Textile printing technologies for next generation, Northumbria University invest in the hp stitch
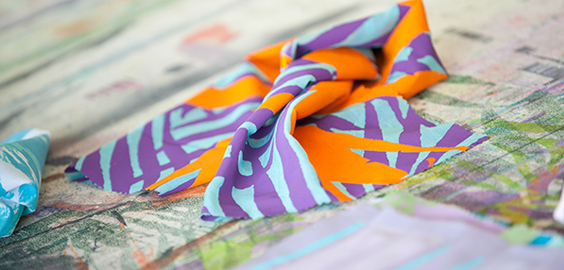.jpg?width=750)
As the Textile industry shifts to a digital future the technologies and software that will facilitate this seismic shift are of critical importance to the education of a new generation of design and print practitioners. Practical experience is an essential learning tool - it is the bedrock of all teaching and both inspires and generates new applications that push the boundaries of creativity.
Kenny Macrae is the principle technician for Fashion and Textiles at Northumbria University. As a designer himself his knowledge of both design, textiles and print is extensive - as is his passion for education.
In this Interview we talk through the application of digital technologies, the new HP Stitch print machine, and importantly how such access to digital equipment will educate the next generation to deliver a vibrant, creative and sustainable textile industry in the years ahead.
Listen to the podcast here.
The Textile department at Northumbria University recently invested in the HP Stitch Dye Sublimation print technology to further expand its digital printing capabilities. The university has a suite of digital textile printing machinery alongside cutting technologies and supporting software with which the students can design, develop and create textiles across multiple departments. Dye sublimation is a huge growth sector and enables greater variance of application – as essential in a learning facility as it is in a live production environment.
When did the Northumbria university first adopt digital technologies?
We run courses that are known for their vocational & practise-based learning. As long as I’ve been here, we have looked to use and integrate digital technology and techniques to sit alongside more traditional skills, from digital illustration, pattern cutting & our recently upgrade Mimaki TX3 fabric printer to exploring the use of laser cutters and 3D printing and digital weaving within fashion. We always encourage the students to be as creative in their use of technology and technique as possible without losing any of our core teaching and skills.
Why did you choose the HP Stitch - What were the important attributes?
We worked closely with our supplier RA Smart to ensure we got the best machine for the job, as technology moves so quickly it was important that we got not only best value for money but a machine that we would give us a reasonable period of service before we need to upgrade. We took advantage of their offer of a visit to their showroom to see the machines in action and help us make our decision.
The Stitch is such an instinctive machine to use. Full width, front loading and with an easy to follow control panel. Combined with full width garment press we already run (alongside smaller sample machines) and with a RIP that is almost identical to the other ones currently in use within the department it made the switch the obvious choice.
How will the machine be utilised - what’s your academic vision?
The original idea behind the machine was to help support our new MA in performance and sports fashion as the inks lend themselves to use with modern synthetic fabrics. We are also seeing an increasing number of undergraduate students wanting to do swimwear and lingerie as part of the degree collections so again this machine should be ideal. Given the current situation the machine is ideal for potential blended learning as well, allowing students to send in work digitally and for technicians to print their designs out and send back to them with minimal fuss or waste of resources.
Will the students have direct access to the machine?
Although run by a trained technician the machine will be accessible to all students across all courses and year groups to utilise where appropriate.
Do you intend to print using both transfer paper and direct to fabric and how will that benefit the students?
Initially we will only run it with transfer paper particularly at an undergraduate level to allow then to easily produce quick full colour samples. As we gain experience, we will explore direct to fabric applications.
Do the students calibrate their screens for best practice colour management?
The students will use appropriate colour profiles, but we don’t as yet run any colour management software. Again, as our experience grows, we will explore the HP Stitches inbuilt colour management technology.
What fabrics will be available?
The majority of fabric will be your standard sublimation bases. However we encourage experimentation and you will find final year and post graduate students using a lot of different fabrics to see what effects they can achieve, this is particularly relevant within our performance and sustainability MA where students have the possibility of using the digital loom to create their own mixed fibre bases.
How important was sustainability in your decision when choosing the HP Stitch machine?
