Auf dem Weg zu mehr Nachhaltigkeit bei Drucksubstraten
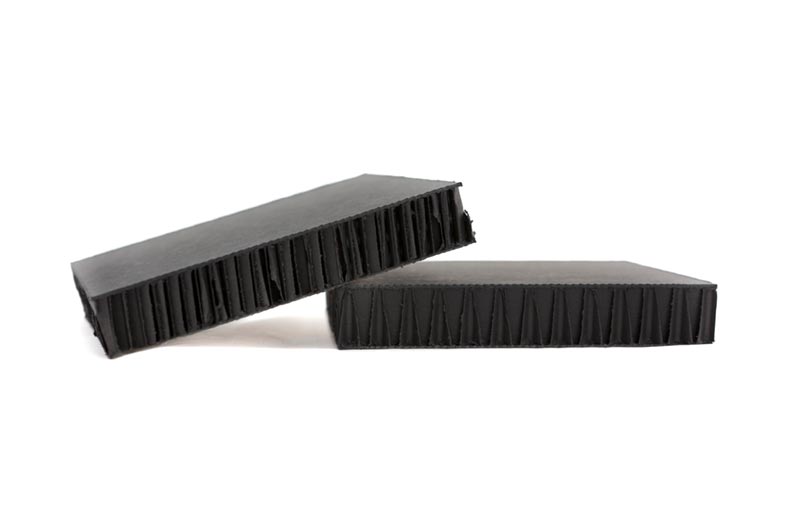.jpg?width=750)
Sonja Angerer erläutert, dass viele digital gedruckte Produkte schwer zu recyceln seien, Hersteller von Substraten jedoch derzeit an geeigneten Lösungen arbeiten.
Die Europäische Union strebt eine Kreislaufwirtschaft an, in der möglichst viel Abfall recycelt wird. Für digitale Druckanwendungen ist dies jedoch noch nicht ganz realisierbar. Die Hersteller von Drucksubstraten arbeiten fleißig an Lösungen. Jetzt liegt es an den Druckern und ihren Kunden.
Nach jeder Messe, jeder POS-Aktion muss der gesamte anfallende Müll entsorgt werden. Zwar lassen sich bestimmte Materialien wie Papier oder Glas relativ einfach sortieren und recyceln. Leider gilt dies jedoch nicht für die meisten Bedruckstoffe, die im Digitaldruck verwendet werden.
Bildunterschrift: Recycling ist bei vielen digital gedruckten Produkten ein Problem. Doch es gibt bereits Initiativen, die das ändern wollen. Foto: S. Angerer
Warum gibt es für viele Digitaldruckanwendungen nicht viele Recyclingmöglichkeiten?
Um zu verstehen, warum Digitaldruckanwendungen oft schwer zu recyceln sind, ist es wichtig zu verstehen, was in der Europäischen Union normalerweise mit Gewerbe- und Siedlungsabfällen passiert:
- Mülldeponie
- Energierückgewinnung bei der Müllverbrennung
- Recycling zu einem neuen Rohstoff
Jeder, der die Richtlinien zur Hausmüllsammlung der deutschen Kommunen kennt, weiß zum Beispiel, den Joghurtbecher getrennt von seinem Aluminiumdeckel zu entsorgen. Mit dieser Kombination „Kunststofftopf mit Alu-Deckel“ lassen sich zwei sortierte Sekundärmaterialien herstellen.
Leider lassen sich Produkte wie laminierte Pop-up-Displays oder auf Aluminiumblechen befestigte Drucke nicht so einfach trennen. Sie bleiben ein Verbundwerkstoff und eignen sich nicht für die Wiedereinführung in den Stoffkreislauf.
Es muss jedoch nicht so sein. In der Automobilindustrie besteht seit der Altfahrzeugrichtlinie im Jahr 2015 das Ziel, eine Recyclingquote von 95 Gewichtsprozent zu erreichen. Dadurch gibt es bereits eine ganze Reihe mehrfach verwendbarer Rohstoffe aus der Automobilherstellung und dem Recycling.
