sit neatly at a cross-roads. They are becoming increasingly cost effective on some printers, while larger platforms are not quite there.
There are still costs to bear in converting your curing systems, but the savings you can make in bulb-life alone will pay for the investment quickly and you improve your environmental performance while saving money on electricity.
If you want to invest in a more profitable future, the scales are tipping towards LED curing - and supported by savings which help the bottom line as well as the environment, that makes it an obvious choice for any printer.
Topics
Interested in joining our community?
Enquire today about joining your local FESPA Association or FESPA Direct
Recent news

What are the opportunities for printers regarding backlit displays and window graphics?
Nessan Cleary describes the various opportunities for printers regarding window graphics. There is a wide range of materials and lighting options available.
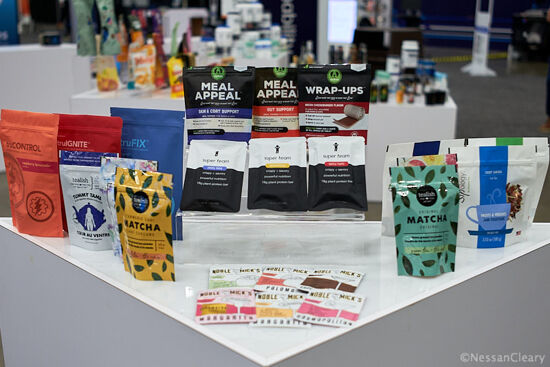
What is the difference between labels and packaging regarding narrow web printing?
Nessan Cleary shares how labelling has always been distinct from packaging but increasingly lines are becoming blurred between them.