I’m not sure if it was a consideration in terms of the machine itself but it terms of what it provides, less wastage of inks, using less water and power than more traditional methods, more precise sampling etc then it’s ideal across the board especially within the context of the sustainability MA course.
Which software suites do you teach for fashion?
Currently students are all taught the standard design packages Photoshop, Illustrator etc. Specialist post graduate students will be taught more specific programmes depending on need.
Which courses will have access to the machine? How will it help you prep the students for employment?
Effectively it can be used by anyone within the university although aimed specifically at design and fashion students. There will be applications for its use from the whole of the school of design; Fashion, Interiors, 3D, Graphics - the possibilities are endless. We have worked in conjunction with other depts with joint projects in the past where its use would have been ideal, and I have no doubt these will continue in the future.
We think its vitally important that students understand not only the design process but the equipment used to realise their ideas, while the may never directly use the machine itself again the understanding of what it is and what it can do will always be invaluable as the move forward with their careers.
In summary - Investing in new technologies is essential if we are to truly educate a digital generation. Digital textiles offer the designer unlimited creativity and the textile industry a sustainable platform for future production. The digital print industry offers graduates an innovative, highly technical environment and infinite career opportunities.
The future of design, print and manufacturing is smart, efficient and agile – for print to thrive we must invest in the education sector, share emerging technologies, expert knowledge and encourage industry collaboration as an imperative if we are to inspire a new generation of design and print practitioners. We look forward to following the progress and creativity unleashed by the HP Stitch at Northumbria University.
Interested in joining our community?
Enquire today about joining your local FESPA Association or FESPA Direct
Recent news
.png?width=550)
FESPA Middle East 2025 Overall Highlights
It has already been 2 weeks since we opened the doors on the 2nd edition of FESPA Middle East.
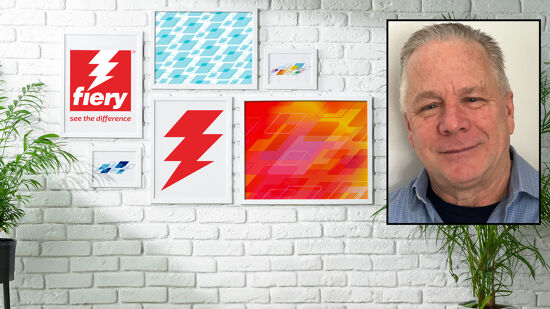
How will Fiery simplify print processes and enhance their user experience
In this podcast, Debbie McKeegan interviews Michael Chramtchenko, Chief of Staff, Sales and Marketing at Fiery, discussing the company's innovative software solutions for the print industry, particularly in garment decoration.
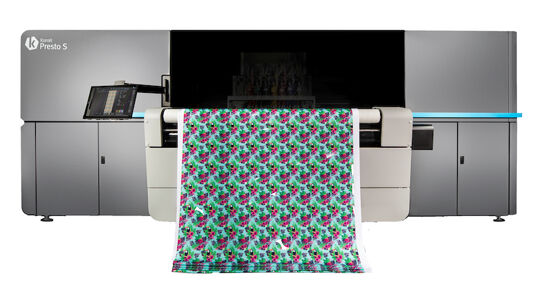
What is digital textile printing and what are the opportunities?
Nessan Cleary shares how textile printing covers a wide range of different market sectors which vary in opportunities. Nessan discusses sportswear, direct to garment and home décor.
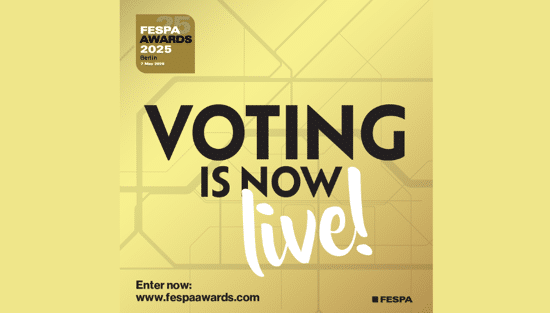
Vote now for the FESPA Awards’ People’s Choice Award!
The voting for the prestigious People's Choice FESPA Award is now open until 7th February where those in the industry have the opportunity to vote for their favourite entries, celebrating the exceptional talent in the industry.