Digitale Druckmedien aus recycelten Materialien
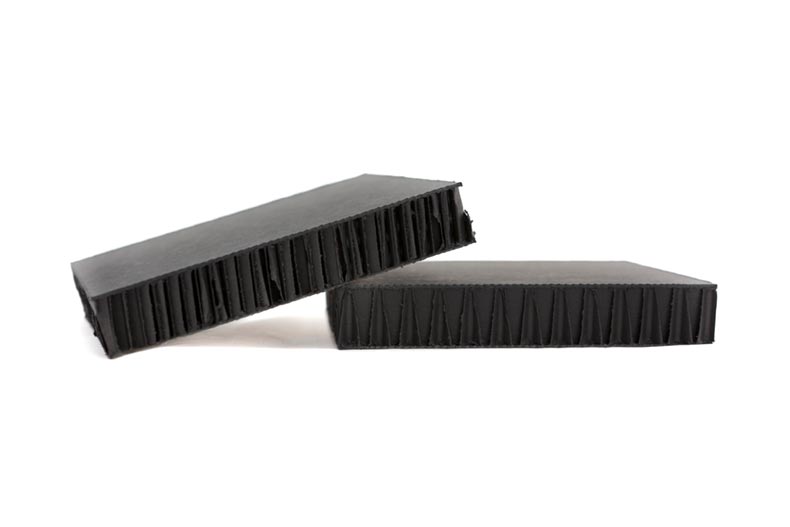
Bildunterschrift: Re-Board (im Bild) und andere Wabenplatten werden aus nachwachsenden Rohstoffen hergestellt. Foto von : Re-board.
Der Digitaldruck erfordert hochwertigere Substrate als herkömmliche Druckverfahren. Dadurch ist es gelungen, eine sehr geringe Menge an Medien anzubieten, die aus teilweise oder vollständig recyceltem Material hergestellt werden können.
Eine kleine Ausnahme bilden Wabenplatten und andere papierbasierte Bedruckstoffe. Die europaweite Recyclingquote für Papier lag im Jahr 2015 bereits bei 71,5 %. Doch auch bei Re-Board , dem wohl bekanntesten Wabenkarton, der in der Druckindustrie verwendet wird, muss ein Teil des bedruckbaren Liners mit einem sehr hohen Anteil selbst hergestellt werden aus frischen Fasern. Nur so kann eine erstklassige Druckqualität gewährleistet werden.
Verseidag-Indutex, seit August 2020 Teil der Serge Ferrari-Gruppe, hat nun Vertex entwickelt, eine Beschichtung, die aus Post-Consumer-Abfällen der Automobilindustrie hergestellt wird. Das Ergebnis ist eine Beschichtung, die frei von PVC ist, aber auch aus bereits recyceltem Material hergestellt wird. Dies ist eine große Innovation für die Digitaldruckindustrie. Vertex soll die Grundlage einer ganzen Produktlinie von Drucksubstraten für den Innen- und Außenbereich bilden. Das Sortiment deckt alle gängigen Digitaldruckanwendungen ab und ist für HP Latex- und UV-härtende Tinten optimiert. „Wir raten bewusst von Eco-Solvent- und anderen Solvent-Tinten für Vertex-beschichtete Materialien ab“, sagt Stefan Altgassen, Director Business Unit Large-Format Printing bei Verseidag-Indutex. „Im Rahmen eines umweltbewussten Druckkonzepts wäre das jedenfalls nicht sinnvoll.“
Derzeit laufen umfangreiche Tests mit Beta-Nutzern. Verseidag-Indutex geht davon aus, dass die ersten Produkte der Vertex-Reihe bis Mitte 2021 auf den Markt kommen. „Ziel ist es, Mesh- und Bannermaterialien für aktuelle Digitaldruckanwendungen zu entwickeln“, erklärt Peter Michael Siemens, Leiter Entwicklung & Innovation. „Bei Bedarf erfüllen diese auch die aktuellen deutschen, französischen und europäischen Brandschutznormen.“
Wie alle anderen Gewebe- und Obermaterialmaterialien für den Großformatdruck verfügen auch die Vertex-Produkte über einen textilen Kern aus gewebtem Polyester. Derzeit werden konventionelle Garne verwendet, da die Marktpreise für recycelte Garne viel höher sind. Laut Markus Simon, CEO von Verseidag-Indutex, plant das Unternehmen jedoch, „auch für dieses Problem eine Lösung innerhalb der Serge Ferrari-Gruppe zu finden“. Der Konzern verfügt über eine eigene Garnspinnerei in der Schweiz.
Recycling und CO2-Fußabdruck
Auch bei der Sortierung von Abfallstoffen gibt es große Unterschiede hinsichtlich ihrer Eignung für das Recycling. PVC gilt immer noch als schwer zu recyceln. In vielen Ländern wird entsorgtes PCV daher auf Deponien gelagert oder in Müllverbrennungsanlagen in Energie umgewandelt. Letzteres mag auf den ersten Blick eine schlechte Idee sein, aber tatsächlich ist der Energiewert von PVC in etwa mit dem von Braunkohle vergleichbar. Als Unternehmen mit mehreren Produktbereichen, unter anderem für textile Architektur und temporäre Bauten, ist Verseidag-Indutex Mitglied der Brancheninitiative VinylPlus , die sich für ein verstärktes Recycling von PVC als Rohstoff für neue Produkte einsetzt.
