How to print 3D with a UV digital inkjet
Simon Eccles gives full marks to the UV inkjet community for turning what was originally an unwanted side effect into a valuable creative feature.
The original photopolymer UV inks cured so quickly that they didn’t have time to spread out and form a thin film, so the image areas stood proud of the media. Coarser halftones looked and felt like sandpaper.
Over the years the ink formulations have been refined and techniques such as pinning have reduced this effect to the point that the smarter curing systems can be used to vary the smoothness level between high gloss and matt within the same image.
However, those sandpaper images can be a definite advantage if you exaggerate them. Because UV ink can be cured instantly after printing, it’s relatively easy to print on the same spot to build up layer on layer, giving a raised image that’s obvious to both the eye and to the fingers.
“The raised nature of a UV print - be it clear or process - has allowed tactile signage, or packaging proofs that require a Braille element or any decorative 3D effect to be created by simply printing multiple layers of ink in register,” said Duncan Jefferies, marketing manager for Mimaki’s UK agent Hybrid Services.
Rather like metallic effects, this raised imaging adds perceived value to the print, as the embossed appearance is associated with quality. As we also pointed out, combining metallics with raised ink simulates foil blocking, again a high value effect.
“Raised imaging gives a new effect,” pointed out Nick Decock, commercial marketing manager of Mutoh Europe in Ostend. “The luxury finish is certainly something printers are looking for, as it lets them charge a lot more than for regular work like posters and banners. It can be used for special effects, trophies, prototype packs and cartons - there are lots of possibilities.”
In theory any UV inkjet with a scanning head can do this, providing the Rip and controller are built that way. However, Roland DG was the first to make a big marketing point with this ability in 2008, when it introduced its first VersaUV printer-cutter, the 30 inch roll-fed LEC-300. This was replaced by the faster LEC-330 and the even faster and wider 54 inch LEC-540. It can build up layers of clear ink to form a pattern embossed effect, or it can create textures by using a greyscale image in the artwork file, where dark is “low (ie fewer layers) and white is high (more layers).
This packaging sample with embossed effects was produced on a Roland VersaUV inkjet
The raised layers are set up and controlled by the Rip, in this case Roland’s own VersaRIP which is bundled with all of its printers. Setting up is similar to creating a cutting path for the printer-cutters – a specially named layer is created in the original image file (which is most likely a PDF), which is then detected by the Rip and assigned to the clear ink.
Mimaki shows off different texture effects using black UV cured ink
According to Jefferies, Mimaki has been able to produced raised images singe the mid-2000s, although it has never made such a big thing of it as Roland did in 2008. The process is exactly the same as Roland’s building up multiple layers of ink by curing each layer.
The Mimaki RasterLink RIP software enables up to nine layers to be printed automatically to create the raised effect. It claims this requires minimal operator intervention or indeed file setup. By using a greyscale ‘height map’ for the clear layers, variable textures and domed effects can be created. Mimaki’s UV printers range from the small UJF 3042 and 3062 flatbeds to the medium-sized UJV-160 and UJV-500 LED-cured roll/flatbed models, to the big JFX-200 and JFX-500 flatbeds.
Mutoh, another of the Japanese wide format manufacturers, is mainly promoting its new generation of LED-cured UV printers. Decock said that both these are suited to raised imaging through the company’s own Rips. In Europe these are the new small A3 flatbed ValueJet 246UF and the 64 inch ValueJet rigid/roll 1626UH. However, the older UV printers can produce raised images as well.
Decock added that Mutoh offers a unique Layer Editor program, running in Windows. This can control the raised imaging layers and also allows white to be sandwiched between two sets of colour images for printing on glass or clear plastic.
Third party Rips can often control textured layers too. Caldera is one of them, for instance. “We do the same thing as Roland in our RIP – greyscale height map for the clear ink layers, where lighter toners are higher, and darker tones are lower,” said Sebastien Hanssens, vp marketing and communications for the French Rip maker. “We also do that on high end machines such as Swiss Q.”
A handful of sheet fed inkjets are purpose built to offer raised and textured effects, but they are aimed more at the sheetfed commercial print sector than wide format. Scodix was the first to do this, launching its first Scodix1200 B2 format printer at Ipex 2010 and since expanding the range into B3 and faster models.