Andere Hersteller von Drucksubstraten konzentrieren sich ausschließlich auf PVC-freie Alternativen ohne den Einsatz von Recyclingmaterialien oder nachgelagerte Recyclingansätze. Im September 2020 stellte Heytex beispielsweise seine Ecotex-Produkte vor. Diese gelten in Nordeuropa als haltbar für etwa ein Jahr unter Außenbedingungen. Da sie leichter als PVC-Produkte mit ähnlichen Leistungsdaten sind, lassen sie sich leichter transportieren und können so zu einem geringeren CO2-Fußabdruck beitragen.
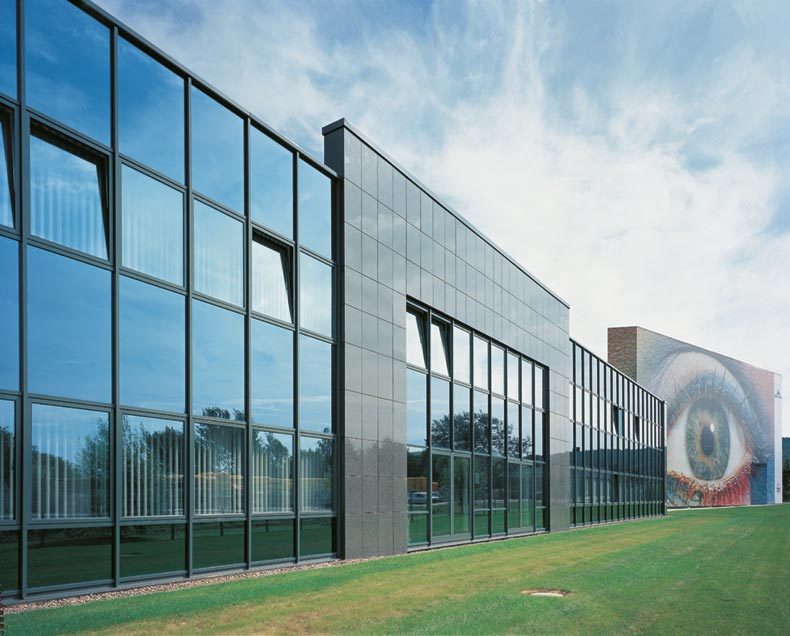
Bildunterschrift: Neschen hat kürzlich sein Portfolio an PVC-freien Produkten erweitert. Im Bild: die Neschen-Zentrale in Bückeburg. Foto: Neschen
Im November stellte Neschen sein Easy Dot-Portfolio vor, eine neue selbstklebende Mattfolie. Die Folie wird ohne PVC und ohne Lösungsmittel hergestellt, da die Klebepunkte wasserbasiert sind. Die Folie selbst besteht aus Polypropylen, kurz PP. Allerdings ist die Herstellung von PP, einer in der Druckindustrie weit verbreiteten Alternative zu PVC, besonders energieintensiv. Darüber hinaus sind die Leistungsdaten für PP-Medien für den Außenbereich deutlich schlechter als für PVC. Das bedeutet, dass ein Druck unter Umständen mehrmals ausgetauscht werden muss, was zu größeren Materialmengen führt. Während PP als besonders recyclingfähig gilt, lag die tatsächliche Recyclingquote im Jahr 2017 bei weniger als einem Prozent . Dies ist der niedrigste Wert aller weitverbreiteten Kunststoffe.
Daher ist es schwierig, einen ökologischen Fußabdruck für verschiedene Drucksubstrate zu ermitteln. Re-board veröffentlichte für seine Produkte eine Berechnung mit Berechnungen auf Basis der CEPI- und ISO 14040-Spezifikationen. Für die Berechnung des ökologischen Fußabdrucks ist die Energiequelle zur Herstellung des Druckträgers von großer Bedeutung. Bei Verseidag-Indutex wurden Produktion und Verwaltung Mitte 2020 durch eine neue, leistungsstarke Photovoltaikanlage und den Einsatz von zertifiziertem Ökostrom weitgehend CO2-neutral. Der Rest wird mit Zertifikaten ausgeglichen.
Die meisten Hersteller von Folien und Substraten für die Druckindustrie haben Initiativen gestartet, um die Auswirkungen ihrer Produkte auf die Umwelt zu minimieren. Beispielsweise konnten bei Avery Dennison durch verschiedene Maßnahmen die Treibhausgasemissionen um 8.000 Tonnen reduziert werden.
Es ist jedoch wichtig zu verstehen, dass etwaige Verbesserungen seitens des Herstellers nur Auswirkungen auf die Produktion des Druckträgers haben können. Ein „zusätzliches Extra“ sind Emissionen, die während des Lebenszyklus des Materials entstehen, beispielsweise durch Vertrieb, Logistik, Verarbeitung, Installation und sogar den Recyclingprozess.
Wie können digitale Druckprodukte umweltfreundlicher werden?
Aber es gibt einige Dinge, die Digitaldrucker tun können, um die Auswirkungen ihrer Produkte auf die Umwelt zu minimieren. Es beginnt bereits in der Entwurfsphase:
- Auswahl geeigneter Materialien
- Vermeidung der Herstellung zusammengesetzter Produkte, beispielsweise durch Laminieren
- Entwicklung von Anwendungen, die weniger Material erfordern
- Effizienter Maschinenpark
- Effizienter Arbeitsablauf mit wenig Ausschuss und wenig Abfall
- Nutzung umweltfreundlicher Energiequellen (Wärmepumpe, Solaranlage, Ökostrom etc.)
Allerdings kann eine Maßnahme nur dann erfolgreich sein, wenn die Konsumenten von Printprodukten ihren Beitrag leisten. Lippenbekenntnisse reichen nicht aus; Sie müssen bereit sein, ihren Anteil am Preisaufschlag für umweltfreundlichere Substrate und mehr Recycling zu übernehmen. Es ist eine große und wichtige Aufgabe von Digitaldruckern, ihre Kunden zu überzeugen. Denn eines haben wir in den letzten Monaten gelernt: Wir schaffen das nur gemeinsam.
Sind Sie daran interessiert, unserer Community beizutreten?
Erkundigen Sie sich noch heute über den Beitritt zu Ihrer örtlichen FESPA-Vereinigung oder FESPA Direct
Jüngste Neuigkeiten
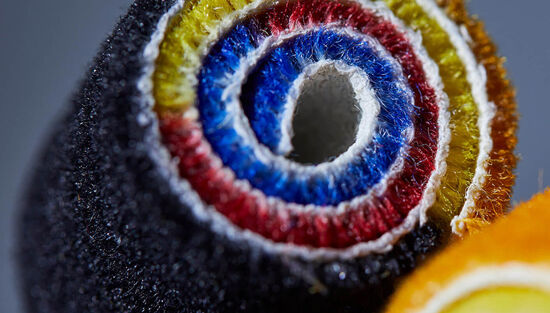
Teppich, Decken und Frottee: Textildruck auf Hochfloor
Ob in Privathaushalten oder für das Gastgewerbe, Bodenbeläge und Heimtextilien nach Kundenwunsch oder in kleinen Serien sind stark nachgefragt. Doch Teppich-Druck und die Herstellung anderer Hochfloor-Produkte erfordern ganz spezielle Technologien.
.png?width=550)
Allgemeine Highlights der FESPA Middle East 2025
Es sind bereits 2 Wochen vergangen, seit wir die Türen zur 2. Ausgabe der FESPA Middle East geöffnet haben.
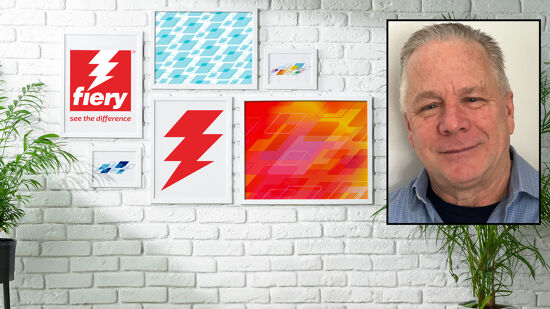
Wie wird Fiery Druckprozesse vereinfachen und das Benutzererlebnis verbessern?
In diesem Podcast interviewt Debbie McKeegan Michael Chramtchenko, Stabschef für Vertrieb und Marketing bei Fiery, und spricht über die innovativen Softwarelösungen des Unternehmens für die Druckindustrie, insbesondere für die Textilveredelung.
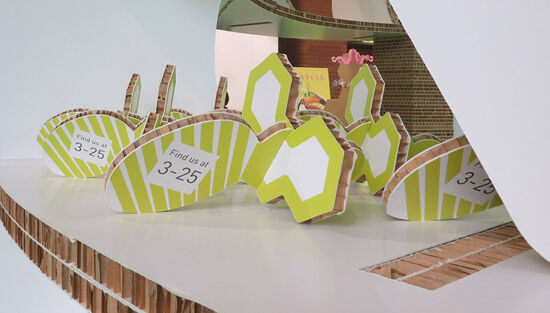
Kartonplatten für LFP richtig nutzen
Kartonplatten und andere Bedruckstoffe aus nachwachsenden Rohstoffen gelten als PVC-freie und umweltfreundliche Alternative für Beschilderung, Messebau und Poster. Bei der Verarbeitung muss man sich jedoch auf die Besonderheiten des Materials einstellen. Hier sind 5 Tipps für gute Ergebnisse.