MGI followed up its original 2008 JetVarnish B2 UV spot varnishing inkjet with the JetVarnish3D at drupa 2012. As you’d expect, 3D means raised and textured imaging, and, with the option iFoil system, metallic foil can be applied over the embossed effects too. They were joined this year by Komfi with the launch of its second generation inkjet UV varnisher, the Spotmatic 54, which can build up multiple layers to form textures.
An exciting use of raised imaging from any process is Braille lettering for visually impaired people. With large format inkjets this is mainly relevant to signage. However raised imaging for book and brochure work is possible with a handful of smaller format digital production presses, notably the Kodak NexPress SX series and recent HP Indigos, as well as the B2 and B3 format raised spot UV varnish printers made by Komfi, MGI and Scodix.
Mimaki produced this sample of Braille on signage, building up multiple layers of black UV-cured ink
This idea has sometimes been extended into the creative sphere, with raised imaging used for illustrations in Braille books as well as museum and gallery signage and descriptive labels. Using a digital print technology makes this possible for one-offs, temporary signage or short runs at low cost, compared to using metal dies to emboss the images.
Although most people will think of print as a planographic process, meaning its images are flat, metal dies have been used for centuries to add a 3D element to the surface.
Digital printing can now emulate that in ways that would be technically impossible, or too expensive for traditional dies, with the added benefit that there are almost no preparation costs, no special presses, and every copy can be different. The creative potential of raised print is on the up and up.
Topics
Interested in joining our community?
Enquire today about joining your local FESPA Association or FESPA Direct
Recent news
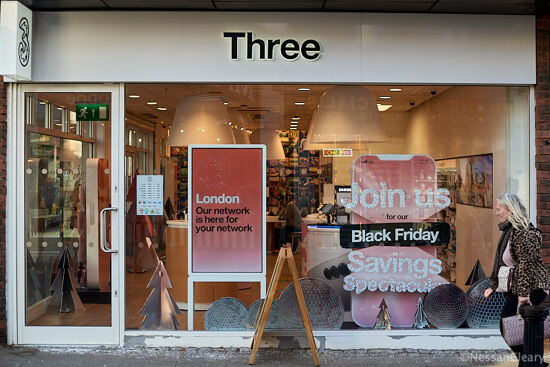
Are digital screens for interior displays a challenge for printers?
Nessan Cleary discusses how the increased popularity of using digital screens for interior displays may pose a challenge for printers. Nessan states there are numerous sustainable options for prints designed for interior spaces.
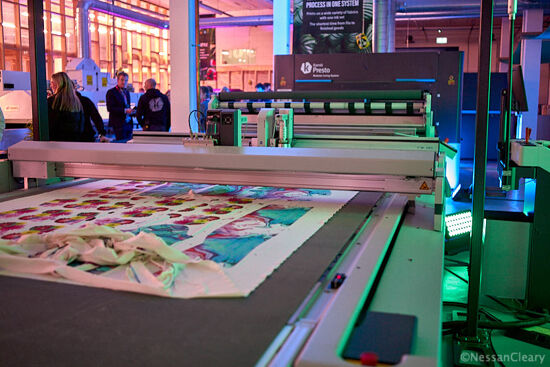
How the success of digital textile printing is reliant on advances in finishing
Nessan Cleary shares how the success of digital textile printing is dependent on the advances in finishing for textile production. The level of automation is a contributing factor to the efficiency of localised production and a more sustainable approach.
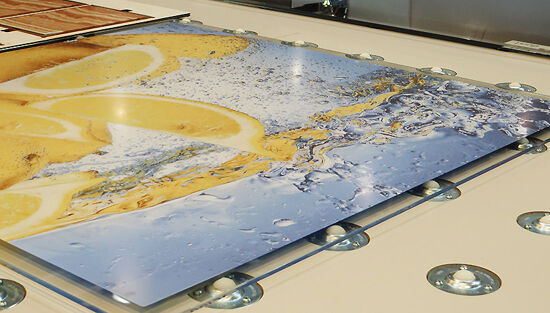
What are the pros and cons of inkjet printing?
As a growth segment in digital printing, Industrial Inkjet (IIJ) is still a popular technology. Sonja Angerer discusses the technologies, the advantages and disadvantages of industrial inkjet and the market opportunities for print shops in IIJ.